ECO mode: new rental-friendly compaction equipment
23 April 2014
Among the many new compaction launches of recent months there are plenty offering ‘Eco’ operation, with lower fuel use. IRN reports.
Altrad Belle, the UK manufacturer of small compaction, concreting and cutting equipment, continues to expand its compaction range, with the first few months of 2014 seeing a new, lightweight version of its twin-drum roller, its first electric powered plate compactor, and a diesel powered rammer.
The walk-behind TDX 650A roller is an alternative to the company’s previous TDX 650, launched at the end of 2012. The key difference is an operating weight of 650 kg, which is 125 kg lighter than the original machine.
“A lot of the 650s were being sold in France”, says Ray Neilson, managing director of Altrad Belle, “but some customers were saying that they were being used for small layers of hot asphalt, where you don’t need the same weight. So we have created this second machine.” The original 650 – popular in markets like South Africa, the Middle East, South America and parts of Africa – will still be produced.
Using a 7.5 hp Yanmar diesel engine – and now with an electrical start and manual start as back-up – the 650A has a drum width of 650 mm and a centrifugal force of 16 kN. It has the same 65 litre water capacity as the standard 650.
“Two of the top five rental companies in France have pre-ordered the new 650A”, says Mr Neilson. Production started in March with availability building up in April, May and June.
Altrad Belle, which is part of the French concrete mixer and scaffolding business Altrad, also has a new diesel rammer, the RTX 80D, using a 3.5 kW diesel Yanmar engine.
This unit, weighing 86 kg and offering 20.5 kN impact force and 450-600 blows per minute, draws on the design work done for the new range of RTX 66 and 74 rammers launched last year. It will be available with three foot sizes – 6, 9 and 12 in pads.
Target markets include emerging markets and in particular the oil and gas sector. Anthony Gibbs, Altrad Belle’s export sales manager, says; “In the oil and gas applications you can’t use petrol rammers because of the sparks – it has to be diesel.”
Finally, the Buxton, Derbyshire-based company has added its first ever electric powered plate compactor to its range of plates. The PCEL 400E is designed for use outside on applications like patios, or inside buildings during refurbishment work or during construction.
Priced the same as the petrol equivalent, but a lot cheaper to operate, the 50 kg compactor uses a fixed-speed motor designed specifically for this unit to belle’s specification.
“This means that if you give it to a home user, it won’t trip out the consumer electric board”, says Ray Neilson. In addition, it will accommodate wide variations in electric cable length, which creates variations in electric power supply.
Available in both 110 V and 230 V versions for the UK and mainland Europe, the 400E has a plate width of 380 mm and centrifugal force is 11 kN. Mr Neilson says it was an enquiry from a major European rental company that led Belle to develop the product.
The new products reflect continued investment in the business since its acquisition by Altrad in 2008. The company has doubled production staff at the factory to around 110 over the past year, and is increasing in-house content of its products, including the new twin-drum roller.
Mr Neilson says this reflects both an upturn in market demand – including from the UK, which still represents half of all sales – but also improvements in its product range; “Our range of rammers is now in a different league – we’ve got a better, more reliable product. In the past they were nice machines, but didn’t have enough power. The rammer redevelopment has been huge for us.”
The business grew its sales by around 10% last year, to around £30 million, and Mr Neilson says this year could see similar growth, although it could be more. Belle’s parent, Altrad, has been growing even faster, from revenues of around €300 million five years ago to more than €700 million last year.
Also investing in its compaction products is Atlas Copco Road Construction Equipment, which is now making machines in five countries worldwide: Germany (pavers), Sweden (rollers), Brazil (rollers), China (rollers, pavers) and India (rollers), each with its own engineering design team.
The company has set itself some ambitious targets for the 2014-16 period, with the aim, it says, of retaining a “lead” position globally on rollers, staying at number two in pavers, and working to reclaim a leading place in the planer market as well.
At a recent product launch in Sweden, the company said new machines were being designed with three main criteria in mind – they have to be better than before, conform to the ideals of sustainable productivity, and be safe.
“We have to make sure the new product is doing better than before, with enhanced productivity, but needing less energy and producing less emissions”, says Herman Mattyssen, vice president marketing.
