How is the aviation industry using modern access equipment
02 April 2024
Effective use is key to reducing the risks for MEWPs around aircraft reports Owen Stockden, Principal at consultants Equinox Partners.
From GPS to simulation training, the aviation industry is often at the forefront of adopting innovative new technology. It’s no wonder, then, that aerospace was one of the first sectors to embrace MEWPs in the 1970s and 1980s.
In the decades prior, accessing various parts of the airframe for maintenance, repair, and overhaul (MRO) was largely accomplished with ladders and scaffolding. When widebody jets such as the Boeing 747 – coined the first “jumbo jet” – entered service in the late ‘60s, however, they posed two challenges for these traditional access methods.

The first was their sheer size, which made it harder to surround them with full-body scaffolds. The second was that fleets were now composed of a mix of wide and narrowbody jets, meaning many different configurations of scaffolds were required. To carry out MRO operations, aerospace companies required on-demand access to any part of the aircraft, and traditional access methods could no longer keep up with their needs.
Enter the MEWP. Both boom and scissor lifts soon saw rapid adoption in civilian and military aerospace operations, owing to their efficiency and flexibility. Using MEWPs, maintenance engineers could easily carry out the hundreds of different tasks required to ensure flight safety – including inspecting and replacing parts, repairing damage, installing new components, and applying enamel and paint.
From concept to standard
Following their introduction, it didn’t take long for MEWPs to become the gold standard for access. “MEWPs are a tremendous asset to the aerospace industry,” says Terry Allen. A veteran commercial pilot, Allen is the CEO of Serious Industrial Motion Simulators (SIMS), which provides simulation-based MEWP training for aerospace and other industries. “With MEWPs, airlines have much greater flexibility in setting up their MRO operations. They can also rapidly switch configurations to service different types of aircraft.”
Today, there are hundreds of thousands of MEWPs in service across the aerospace industry worldwide. Some airline and MRO companies own their MEWPs, while others rent them on a long-term or project basis. “It all depends on how they structure and schedule their maintenance, which in turn is determined by their strategy and position in the market,” explains Allen.
As is the case with other sectors that use MEWPs, there isn’t an overarching international standard for MEWPs in aerospace settings. Instead, today’s industry operations are informed by standards such as ISO 18878, ISO 18893, BS8460:2017, and by legislation enacted by the national level. “Often, the particular standards that are followed will depend on the country where the work is taking place, especially in the case of multinationals,” says Allen. “Many companies also build their own best practices on top of these standards.”
New possibilities
While MEWPs are undeniably more cost-effective and efficient than the scaffolding they replaced, they did introduce one new challenge – the possibility of striking an aircraft. “Being self-powered, MEWPs have the ability to run into aircraft with more force than ladders and scaffolds,” says Allen. “So they cause a lot more damage.”
Though human injury is relatively rare compared to other sectors, MEWP strikes result in something all aerospace companies dread – unscheduled AOG, or “aircraft on ground.” Once damaged, an aircraft must be grounded while it’s inspected and repaired, leading to flight delays and rescheduling. Last year alone, flight delays cost the global airline industry $31 billion, with unscheduled MRO contributing to its fair share of this staggering cost.
Further adding to the risk, MRO engineers may not operate MEWPs particularly often. Though they are highly trained and skilled professionals, MEWP use is not their primary competency. “The MEWP isn’t your work – it’s your ride to work,” Allen explains. Though maintenance engineers all have a MEWP operator’s card, they may go weeks or months at a time without using one as they work on machinery at the ground level instead. Whether they’re rusty from a lack of recent experience, or whether they never had much time to practice in the first place, this is where the risk of incidents creeps in.
To make matters worse, aircraft themselves are challenging to manoeuvre around. Their parabolic shapes are unlike the flat walls, ceilings, and beams that MEWP operators might encounter in most other environments. Moving up and down along the curved fuselage means also having to move forward and backward to keep the distance consistent.
Low hanging fruit

The vast majority of MEWP aircraft strikes are caused by human error. The good news, according to Allen? “That means they’re largely preventable.”
“Any time you have a human-error factor that’s causing AOG and flight delays, and you can reduce that factor through better training, that’s low-hanging fruit for cost reduction,” Allen says. “With the right training and culture, companies can save money and improve safety for everyone involved.” He recommends assessments of new operators, regular practice, and refresher training for those who haven’t been on a MEWP in a while.
“Part of the challenge, historically, is that the only way to practice manoeuvring a MEWP near an aircraft is to manoeuvre a MEWP near an aircraft. So right away, you’re putting potentially inexperienced operators, or those whose proficiency level you’re not sure of, in a place where they can damage that aircraft.”
Aerospace companies have used a variety of methods to try and mitigate this, such as padding on the baskets of their MEWPs or proximity alarms to alert operators when they get too close. “These are good approaches, but I think we can do even better if we look at something that’s already in the industry’s DNA,” says Allen.
Simulation: not just for pilots
Allen is referring to simulation, which has been in widespread use in the aviation industry since the 1950s. First used to train pilots, it is now seeing expansion to other personnel such as flight crews. Allen believes it represents the future of training for MEWP operators as well.
One of the chief advantages of simulation is that it enables users to experience potentially risky and challenging situations without ever actually placing them or their equipment in danger. In turn, the skills they build in simulation are highly transferrable to real life. “Just as a pilot might sit in a simulator to practice a takeoff, we can have a maintenance engineer practice the MEWP manoeuvres that got the plane ready for takeoff,” Allen says.

