How construction change is spearheading move to zero carbon
02 September 2021
The pace of change and innovation in construction is accelerating sharply as the industry searches for the best routes to zero carbon dioxide and a more sustainable future. Graham Anderson and Alex Dahm report.
Construction site equipment users and heavy transport companies are experimenting with alternatives to diesel fuel in response to client demand and tightening air quality regulations around the world.
What is already clear is that the market will fragment, with different solutions adopted according to equipment type, project needs and the availability of resources. A large number of wide-ranging and ambitious schemes is bringing together OEMs, university academics, technology experts, energy companies and environmentalists in an exciting mix.
Many in the industry also worry about how to reduce the environmental impact of older and other diesel-fuelled equipment likely to be around for many years to come.
Environmental impact
Jan Sarens, equipment trading director at Sarens, the Belgium-based international heavy lift and transport company, explains the dilemma. “In terms of carbon neutrality, we have to ask whether the mass adoption of new equipment models, whether electric or hydrogen, will be good for the environment.
“Cranes have a much longer working life than a car, for example, and replacing our old cranes with new ones might easily be negative in terms of CO2 emissions when the entire manufacturing process is taken into account.”
This issue is likely to mean construction adopts a two-pronged approach on the road to zero carbon dioxide – using alternative fuels in existing equipment to reduce the impact of diesel in the short term while developing new ranges of equipment and solutions.
For some time now, crane and transport companies, for example, Sarens and Mammoet have been developing their use of HVO – or hydrotreated vegetable oil – as a diesel substitute.
In the field
At the smaller end of the market, the MHM Group in the UK told its customers all the company’s diesel-powered machinery – mainly generators and lighting towers – is fully compatible with HVO fuel, saying tests have shown HVO provides not just cleaner combustion but also better starting and a reduced chance of waxing and water retention in extreme temperatures.
Jan Sarens continues, “More and more users are asking for HVO fuel, driven in part by local regulations such as low carbon zones in urban areas.”
Finnish company Neste is one of the main global producers of HVO, which is a second-generation biofuel primarily made from renewables such as used cooking oil and animal fats from food industry waste. It has a chemical structure almost identical to regular fossil diesel and can be used as a “drop-in” substitute, cutting emissions by up to 90 %.
The company also stresses it is different from – and, it says, better than – traditional biodiesel (also known as FAME, or Fatty Acid Methyl Ester), as it burns more efficiently, produces lower emissions and has better cold and storage properties.
Environmentalists have raised questions about the use of waste from the palm oil industry in HVO production, although the HVO producers insist they are addressing this.
Certainly, HVO’s rise and increasing acceptance has contrasted sharply with the growing environmental concerns around other biofuels primarily sourced from crops such as maize, with many questioning their green credentials, arguing they can lead to deforestation and the loss of valuable land for food production.
High speed change
But while industry searches for ways to reduce the environmental impact of the existing stock of diesel engines and over the lifetime of the machines they power, OEMs are accelerating investment in innovations and new types of equipment.
The speed of change was underlined at the end of July when construction equipment maker JCB went public on its work to develop a hydrogen combustion engine and the thinking behind its current strategy.
Challenged by JCB chairman Lord Bamford to develop a zero-carbon dioxide hydrogen motor, the company established a specialist development team at its Power Systems factory in Derbyshire, UK.
JCB had already launched an electric mini excavator and today has fourteen models in its compact equipment range powered electrically via lithium-ion batteries, including telescopic handlers, scissor lifts, dumpers and forklifts. But its engineers argued batteries are not practical for equipment with an operating weight of more than 6 tonnes, for example, backhoe loaders and large excavators.
Quite simply, batteries would be too expensive and weigh too much and result in loss of performance, the group found.
The company then turned its attention to hydrogen, initially to hydrogen fuel cells, using the technology to develop a 20 tonne tracked excavator.
In a fuel cell, hydrogen and oxygen are combined to generate electricity, heat, and water.
Fuel cells using pure hydrogen fuel are completely carbon-free, with their only by-products being electricity, heat, and water. Some types of fuel cell systems can use hydrocarbon fuels, for example, natural gas, biogas, methanol, and others.
