Wirtgen Group targets growth
20 October 2014
This year Wirtgen Group expects revenues to hit a record € 1.95 billion (US$ 2.45 billion), and staff numbers are also at their highest ever, at some 6,500.
One of the reasons for this growth is the Group’s acquisition of a 70% share in asphalt plant maker Benninghoven earlier this year, a company Wirtgen Group co-head Stefan Wirtgen described as a “Technology leader.” He added, “This is the perfect addition. It really complements what we have.”
Benninghoven has 600 staff and manufactures plants at two locations in Germany. Its range comprises transportable (stationary, but able to be moved from location to location), mobile and semi-mobile asphalt plants.
However, the addition of Benninghoven to the group has prompted a slight reorganisation. Wirtgen now distinguishes between its ‘Road Technology’ products – most of the Wirtgen brand range, along with Vögele pavers and Hamm compactors and ‘Mineral Technology’, comprising the Wirtgen surface miners, Kleemann crusher and screen range and the Benninghoven portfolio.
According to Stefan Wirtgen, the reason the company has made this distinction is to provide dedicated support in each of the two areas. “The idea is that we are specialised,” he said, highlighting areas such as sales, service and technical support whether the requirements are different between road building and minerals equipment.
Global Reach
And although the acquisition of Benninghoven has added to the group’s manufacturing footprint in Germany, there is also a push at Wirtgen for greater internationalisation. AS Stefan Wirtgen said, “We are now placing an emphasis on the buildings and activities of our local production. About 50% of sales are in emerging markets.” He added, “This is very challenging for European manufacturers. The world has changed and we simply have to adapt to that.”
The group has three production facilities outside Germany, a subsidiary called Ciber in Porto Alegre, Brazil, Wirtgen China, which is in Langfang, near Beijing and Wirtgen India in the manufacturing hotspot of Pune.
Both the Chinese and Indian operations are currently undergoing expansion projects. The facility in India has only been open for three years and now produces some 500 rollers per year, but it is already undergoing its first extension. This will see 8,000 m2 of covered space added at a cost of € 11 million (US$ 14 million)
Stefan Wirtgen said, “After the successful entry into the roller market in India we are starting with small pavers.”
He added that there are also plans to build Kleemann screening products in Pune, as price pressures in India mean it is difficult to be competitive without manufacturing locally.
In Langfang, China meanwhile a further 32,000 m2 of covered space is being added to the production facility at a cost of € 45 million (US$ 57 million), and Wirtgen is also opening two new sales and service offices elsewhere in China.
As well as these factories, the Wirtgen Group has some 55 sales and servicing subsidiaries around the world. The group is currently investing to expand these and build new outlets in countries as diverse as Australia, Brazil, Iran, Malaysia and South Africa, among others, and it is easy to understand why when sales through these direct subsidiaries, as opposed to the Group’s 150 independent dealers and distributors, account for about 75% of revenues.
These facilities are also used for training and servicing of equipment, and Group co-head Jürgen Wirtgen said, “We see a trend around the world where more and more contractors have closed down their workshops and rely and suppliers of machines.” He added, “We have found that the more operators we train, the fewer problems we run into.”
New technology
As part of its 2014 Road Technology Days, a customer event attended by nearly 3,500 people, Wirtgen Group took the wraps of new machines from all three of its road building brands – Hamm, Vögele and Wirtgen.
The event was held at the Hamm plant in Tirschenreuth, Germany, and the new compactors from this Wirtgen Group brand were among the most interesting new arrivals.
The H 5I and H 7i soil compactors cover the 4.5 to 8 tonne classes, and one interesting design change is that the rear wheels are now driven by wheel motors instead of an axle. Hamm said this improves climbing ability and increases the ground clearance of the machines.
The machines have been designed to be compact and easy to operate. The H 7i, for example, is 4.40 m long, which Hamm says is the smallest in this weight class. In the cab meanwhile, the control panel is based on that of the company’s HD Compact Line models, and the steering wheel is positioned to give an unobstructed view of the instruments.
Fuel economy has been improved by an automatic engine stop feature which cuts the motor if the machine has been stationary for an extended period.
The two models are due to go into full production at the end of this year, with commercial availability from January 2015.
Also new from Hamm are the DV+ 70i and DV+ 90i tandem rollers, available a double vibratory roller (VV), an oscillatory roller (VO - a vibratory and oscillatory drum) and as a combination roller (VT).
One of the most striking things about the compactors is that they look almost identical from the front and the back. Indeed, Hamm said this was part of the design philosophy, which extends to the 180° rotating seat, allowing the operator to be comfortable whatever the direction of travel.
Operators will also appreciate the large cab with plenty of glass and widened access. The controls have been designed to be ergonomic and intuitive to use, with the most important functions included on an armrest joystick.
Series production of the DV+ is scheduled to start at the beginning of 2015, with availability from the spring.
Wirtgen meanwhile used the event to unveil the W 50 Ri and W 60 Ri, compact milling machines with cutting widths of 500 mm and 600 mm respectively.
They feature Wirtgen's proprietary Level Pro Plus levelling system to make operation easier and improve milling performance. This is accessed by a new high-resolution display.
At the sharp end, as it were, the milling drum is part of a new generation designed to minimise wear and increase the drum life by up to 75%.
Also new from Wirtgen is the spreader pack (S-Pack) for its WR240, WR240i and WR250 milling machines. This option is designed to allow binders to be spread without creating clouds of dust by placing the binder straight in front of the rotor so it is immediately mixed.
