Compaction: IRN reports on new rollers, plates and rammers
14 August 2013
IRN rounds-up new compaction equipment, including rollers, plates and rammers.
Clee Hill adds MOBA control
David Hargreaves, managing director of one of the best known names in compaction equipment rental in Europe, Clee Hill Plant, says its partnership with MOBA for compaction control technology is a natural one.
“I don’t want Clee Hill to be seen as just a roller company…we have to work at developing technology”, says Mr Hargreaves, “We’re a niche company, for compaction, principally for road surfacing. So in terms of road surfacing, for pavers and rollers, MOBA did lend itself to be a good fit.”
Clee Hill has eight machines fitted with MOBA’s MCA 2000 compaction assistant, a system that helps operators manage compaction activity, recording passes accurately. For Mr Hargreaves, the benefit of the MOBA product is that it isn’t too complicated to use or expensive and can be fitted on any brand in its fleet – the company has Bomag, Hamm and Ammann units. “The key driver is getting the operator to buy into it”, he says.
Around 50% of the company’s business is in road surfacing, but it is also strong in earthworks, landfill sites and windfarms.
The compaction monitoring and recording systems also fit in with the demand from clients, who are increasingly concerned about longer term liability for road repairs and are willing to invest more up front to ensure that road materials have been laid properly and correctly compacted.
Mr Hargreaves says the technology isn’t just about proving a road has been built properly, but to prevent over-rolling, which saves fuel and labour costs and reduces machine hours.
Clee Hill is using the systems on Bomag BW 161 size machines, but as the technology becomes accepted on the market Mr Hargreaves thinks it will migrate down to smaller rollers as well.
Fundamentally, this kind of technology is about giving Clee Hill something extra in a difficult UK construction market; “All indicators are of a further decline this year”, he says, “There are still opportunities out there, but it’s tough, and margins are being impacted by the smaller workload.”
Economizer now on small rollers
Bomag is now offering its Economizer compaction monitoring system on its 1.5 t to 4.5 t light tandem rollers. The system has previously been used on larger Bomag machines and the company says it is the first manufacturer to offer such a system on smaller rollers.
Bomag says the system means that operators no longer have to rely on their instinct or ‘feeling’, with the compaction status continually displayed and soft spots identified.
Most operators, says Bomag, “stay on the safe side, preferring to carry out a few passes too many, rather than too few. The time, effort and expense that ensues can be significantly reduced by the Economizer.”
The Economizer display is situated on the machine dashboard, showing compaction progress in real time via an LED indicator. It will operate on both earthworks and diverse asphalt layers.
Bomag says the system will also detect weak spots in road sub-bases, with the operator locating these with any sudden decrease in ‘compaction’ LEDs.
The system is available on the tandem rollers in the new 5th generation BW 80 to BW 138 models.
Also new from the company is its first tandem roller with tangential oscillation. The TamGO system, being offered first on the BW 161 roller, means that one drum vibrates while the other produces horizontal oscillations, which means that the same compaction performance can be achieved with lower vibrations.
The system, which will fit between its standard vibratory rollers and the more sophisticated Asphalt Manager machines, will be particularly suited for use on bridge structures and close to buildings, where the lower vibration levels can be a significant benefit.
The TanGO exciter system is located in the rear drum of tandem rollers and can be combined with a vibrating drum at the front depending on the application. Bomag will begin offering rollers with tangential oscillation in the 10 t class with the BW 161 ADO-4, but it will be available later in other weights.
Altrad Belle’s newdrums and rammers
Altrad Belle’s new double drum walk-behind roller and five trench rammers are the results of a two year research and development programme in its compaction products.
The TDX650 roller, which uses a hydrostatic drive system, has a water tank with twice the capacity of its predecessor, which means longer usage time between refills. The canopy is now fully enclosed to reduce noise level and has a padlock location for increased site security. The electric start diesel engine has a recoil start back-up system, which prevent the loss of rental in the event of the battery going flat.
Belle says the roller is suitable for a wide range of sub-base and asphalt compaction applications, with the clear sided design allowing compaction right up to the edge on either side. The company adds that the machine’s “very low levels of hand-arm vibration” gives operators increased usage times.
The range includes machines with larger frames (RTX50, RTX66 and RTX74) as well as machines that are more compact, making them ideal for tight applications (the RTX60 and RTX68).
Crusher surprise
Hamm had a surprise in store at Bauma in the form of its new VC drum compactor, a vibrating roller than can be fitted with a range of different tools, allowing the unit to operate as a padfoot soil compactor or a concrete and stone crusher.