Allen’s company, SIMS, offers a portable virtual reality (VR) MEWP simulator that is seeing increasing industry adoption. (The company recently acquired the technology after buying Canada-based Serious Labs’ virtual reality (VR) simulator division).
Current users include Singapore Airlines, Lockheed Martin, and Canada-based Cascade Aerospace, with other deployments planned in the coming months. With realistic motion and real-world MEWP controls, the simulator includes training and assessment modules customised for MRO operations.
SIMS’ studies of operator data show that the simulator can assess an operator’s real-world proficiency level with 97% accuracy. Those rated as low-proficiency operators were nearly 15 times as likely to experience an incident or a near miss as high-proficiency operators. Remarkably, however, most operators could improve to a high proficiency level in about an hour of simulator training time.
Allen says there are many ways to use the simulator, from assessing each new MEWP operator to providing regular upskilling and shaking the rust off ahead of challenging manoeuvres.
“Like many simulators, it’s a versatile tool,” he notes. “What’s most important with a product like this is to use it in a consistent, strategic way as part of a larger safety plan. That’s where we’ve got people who are seeing those incident reductions that are saving costs and delivering that all-important reduction in downtime.”
When it comes to aerospace, it’s clear that MEWPs are here to stay. Allen is confident that advances in MEWP technology, as well as training tools like the SIMS simulator, will enable companies to maximize their benefits, while reducing risks.
STAY CONNECTED
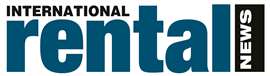


Receive the information you need when you need it through our world-leading magazines, newsletters and daily briefings.
CONNECT WITH THE TEAM
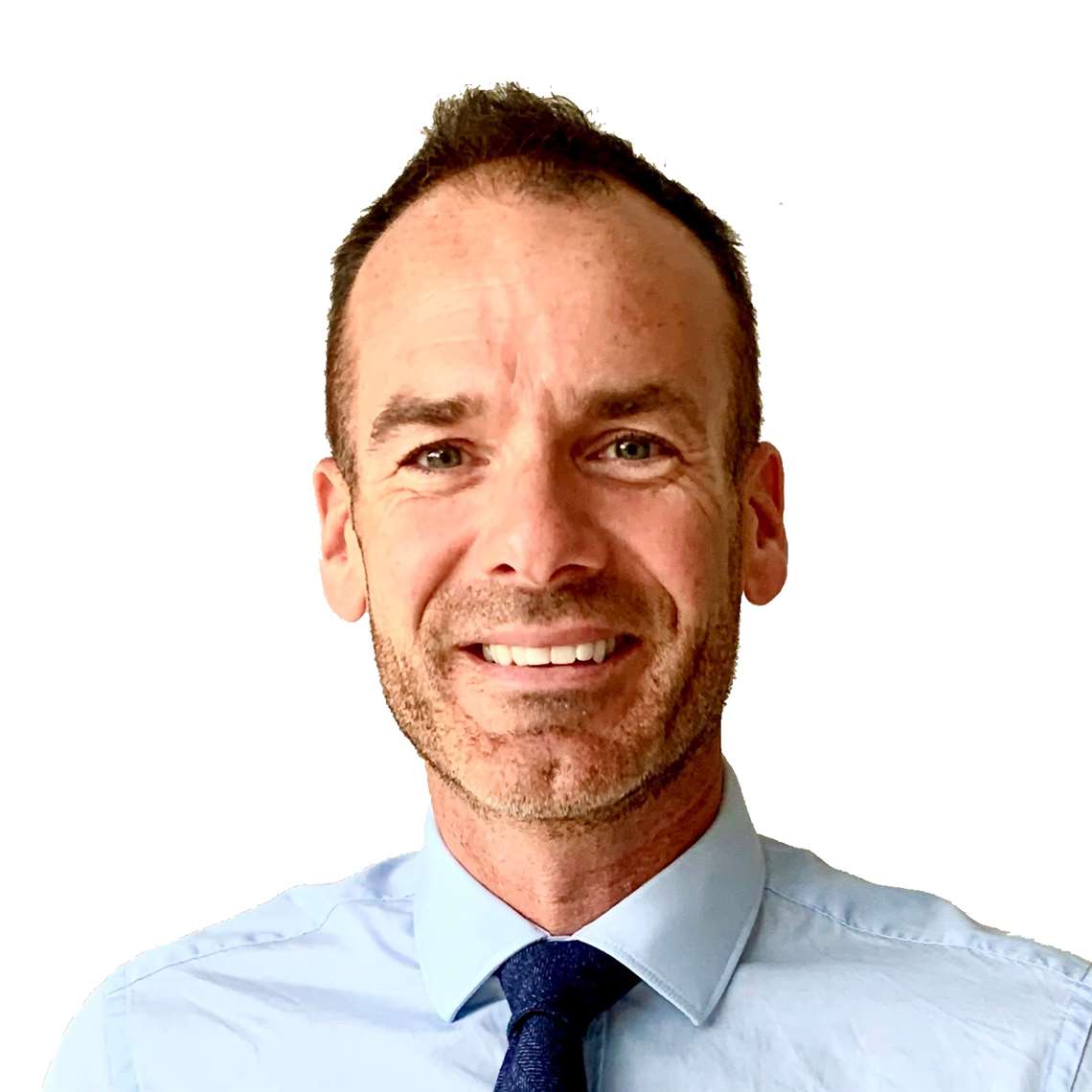
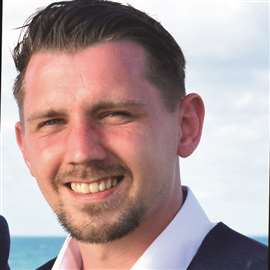