New from Vögele meanwhile are the Super 1600-3i and Super 1603-3i asphalt pavers. These are compact machines for paving widths up to 7.5 m on the tracked model and 7 m on the wheeled variant.
They include many of the features from the company’s larger pavers, such as the Eco Plus fuel and emissions reduction system, comprising a splitter gearbox that disengages paving functions after a minute of idle time and a variable speed fan, among other components.
The paver also has Vögele’s Pave Dock system onboard to cushion jolts when asphalt trucks back up to it to deliver material, and there is also the Pave Dock Assistant system of lights to help communicate with the feeder vehicle.
The operator handles all machine functions through the Ergo Plus 3 operating system, and one aspect of this is the ‘Auto Set’ button, which takes care of the numerous operations to prepare the paver for either transportation or paving at the push of a single button.
Another new innovation from Vögele is to offer its Spray Jet option on the Super 1800-3i paver. As the name suggests, the Spray Jet module is for spray paving applications of thin overlays, as well as conventional binder and surface courses.
STAY CONNECTED
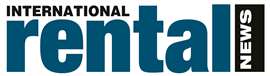


Receive the information you need when you need it through our world-leading magazines, newsletters and daily briefings.
CONNECT WITH THE TEAM
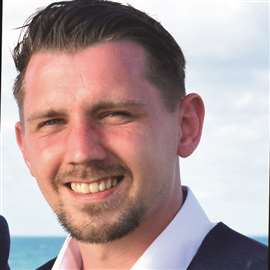

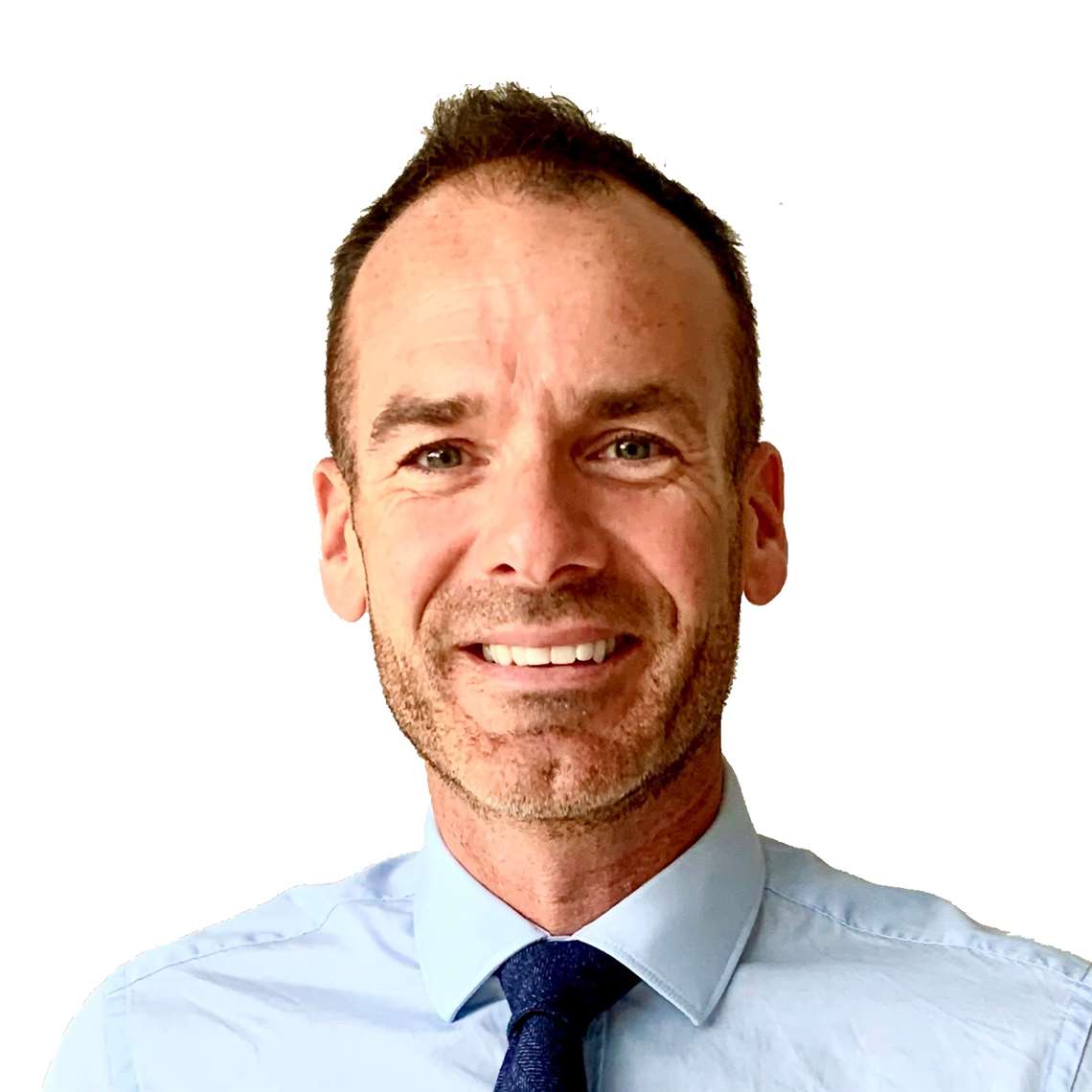