A total of 150 quick-change toolholders are welded to the drum, with Hamm offering a range of tools for different applications, including padfoot roller or picks for cutting or loosening rock.
The manufacturer is offering two VC compactors: the H 25i VC (pictured here) with a 160 kW Tier 4i/Stage IIIB engine and the 3625 HT VC with a Tier 3/Stage IIIA engine developing 155 kW.
Hamm says the result is a machine that can compact cohesive soils when fitted with padfoot tools, and when fitted with picks will break up rock layers consisting of basalt, granite or minerals of comparable compressive strength as well as mixed soils, while compacting the soil to a great depth.
Roadbuilding applications include homogenisation of rock or breaking up concrete as well as compaction during cold recycling.
Also at Bauma the company added four oscillatory models to its HD CompactLine, which means that it is offering oscillatory machines not only for medium and heavyweight tandem rollers and compactors.
The HD CompactLine comprises 16 models in the sub -4.5 t weight category, with the four new oscillatory models being the HD 10 VO (2.6 t), HD 12 VO (2.8 t), HD 13 VO (4.0 t), HD 14 VO (4.4 t). The ‘O’ in the name is what denotes that the rollers are oscillatory.
Hamm says it is responding to increasing demands for high-quality compaction even in extremely small areas.
Control and flexibility from Wacker Neuson
Wacker Neuson is now offering a compaction control system called Compatec with its DPU 6555 reversible vibratory plate. Compatec, which uses eight LED lights to indicate the degree of compaction, is available as an option and can also be retrofitted to DPU 6555 models made since 2011.
The German company says the system will be particularly valuable where the machine is being used by an inexperienced operator who may need guidance when assessing if a soil is well compacted.
Wacker says Compatec “works very reliably and fault-free, the unit's service life is extended and the risk of damage is minimised, which are features that rental yards and large contractors in particular value when different users work with one unit.”
Also new from the company is the RTx trench roller, which uses detachable drums sections to change the operating width from 56 to 82 cm. The system means the same roller can be used both for narrow trenches and larger applications.
The roller replaces the RT 56 in the Wacker Neuson product range, although the RT 82 with a fixed drum width of 82 cm will still be available.
Compaction overhaul
The first half of 2013 saw the largest product launch in large compaction machines ever from Ammann as it introduced European Stage 3b (Tier 4i) models, including single drum rollers from 3 to 25 t, pneumatic tyred rollers and articulated and pivot-steering tandem rollers from 1.2 to 14 t.
These include its first ever 9 t articulated roller, the ARX 90, a 9100 kg operating weight model with a working width of 1680 mm and static line load of 27.2 kg/cm. The unit is powered by a Deutz 74 kW engine.
At the smaller end of the scale is the new Rammax 1575 CI, an articulated counterpart to the skid-steered Rammax 1515 trench roller. Ammann says the new unit “underscores Ammann's position as a specialist for trench rollers and rounds off the world's most comprehensive programme offering both steering concepts available on the market.”
The 1575 is equipped with a water cooled Yanmar 3-cylinder engine and Ammann says it has the lowest centre of gravity available on the market, giving it good tilt stability of difficult terrain.
OTHER COMPACTION NEWS
JCB has introduced the first two models in a range of “new and improved” soil compactors. The VM117D (pictured) and VM137D are 11 t and 12.2 t operating weight models powered by Stage IIIB/Tier 4i JCB Ecomax 93 kW engines. Both rollers come equipped as standard with a smooth drum and JCB says “significant enhancements have been made to the compaction criteria, including amplitude, frequency, centrifugal force, static linear load and weight distribution, resulting in fewer passes being required to meet the material density requirements.” The VM117 and VM137 are global machines and will be manufactured in Germany, India and Brazil, available with Tier 2, BS3 and Tier 4i/Stage 3b engines.
Groundcare equipment specialist Toro is now offering rental professionals a range of compaction equipment following its acquisition last year of the products from Stone Construction Equipment. The range includes plate compactors, rammers and a trench roller. Pictured is the TR-34 Trench Roller, which provides 7070 kg (15709 lb) of centrifugal force. The plate compactor range comprises both forward and reversible plate compactors as well as three rammer models.
Weber MT’s new CR 9 plate compactor offers a centrifugal force of 100 kN and weighs 730 kg. New features include an infinitely variable, electro-hydraulic tip control that allows for precise and convenient shifting between forward and reverse travel, and guide bars that can be adjusted to the height of the operator's body. Powered by a Hatz Diesel 1D 90 engine, the CR 9 also offers low maintenance requirements because of a centrifugal clutch with automatic tensioning feature and throttle cables installed inside the guide bar.
