3 findings from Skanska USA’s Market Trends report
10 June 2024
Skanska – a Sweden-based global construction and development company – held its 2024 Skanska USA Building Spring Construction Market Trends webinar alongside publication of its Market Trends Report, which revealed three important topics permeating today’s industry.

In an opening letter titled “Inflation Proving Tougher to Combat”, Steve Stouthamer – Skanska’s USA’s executive VP of project planning – said, “Inflation is still top of mind for the near future,” but he noted that price escalation has stabilised.
While the industry’s bogeyman (inflation) is starting to show even the slightest signs of retreat in the US, what else are Skanska and other US builders and suppliers talking about in 2024?
Helping answer that question during Skanska’s Market Trends Spring webinar were Dean Lewis, Skanska director of mass timber and prefabrication; Rob Cantando, Skanska director of strategic supply chain; and Hardy Wentzel, CEO and founder of Think Mass Timber, among others.
All eyes on Baltimore’s Key Bridge and supply chain
Cantando opened the series by discussing the Francis Scott Key Bridge collapse in the Port of Baltimore, Maryland, US.
While initial suggestions after the tragedy were that the clean-up and rebuilding process could cause severe issues to the construction supply chain, Cantando said time and investigation has revealed that disruptions should be limited in the build sector.
“Port of Baltimore is primarily utilised for shipping and receiving passenger vehicles,” he explained. “Further research showed that very little construction material actually flows through the port.”
The Key Bridge collapsed in late March after one of its piers was struck by a powerless cargo container ship. Six construction workers were killed.
Clean-up of the channel lasted until early June, and the port remained closed until earlier this week.
Ultimately, despite the disruption to what is one of the busiest shipping ports in the US, there should be no outsized lingering issues stemming from the accident.
“We don’t anticipate any major disruptions because of what’s going on at the Port of Baltimore,” confirmed Cantando.
Construction material prices are up
While it was good news for the construction industry from Baltimore, the bad news is that materials pricing is already highly elevated and, in some cases, not showing signs of retreat.
Concrete prices rose throughout 2023 and into 2024 – about 20% – Cantando said.
“The root cause is higher cost of raw materials, labour, and diesel fuel,” he added. “These raw material and labour costs escalated so quickly that ready-mix producers were playing catch-up to recover lost margin.”
He expects concrete prices to continue rising “but at a much lower rate than what we saw in 2023.”
Metal prices continued to inflate, particularly copper, which reached an all-time high in May of this year.
“Aluminium is up 16%. Zinc is up 20%. Copper is up 34%,” said Cantando, who explained a short squeeze in the copper markets caught some traders flat-footed, which required them to purchase large amounts of copper at an elevated price to cover short positions. “The additional buying activity that happened at these higher prices just added fuel to the fire and drove pricing to the record highs.”
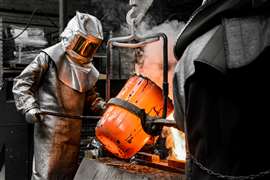
The price for copper – a metal that is vital to the electrical, computing, and data centre industries – has since returned to somewhat normal levels, “which is still elevated.”
Cantando noted the electric vehicle market, which is set to grow around 20% annually in the US, will be a continued driver in keeping the price of copper elevated.
He used the example of a non-electric Honda Accord, which “uses about 40 lbs [18kg] of copper.
“[The] EV version uses 200 lbs [91kg],” continued Cantando, illustrating via maths the potential demand squeeze coming for the mined resource. “90 million passenger vehicles are produced every year, and that equates to about seven million tons [6.4 million tonnes] of additional cooper when you talk about electrifying all the vehicles in the world.”
About 22 million tons [20 million tonnes] of copper is mined annually around the world.
Mass timber is working out efficiency kinks
While the emerging resource of mass timber has excited some and rattled others in the construction industry, Skanska’s panel offered a pragmatic view of the industry, as US states have increasingly codified the material use in recent years and record-breaking high-rises are entering city skylines.
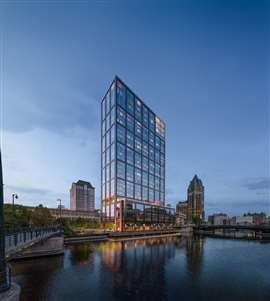
Hardy Wentzel of Think Mass Timber said the segment is moving out of the early-adopters phase and crossing into the early-majority step on the upscale lifecycle.
Dean Lewis, Skanska’s mass timber expert on the Market Trends panel, used some data to show the market growth in the decade.
“The average size of a project back in 2016 was around 35,000 sq ft (3,251m2) and that’s almost doubled in the last few years now. The average project size is now around 60,000 sq ft (5,574m2) and that’s also because of code adoption,” said Lewis.
The International Building Code (IBC), in 2021, significantly updated mass-timber structure height allowances, and already developers in the US are proposing some of the tallest mass-timber buildings in the world.
But for mass timber to become a true sustainability darling and combat the housing crisis in the way that some have advertised, significant cuts to transportation and more regionalisation will need to take place.
“To truck large distances or ship by ocean, you can see how the carbon usage really increases,” said Wentzel, showing a global map of mass timber’s production to implementation lifecycle. In some instance, the material is shipped from Nordic countries to a US distributor and then shipped again to the construction site, causing a hike in project costs and carbon footprint.
