Are robots the future of tunnelling?
02 May 2022
Patrick Lane-Nott, director of engineering at HyperTunnel, tells CE how the company’s radically different approach to tunnelling - using miniature robots to dig multiple mini tunnels could one day transform the industry
HyperTunnel is a UK-based tunnelling technology company that is bringing together proven technologies from across multiple industries, with the aim of 3D-printing a tunnel inside the ground.

“Normally you dig a hole and then build the tunnel in the hole, but we’re actually building the tunnel and then we’ll dig the hole,” says Patrick Lane-Nott, Director of Engineering at HyperTunnel. The new method was created by an engineering team sourced from “innovation-rich sectors such as Formula 1, aerospace, oil and gas, and geoscience”.
They focused on a key question to guide them; what do we know from a different application that can solve this problem? This has resulted in the development of a radically different tunnelling technique.
PHASE 1 – Preparation and tunnelling
It starts with taking core samples of the ground via test bores. A proprietary 3D ground-penetrating radar (GPR) system is run through the bores and its data, along with seismic, tomographic and thermal imagery, helps create a detailed picture of the geology.
This is developed into a 3D, digital twin of the tunnel and the geology immediately surrounding it, which is supported by BIM, virtual reality (VR) and augmented reality (AR) technology. Lane-Nott says, “What we’re putting together is a flexible solution that will allow tunnellers of the future to customise their tunnel according to the geology.
“So you could have different thicknesses of tunnel lining for example, you could have different materials, all depending on what’s going on in the geology and what the use of the tunnel is.” A series of bores are drilled around the tunnel periphery and used as a skeleton or scaffold during the construction phase, into which multiple semi-autonomous robots, called hyperBots, are deployed.
PHASE 2 – Tunnel construction
The reusable hyperBots deploy an additive manufacturing process into the ground using the same principle as 3D printing, to create tunnel’s shell.
Managed by swarm technology, they operate simultaneously at different locations within the tunnel’s scaffolding to form a shell structure, according to a construction plan which provides key construction data, such as material strength, chemical volume, and location.
“Because we can work down the whole length of the tunnel, we can then just put more bots in the system to be able to do the construction,” says Lane-Nott. “It actually would take no longer to build a 1km tunnel than it would to build a 5km tunnel, because you just put more bots in and they operate in parallel.”
When the tunnel’s structural shell is complete, the untreated geology within it is disrupted to make excavation of the spoil easier.
PHASE 3 – Excavation
For excavation, HyperTunnel has taken inspiration from open-cast mining and is developing its own ‘dragline shield’ technology for large tunnels. Known as the hyperShield, the machine gets pulled through the geology and its leading edge cuts the interior shape of the tunnel, explains Lane-Nott.
“It’s remote controlled – or semi autonomous, there’s no one that needs to be onboard, and because of the disruption we’ve done already within the ground, it scoops up and pushes it [the spoil] out the back either onto conveyors or a convoy of autonomous trucks”.

Of course, the standout advantage of the method is to do with site worker safety. “The one thing we can say with absolute certainty is that safety is significantly better because we don’t have to put anyone in harm’s way until you’ve got a competent structure,” says Lane-Nott.
PHASE 4 – Tunnel lining and asset handover
The tunnel is then lined and the digital twin and all the data gathered throughout the planning and construction stages can then be used for assurance.
In addition, with the scaffolding and sensors remaining in place after construction, these can then be used for future maintenance and management of the tunnel, which effectively turns it into a ‘smart asset’.
The new tunnelling method will Initially lend itself to repairs and general inspection repairs of underground or buried structures. “We can see that happening relatively quickly, and I think that will be the first commercial work we do, in and around that, and that may even be around relatively simple structures – there’s a lot of opportunities,” says Lane-Nott.
The possibilities offered by the method have already been recognized by UK transport authority National Rail, which last year awarded the company with a research and development contract.