Fuel cells are already used today in a range of applications but concerns about cost and security of supply prompted moves to develop a hydrogen combustion engine which JCB now regards as having significant advantages.

Lord Bamford says, “While there is much discussion about the merits of using battery and fuel cell technology in machinery, we believe that the use of hydrogen motors will provide the quickest way to reach the target of zero carbon dioxide emissions, especially from high use, high energy equipment.”
He adds, “We believe there should be continued use and development of internal combustion engine (ICE) technology; the use of fossil fuels may be phased out in the future, but that shouldn’t mean that ICEs don’t have an important ongoing role in helping to reach zero carbon dioxide emissions.”
Simple combustion
JCB believes the great advantages of hydrogen combustion are its simplicity, the fact that it is relatively inexpensive – the fuel costs will be similar to diesel – and can be integrated into all forms of powertrain. It is, said one engineer, a “plug and play” solution.
Others are going down a similar path, notably engine manufacturer Cummins which has started testing a hydrogen combustion engine of its own and, like JCB, has been delighted with the progress the technology has made so far.
Srikanth Padmanabhan, Cummins Engine Business president, said, “Cummins is thrilled about the potential of the hydrogen engine... we are optimistic about bringing this solution to market.”
Manufacturer Liebherr’s components division is working on direct injection for hydrogen so it can be used to fuel internal combustion engines, as reported in ICST August 2020.
While prospects for hydrogen combustion are exciting Liebherr, Cummins and JCB, for other OEMs batteries and fuel cells remain a good bet.
Hyundai unveiled a hydrogen fuel cell powered forklift drawing on its expertise in the automotive industry. The forklift – in the mid- to large-size range – can lift up to five tonnes and operate for five hours when its fuel cell is fully charged. Trials are continuing with the aim of bringing it to market in 2023 and, the company says, it now working on a prototype of a hydrogen fuel cell excavator.

In China, crane and equipment manufacturer Sany has announced it is developing a range of construction vehicles using fuel cell technology, including a dump truck and a cement mixer the company claims is the first of its kind in the world.
At the same time, the number of electric cranes is steadily increasing. Small industrial cranes have been available with battery power for more than a century but larger models have never been deemed practical until now.
In mid-2020 Zoomlion announced a fully battery electric 25 tonne capacity wheeled mobile crane and later in the same year Liebherr announced its new battery-electric crawler cranes – the 220 tonne capacity LR 1200.1 unplugged and the 250 tonne capacity LR 1250.1 unplugged. Spierings Mobile Cranes has been developing battery and hybrid options for its mobile cranes since its first City Boy model made its debut in 2010.
This year we have had Dutch company PVE announce a full series of battery-electric crawler cranes (see ICST February 2021).
On the move
In the transport sector manufacturers Scheuerle, Cometto and Goldhofer are all working on or have already launched electrically powered modular transporters. Volvo, Daimler Truck and Traton Group are working together on plans to install a high performance battery charging network in Europe for heavy transport. At the same time, both truck manufacturers, among others, have also developed battery-electric heavy trucks.
In July, the Group announced it is investing more than €500 million and hopes to start operations in 2022 with the aim of installing and operating at least 1,700 charging points within five years.
The speed of change is inevitably upending the business models of the traditional energy giants. What will the future hold for the old-school oil and gas companies?
Shell has set out its strategy to support the decarbonisation of road freight. A top priority is increasing the production and availability of hydrogen for heavy-duty and long-haul medium-duty trucks. The company is part of the H2Accelerate collaboration with Daimler, Iveco, OMV and Volvo that is focused on the large-scale rollout of hydrogen trucking infrastructure across Europe over the next 10 years.
The company is also expanding electric charging infrastructure and services for light-duty and short-route medium-duty freight trucks, and it is supporting low carbon fuels, for example, liquified natural gas (LNG) and biofuels as zero emission technologies are developed.
Shell has also developed gas to liquid, or GTL, fuel. This is an alternative diesel fuel derived from natural gas, which burns more cleanly than conventional crude oil-based diesel. It can cut emission of particulates by 90 per cent compared with regular mineral diesel and can greatly improve air quality but its carbon dioxide reduction is a fraction of HVO.