Environmental issues are important, he says. “We always have to be one step ahead, and so we are already working with Tier 4 Final engines. Also noise is very important.” This is for operator comfort and to be able to work in cities.
With ergonomic changes to the cabins, operators can stay fit all day, he said, adding that this was important in places like Scandinavia when there are extended shifts in the lighter summer months as a result of the shorter roadbuilding and repair season.
New is the Dynapac CG2300, adding to its articulated CC machines. The CG2300 is 3.99 m long – important for manoeuvrability - and 2.99 m high. Instead of central articulation, machines in the Dynapac CG roller range traditionally have steering on the drums.
The cab on the Dynapac CG2300 has been designed with the operator in mind, and drum edge visibility is described as excellent thanks to an extended sideways sliding seat and steering assembly.
A standard ECO reduced fuel consumption by more than 15%. The company says the ECO mode was the result of closely monitoring the fuel consumption of the new Dynapac CA2500 – 6500 soil compactor range and its large CC asphalt rollers, as well as the new CG2300. It claims all the rollers consume 15 to 20% less diesel than the previous range without ECO Mode.
The engine is Stage IV/Tier 4 Final ready and claims low emissions. Advanced options that are available, include an edge presser/cutter (left and right), and a chip spreader.
Caterpillar is also promising lower fuel use with its latest compaction products, with the new B-Series utility compactors in the 1.8-5 t classes comprising eight models: the CB22B, CB24B, CB24B XT, CB32B, CB34B, CB34B XW (extra width), CC24B and CC34B.
These machines, which will typically be used for smaller applications such as streets, bike paths, courtyards, patchwork, parking lots, driveways and town centre work, have several improvements over previous models.
Designed for rental, they have an ECO mode that makes a “significant” difference to fuel use, the seating areas has more legroom, and the new dashboard design includes “intuitive controls and easy viewing LCD display for day and night operation”.
Other improvements include and more robust, reliable water spraying system with a larger capacity tank allowing up to 10 hours operation. The 3X models have 300 litre tanks and the 2X have 235 litre tanks. The rollers can also be fitted with up to 400 kg of additional ballast to increase linear loads, making the rollers more versatile. Drum diameter increases from 700 to 720 mm, which reduces the rolling resistance. The 3X models have two vibration frequencies, while the 2X units have three.
Meanwhile, JCB, in addition adding several new compactors to its range, has also announced some changes to its manufacturing strategy. It is to close its factory in Gatersleben, Germany, which it has operated since the 2005 acquisition of Vibromax.
Production of its compaction range will shift to JCB factories in the UK and India, reflecting increased demand from emerging countries. Ninety jobs will be created in the UK and India, although 145 will be lost in Germany.
JCB CEO Graeme Macdonald said, “The decision to relocate production of compaction equipment to factories in the UK and India is right for our business. The decision wasn’t taken lightly and the impact on our employees in Germany is regrettable. This will improve competitiveness of JCB in the compaction sector. It will also create a far more sustainable position on which we can build as we grow business in the future.”
Walk-behind compactors and the two smallest tandem rollers in the range will be built at the JCB Attachments factory in Uttoxeter, UK, while production of all soil compactors and two larger models of tandem roller will be moved to Pune, India.
In that soil compactor range, JCB has launched the first two of what it says will be a new and improved range. The VM117D and VM137D are powered by Stage IIIB/Tier 4 Interim JCB Ecomax engines delivering 93 kW (125hp).
The VM117 and VM137 machines will be offered for sale globally and will be manufactured in India and Brazil, available with Tier 2, BS3 and Tier 4i/Stage 3B engines.
The VM117D has an operating weight of 11 t, while the VM137D weighs in at 12.2 t. Both come with a smooth drum as standard with a smooth drum, although for cohesive soils both compactors are available with pad foot drums as an option.
JCB says that “significant enhancements” have been made to the compaction criteria, including amplitude, frequency, centrifugal force, static linear load and weight distribution, resulting in fewer passes being required to meet the material density requirements.
JCB’s Automatic Vibration Control (AVC) automatic compaction control system, which avoids over-compaction at the end of each pass, is a standard feature of both the VM117D and the VM137D.