This will be completed within the next six weeks and while the HyperTunnel method is not due to be trialled on a larger scale for another year, its potential and current level of development has left many wondering; could this be the future of tunnelling?
STAY CONNECTED
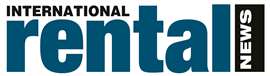


Receive the information you need when you need it through our world-leading magazines, newsletters and daily briefings.
CONNECT WITH THE TEAM
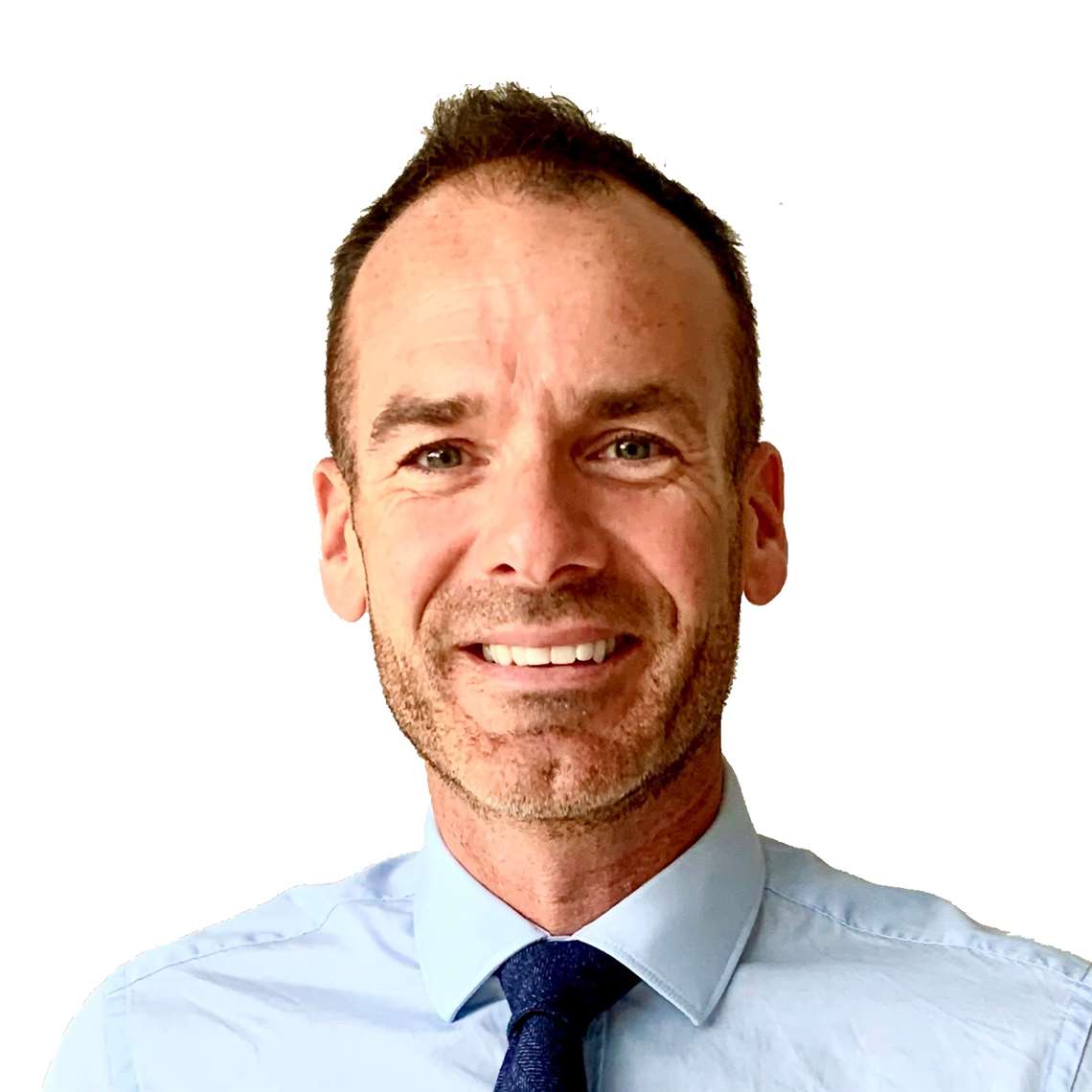
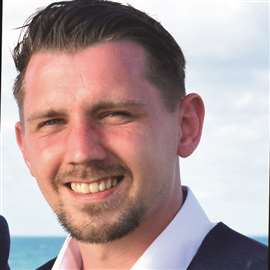