STAY CONNECTED
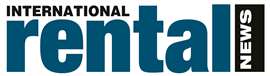


Receive the information you need when you need it through our world-leading magazines, newsletters and daily briefings.
CONNECT WITH THE TEAM
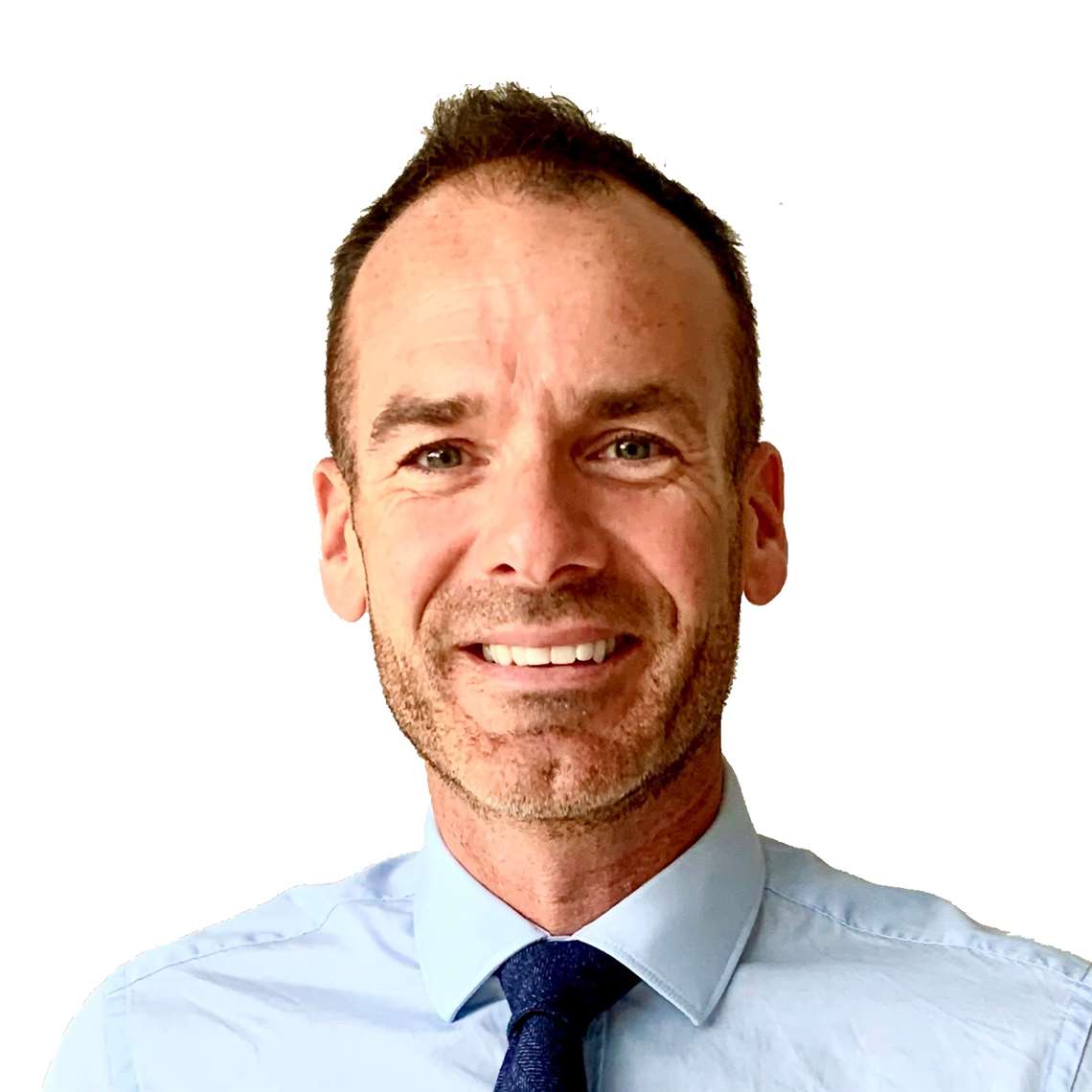
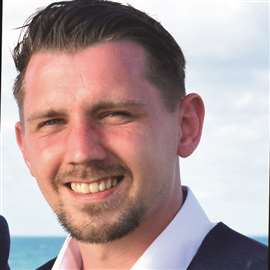