Mammoet, the Dutch international heavy lift and transport giant, was an early user of GTL fuel and recently completed its first specialized transport project using HVO, to power SPMT for a module move (see ICST July 2021).
Paul van Gelder, Mammoet CEO, comments, “It’s my personal belief that in our industry, there will be no silver bullet on sustainability...there are many developments, we are not betting on one horse. We are following all opportunities and are tapping into what we think are the best solutions.”
Gradual change
Ton Klijn, director at ESTA – the European Association of Abnormal Road Transport and Mobile Cranes – believes industry will adopt short-term options, while the longer term solutions and their implications are worked out.
“For mobile cranes – in the 120 to 150 tonne range – the short term option will probably be to use diesel to get the cranes to site and then battery power for the crane movements on site itself.
“Another interim solution might be to increase the use of LPG; it is not completely clean, but it is a lot cleaner than diesel and moves us in the right direction until electric battery-driven or hydrogen options are more readily available.”
He added, “Personally, I am very interested in the hydrogen combustion engine being worked on by a number of companies. I think that could well be an important part of the mix of solutions going forward.”
Finding the right technological and engineering solutions is only the first step. The next questions will be whether the products can be manufactured and distributed on a global scale, whether secure supply chains can be established and whether the necessary laws and regulations can be enacted in time.
Speaking at the end of July, John Kerry, the first United States special presidential envoy for climate, said developments are increasingly being driven by innovative private sector companies and the demands of their clients.
The question will not be whether government and international political institutions can drive change but whether can they keep up.
To facilitate change and to ensure it is rapid and takes root, industry will need forward-thinking regulation, informed government support and, where possible, common international standards.
Cadman makes HVO carbon reduction pledgeCrane rental specialist Cadman Cranes in the UK has made a major commitment to reducing its carbon footprint by using HVO fuel. It says it will immediately switch 50 per cent of its fleet over to HVO fuel and plans to have switched the other half over by the end of 2021. ![]() The company calculated that over a 12-month period it produces 645 tonnes of CO2, 519 tonnes of which is solely from the use of red diesel in the mobile crane fleet. Matt Waddingham, Cadman Cranes managing director, said, “We are a mobile crane company, and we can’t avoid taking these big vehicles on the road. But we can do it in the most responsible way possible by investing in the huge advances in green technology that exist right now. The introduction of HVO to 50 per cent of our crane fleet will mean an immediate reduction in CO2 of 230 tonnes a year and our planned move to 100 per cent HVO will see our carbon footprint drop by 72 per cent overall. This is on top of greatly improved air quality caused by a substantial reduction in nitrogen oxides and particulate matter. The benefits of a switch to HVO are undeniable and for Cadman Cranes it is a vital first step on our journey to net zero carbon.” Cadman’s fleet includes wheeled mobile telescopic cranes from up to 180 tonnes capacity, mini cranes, compact crawlers, truck mounted units from Böcker, lorry loaders and specialist lifting equipment. |
Morello uses Loop Energy fuel cellElectrification of the powertrain is the biggest disruption to transportation since the invention of the internal combustion engine, says hydrogen fuel cell specialist Loop Energy. Zero-emission hydrogen fuel cell electric vehicles are being developed for specialist construction and material handling applications. ![]() In March 2021 Loop Energy and industrial transport equipment manufacturer Morello announced a co-operation agreement. Loop is supplying its eFlow fuel cell modules to power Morello’s heavy-duty tractors designed to carry heavy loads in steel and paper mills and other industrial applications. A series of 10 tractors will be deployed over the next 18 months, Loop says. Italy-based Morello is known for its industrial vehicles with payloads up to 1,000 tonnes. It already designed and launched a battery-electric version of its heavy-duty model. Loop says Morello describes hydrogen as the final piece of the puzzle with which “to provide customers with a product that delivers superior operating duration and productivity, as well as faster refuelling times and flexibility in required space and location.” After the technology has been proved, plans include transferring the technology to other industry sectors. |
STAY CONNECTED
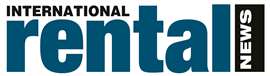


Receive the information you need when you need it through our world-leading magazines, newsletters and daily briefings.