A more regionally-focused industry will be needed to realise potential sustainability goals mass timber offers, and the US forestry industry would also benefit from growth if more softwood sawmills opened and started producing the raw materials needed for mass timber.
“There’s about 72 billion board feet of sawmill capacity in North America. Our annual consumption is about 60 billion board feet,” said Wentzel. “There’s room for mass timber to have the lumber it needs [and] forests are growing every day, all the time. It probably takes North America’s forests about six minutes to regrow lumber [for a] 35,000 sq ft building.”
Lewis also added mass timber’s arrival isn’t a race to replace more conventional building materials like steel and concrete. He said both are necessities to mass-timber builds (in varying scope), and he added if construction wishes to reduce its overall carbon footprint, all build materials will need to improve their process and products.
“We need all materials to be ‘greener’ to decarbonise our overall building environment,” he said.
STAY CONNECTED
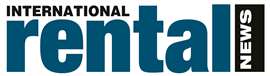


Receive the information you need when you need it through our world-leading magazines, newsletters and daily briefings.
CONNECT WITH THE TEAM
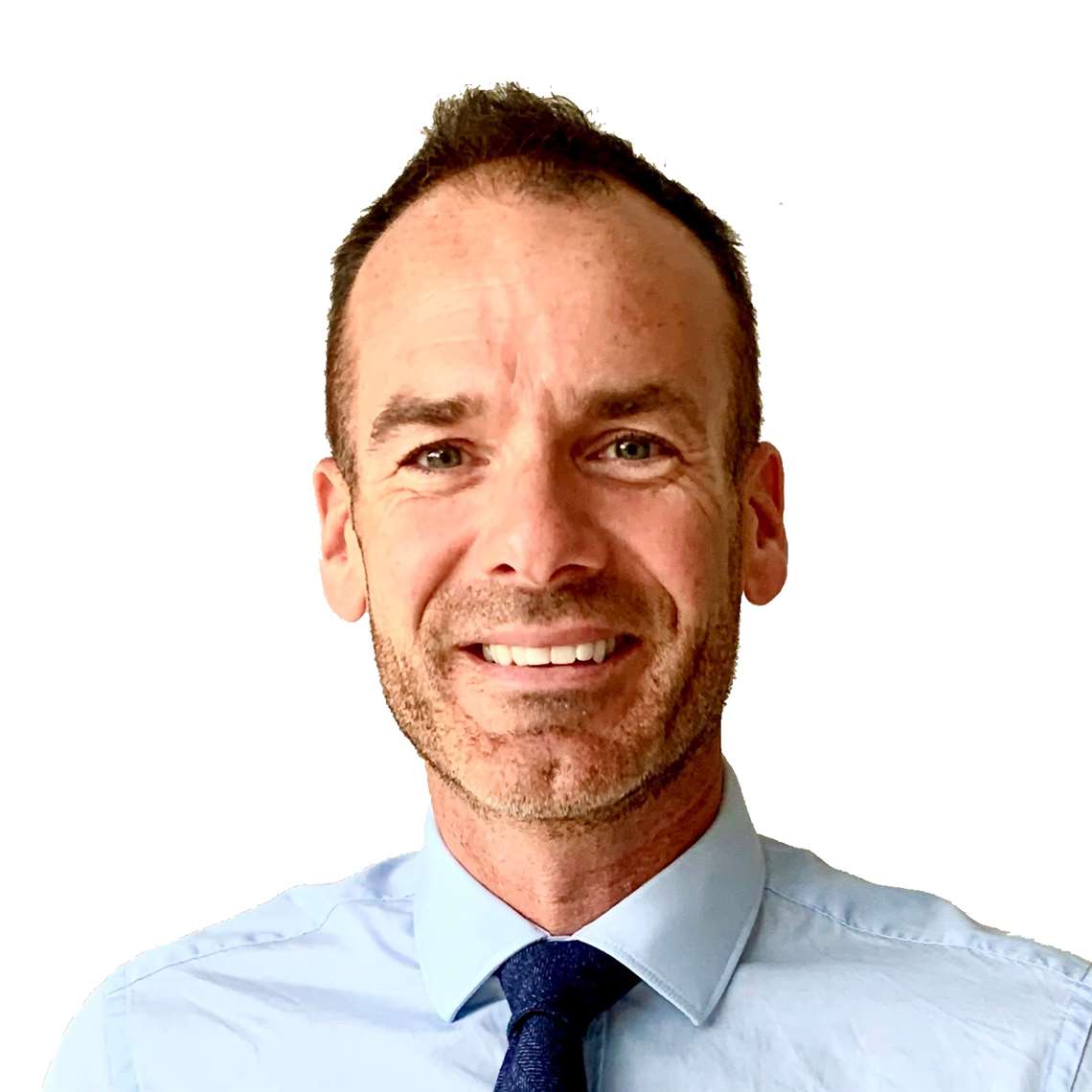
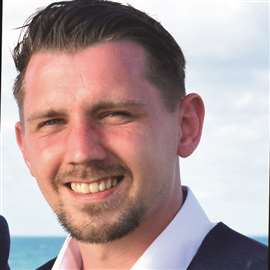