Like many other suppliers, an ECO Mode is available, an option that JCB says will reduce fuel consumption by 16% fuel. With the Tier 2 engine, an optional variable fan kit provides up to 5% fuel savings.
Volvo CE’’s latest soil compactors are the SD75, SD115 and SD135, all offering more power, greater efficiency and up to a 30% reduction in fuel consumption over previous models.
The three new models are Stage IIIB emission compliant and are fitted with the new turbocharged 4-cylinder Volvo D4 diesel engine producing between 75 and 110 kW.
Volvo CE Road Machinery product manager for sales region EMEA (Europe, Middle East and Africa), Paul Johnson, says the new SD soil compactors “put performance and operator comfort at the heart of the process with shock absorbing cab mounts and highly effective sound-insulation throughout the Volvo cab ensuring new levels of well-being. Vibration is essential for efficient material compaction so distancing and protecting the operator from this represents a significant step.”
He says all three SD compactors have high and low amplitude and frequency as standard, while a five-frequency selector is available as an option for even greater optimisation when matching drum frequency to material type.
Volvo Smart Power mode is available as an option on both the SD115 and SD135, which helps reduce fuel consumption without having any adverse effect of compaction performance. A further benefit of the new SD compactors is the ease with which the smooth drum can be converted to a padfoot. “We have designed in the Volvo clamp-on kit which means users require minimal tools to convert the drum,” said Mr Johnson. “This further extends the flexibility of these compactors.”
From Wacker Neuson in Germany comes the new version of its asphalt roller RD27, with additional features such as a detailed control panel giving a quick overview of all functions as well as a multi-function lever for controlling the vibration options and the water supply with one hand.
With a compact design - only 2.5 m long and 1.0 m wide - the roller can be switched between low and high compaction force. The low centrifugal force is best for asphalt compaction while the high level is ideal for the compaction of granular materials.
All-round visibility has been improved, with a modified shape of the hood and a high seating location providing for more safety on the job site. A new vibration damped driver's cabin and a new seat provide greater comfort and fatigue-free working.
The RD27 is available in two versions: a base variant has the forward and backward folding roll-over protective structure and the ergonomic driver's seat.The second version additionally offers a central lifting point for easy transport, a left-sided armrest, drum-edge lighting, and a fold-down scraper bar, as well as an optional automatic vibration connection and water cut-off.
Making improvements to its range of tampers and rammers is Weber MT, with the new SRV 590 and the SRV 600i. The SRV 590 is a lightweight unit, weighing just 62 kg, with the low weight put down to the redesign of 20 components.
The SRV 600i is designed for the international market, a basic model stripped of some additional features, and weighing 63 kg. Weber MT says; “These reductions, however, do not impair the model's suitability for professional applications in any way…Despite its light weight of 63 kg, this tamper will satisfy the highest standards in terms of performance, reliability and quality even under the harshest conditions.”
North America is getting additional compaction machines from companies including Chicago Pneumatic Construction Equipment and Allen Engineering.
Chicago Pneumatic is offering a range of compact tandem asphalt rollers and soil compactors, including articulated tandem asphalt rollers in gasoline and diesel models, and small vibratory rollers for soil compaction. The new models now available in North America include the gasoline asphalt AR90G, the diesel articulated tandem asphalt roller AR100, the AR120, and the following soil rollers: SR130D and SR130PD.
These ride-on models complement Chicago Pneumatic light compaction equipment.
Allen Engineering, meanwhile, has moved into the rammer and plate compactor model to widen its product range beyond its core concrete products, such as power trowels.
The new products, assembled by Allen in North America, include the ATC130H and ATC170H, both using Honda petrol engines that are built specifically for rammer use.
The new reversible and single direction plate compactors, three models in each line. The reversible plates use Honda gasoline and Hatz diesel engines and have working widths of between 0.5 m and 0.63 m and there are three different models to choose from.
The three single direction plates are the APC140H, APC160H and APC210H, which use Honda GX120 and GX160 gasoline engines.
STAY CONNECTED
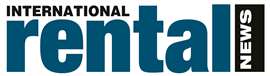


Receive the information you need when you need it through our world-leading magazines, newsletters and daily briefings.