CONNECT WITH THE TEAM
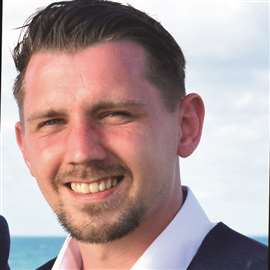

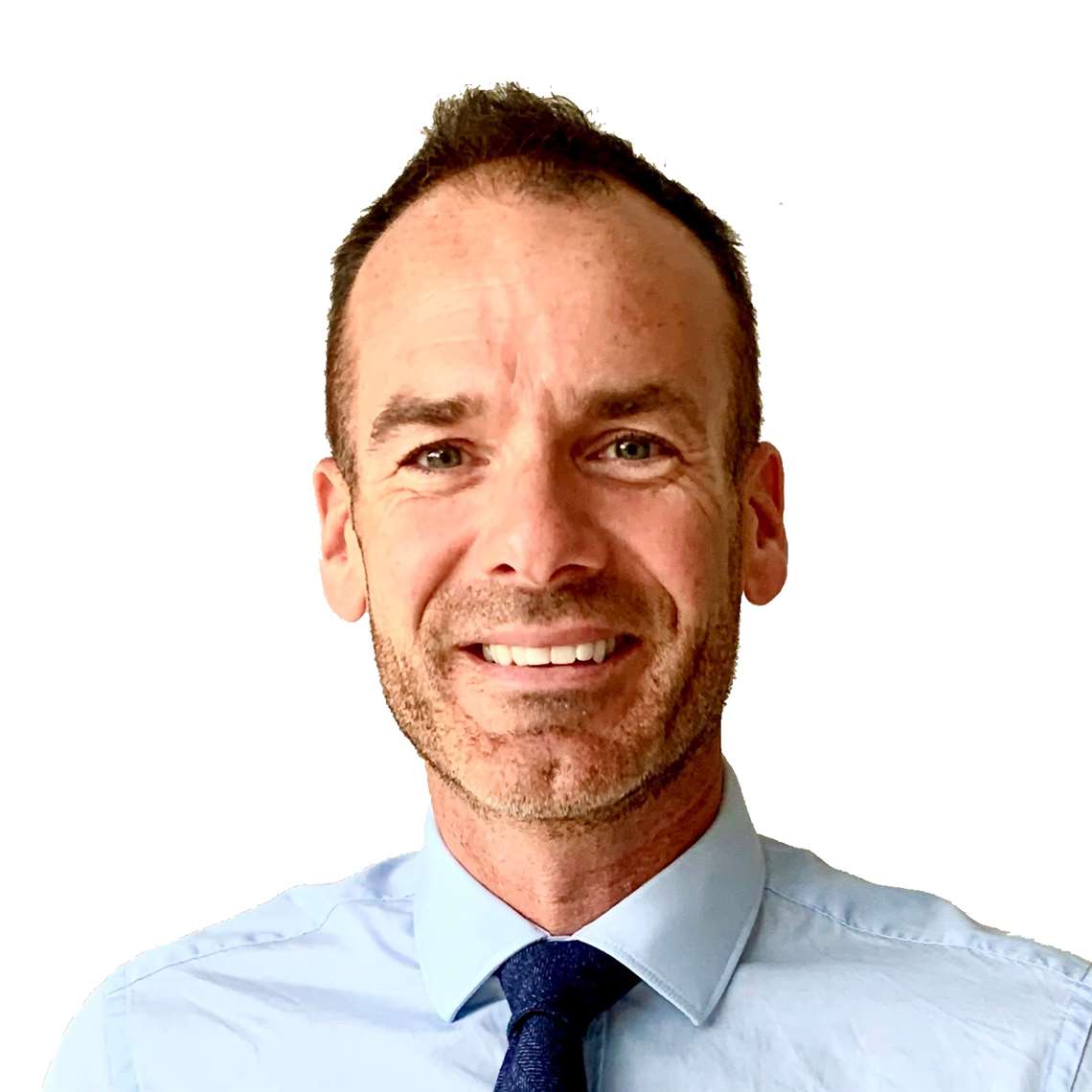