Opinion: The trouble with ditching diesel compressors
23 April 2025
In the world of mobile compressors, diesel power remains dominant. Alex Persyn, an expert in product management for portable compressors, gives his view on what the barriers are to cutting emissions.
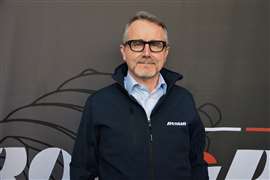
Diesel-powered mobile compressors have been offering their loyal services on construction sites across the globe for over a century.
While their role is not disputed, the use of diesel engines frequently is.
Alternative technologies already exist. For example, we see a growing interest in our VRH (hydraulic-powered) and TVR (PTO-powered) models.
However, these are carrier-mounted and therefore remain a niche solution compared to the broader construction market’s needs.
When it comes to offering a powerful, reliable and above all autonomous source of pneumatic energy, the diesel-powered mobile unit is iconic and difficult to match.
Nobody denies the need for emission reduction measures. The current generation of Stage V diesel engines is the cleanest available today. However, compared to prior engine generations these do come at a substantially higher price.
While we, as an OEM, can only bring Stage V compliant models to market in Europe, there is no European incentive to phase-out older compressor models.
The overall build quality of mobile compressors, combined with good service, means that units made 10-15 years ago often remain on active duty.
Rolling out a European initiative to replace these aging compressors with new Stage V models could effectively contribute to a substantial reduction in annual carbon emissions.
Applications for alternative power
The search for alternative power is ongoing. From the perspective of someone familiar with manufacturing diesel engine machines, I am very curious about further developments in the potential use of hydrogen combustion engines.
Meanwhile, electrification gets the most attention overall. For mobile compressors, fitting batteries is, in our appreciation, not the answer.
This is technically feasible but dramatically increases the weight, cost and mobile “range anxiety” of the unit.
Electric engines are being fitted but powering a screw type compressor is more demanding than driving a piston type, for example.
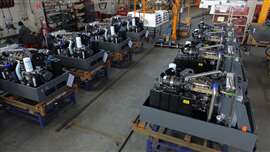
Besides the price reality, there are also some operational challenges.
Firstly, not only is the unit not autonomous anymore, but additional cables on-site are also not always practical.
Above all, 63-125A connections are not that frequently available.
32A is more common but does generally not allow you to use the full potential of current electric models.
In a construction context, the mobility and autonomy remain key. Using a diesel generator to power an electric compressor would be rather ironic.
In an industrial context, infrastructure is fundamentally different and connectivity and even mobility might be less of an issue.
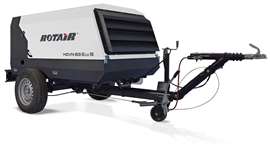
More rental companies are offering weatherproof stationary units mounted on lifting frames for such applications, a niche where we collaborate with our Elgi Europe colleagues.
Conclusion
The push from several governments or municipalities for zero-emission - or at least Stage V-driven - construction sites is growing.
This growing awareness also impacts our project development. Some electric projects are being studied, next to extending our Stage V compliant range.
The diesel-powered mobile units still play a vital role in various air-critical applications. Going forward, particular segments might further adopt alternatively powered models, an industry shift we will keep monitoring and support.
STAY CONNECTED
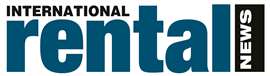


Receive the information you need when you need it through our world-leading magazines, newsletters and daily briefings.
CONNECT WITH THE TEAM
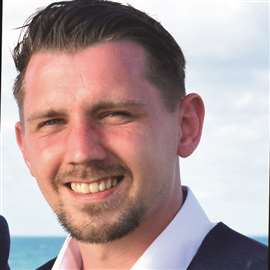

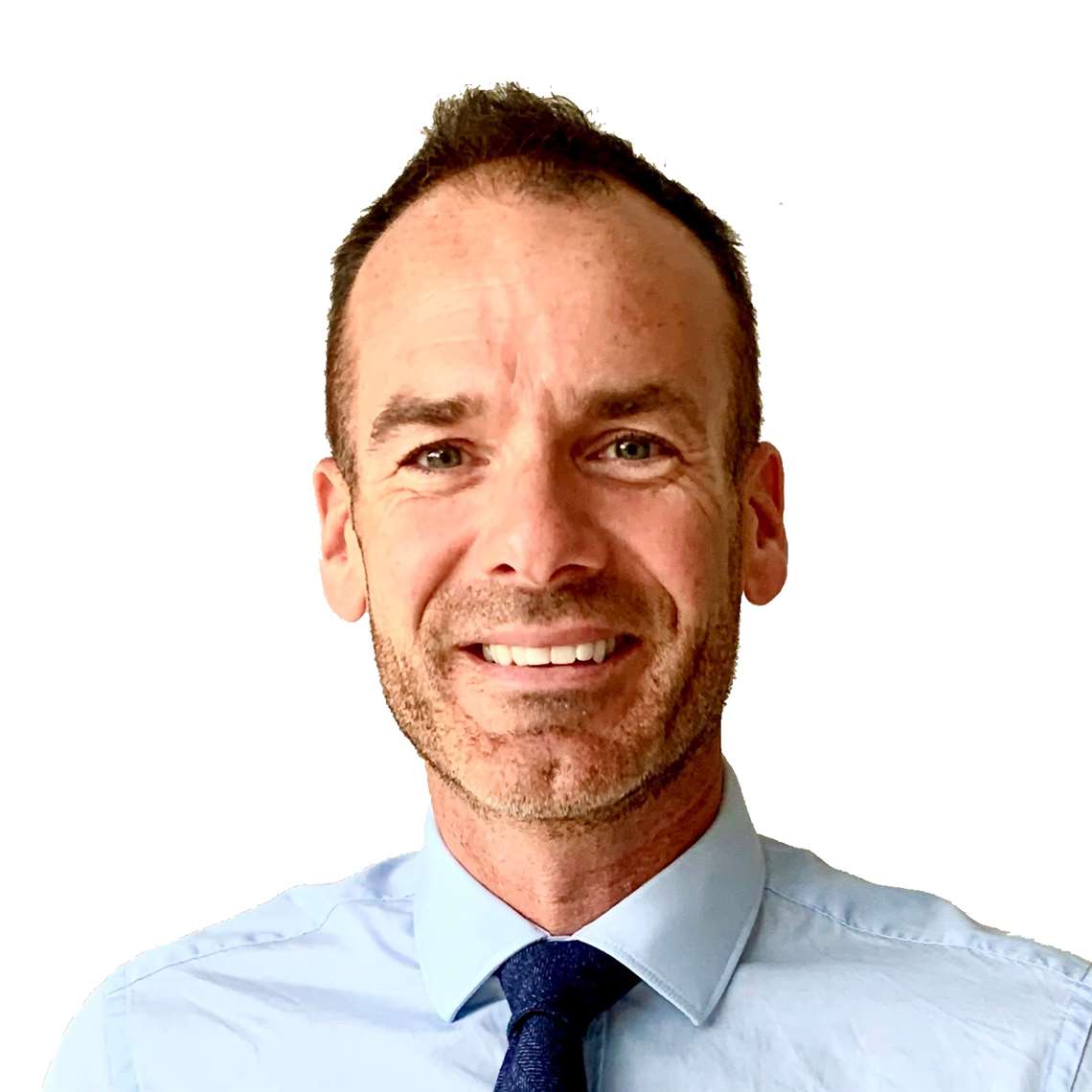