CONNECT WITH THE TEAM
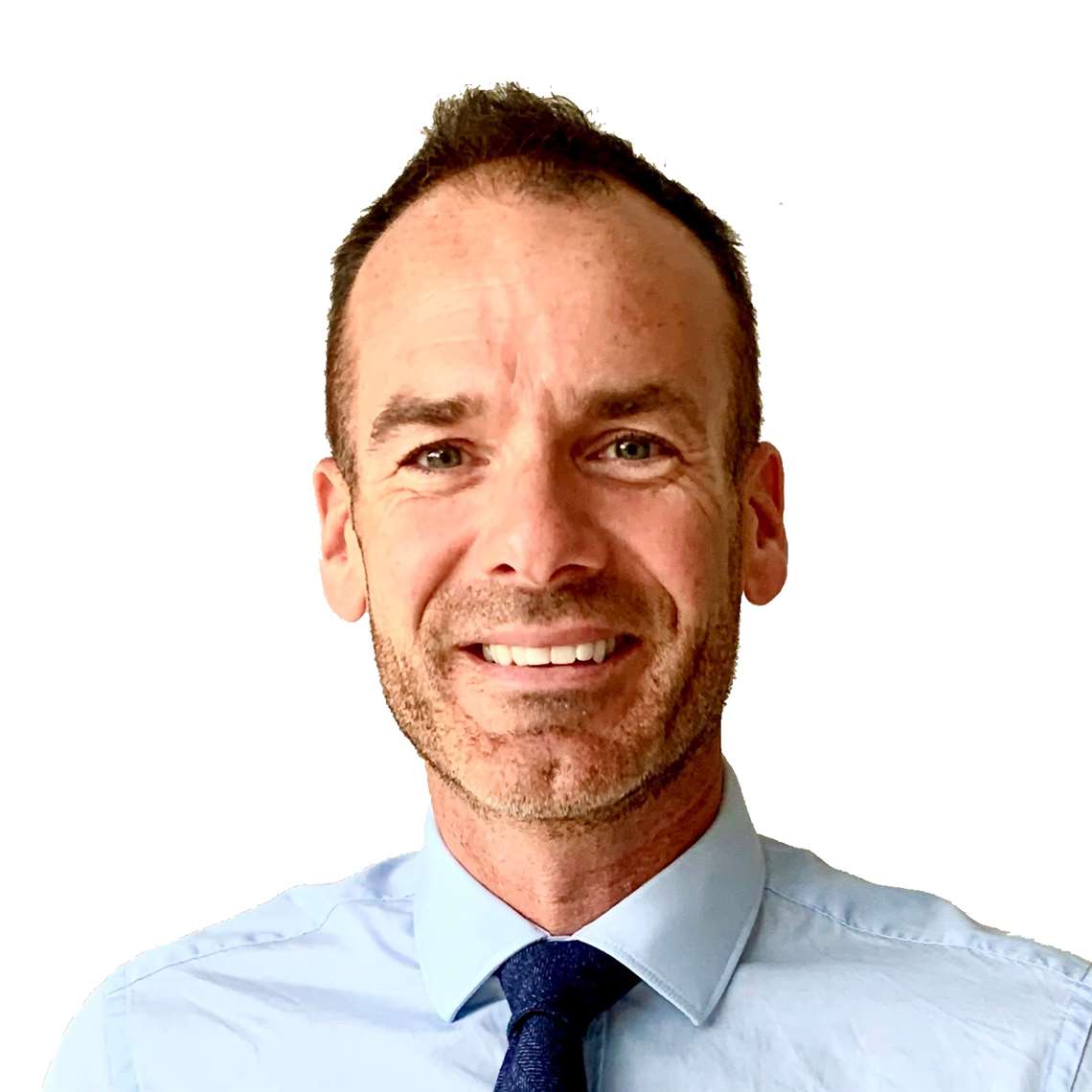
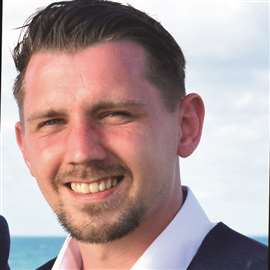