The AI systems used to fight energy waste on construction sites
22 May 2024
Construction contractors are wasting thousands of dollars a year on unused electrical devices plugged into site cabins. Lucy Barnard finds out how AI-empowered energy management systems can change that.
As consumers, we are frequently reminded to switch off lights when we leave a room, turn off heaters when not in use, and avoid leaving so-called ‘vampire devices’ on standby to avoid them sucking away the small amounts of electricity which eventually can add up to big cash and carbon savings.
But when it comes to work premises – especially construction sites – although the advice may be the same, in practice, power experts say, little is done to prevent construction crews wasting thousands of dollars and tons of CO2 on electrical devices they aren’t even using.

Adam Wright, commercial director at UK-based tech startup Measurable Energy, which specialises in helping contractors and others reduce their site cabin power usage says that construction sites are some of the worst culprits for wasting small amounts of electricity by not switching things off – something he calls ‘small power.’
“Small power is a problem on construction sites because people come in to do their shift, they do what they’ve got to do and then they leave,” he says. “There is very little ownership. They get what they need on that shift and then they’re on to the next thing. That’s how sites work. Everyone’s focused on doing what they need to do and then moving on. But what that means is that someone may have turned on the heaters because it’s a bit chilly and overridden any controls that are in place to turn those heaters on and off and then left. Those heaters then stay on overnight and over the weekends and in the end we get scenarios where it’s the middle of summer and we’ve got cabins being heated and all the windows are open because it’s too hot.”
Moreover, Wright points out that, unlike in permanent buildings, which are nearly always connected to the cheaper and greener national grid, temporary construction site offices often need to generate their energy via expensive and carbon-hungry diesel gensets.
Why do contractors waste so much electricity on site?
“For a tier one contractor, they’ll have hundreds and hundreds of sites at any one time with between four and fifty of these cabins on each site,” Wright says. “A lot of construction companies really struggle to get these cabins connected to the grid. They will book in a grid connection to try and get the electricity supplied by the grid but the project may be finished by the time the grid can connect to them so they’re often using a diesel generator which means that rather than talking about pennies here for leaving stuff on, we’re talking about thousands of pounds worth of fuel bills every month so across all those sites that can add up hundreds of thousands of pounds worth of diesel fuel that’s being wasted. And then the magnitudes get even higher when you look at the carbon emissions from that.”
To combat this, Wright says, Measurable Energy, is one of a number of green tech startups producing AI-empowered energy management systems to monitor the energy used inside site cabins and help make them more efficient.
In the case of Measurable Energy, the company installs ‘smart’ sockets into the electric plug sockets in site cabins. Each of these is connected to a cloud-based system which uses an AI algorithm to analyse which plug sockets are in use and which are still turned on but not being used. The system then uses this intelligence to switch off the power to the latter.
In 2021, the company agreed a deal with Kier to fit the new sockets on two trial construction sites. Measurable Energy fitted 37 of its sockets into cabins provided by portable accommodation business Wernick Group for use as kitchens, toilets, showers and communal areas. The company also set the cabin’s drying room dehumidifiers to only switch on when the weather was rainy.

Wright says that by using AI to identify devices which were switched on but not being used and automatically turn them off, Kier was able to eliminate 4,566 kWh of waste electricity equating to 3.9 tonnes of CO2 emissions and saving the company £3,031 in its annual electricity bill. And, by monitoring the spikes in energy use the tech was also able to identify a faulty heater which was then removed before it became a fire risk.
A similar 2022 trial with contractor Morgan Sindall at a school it was building in the UK was even more dramatic. The contractor went from paying £10,000 a month in diesel fuel to just £5,000, saving 5.5 tons of CO2.
According to Wright, the biggest waste of energy comes from site cabin drying rooms – essentially rooms full of up to ten 2kW heaters used to dry of wet clothing and equipment, preventing mold and mildew.
“The idea is that it’s been a wet day working for the guys coming off the site so they hang their clothes up in the drying room and the heaters just blast to get them dry before they come back the next day,” says Wright. “But what ends up happening is that no one wants to come back to wet clothes, so these heaters just get left on 24/7 regardless of whether it’s wet or not.”
Instead, Wright says, Measurable Energy has created a system where drying room electrical circuits on some of the sites it covers are connected to data from a local weather station. The heaters are therefore programmed to only come on when it rains and are scheduled to switch off again after a set number of hours.
How can AI reduce on-site power waste?
“Although on paper a diesel generator should be running at 60-70p per kWh, with inefficiencies in how it works, we regularly see that this can rise to as much as £5 per kWh. So if you’ve got something that’s wasting 20kWh every hour, through the night and it’s costing up to £5 per kWh of diesel fuel, you can see how quickly that adds up over a week, a month, a year.”
Wright says that since the company launched in 2022, it has installed around 10,000 smart sockets on site cabins and at construction company offices around the UK saving a total in the region of 444 tons of carbon emissions each year.
Sockets cost between £25 and £45 each on top of a monthly subscription of £1.68 per socket per month, although for contractors, this cost can be included in the overall rental cost from the cabin provider.
Contractor clients including Kier, Morgan Sindall, Balfour Beatty, Galliford Try and Balfour Beatty Vinci. The company also works with site accommodation specialists Algeco (part of Modulaire), Wernick Group and Sunbelt Rentals to install smart sockets in site cabins before they are delivered to site. Measurable Energy is also currently developing a European socket compatible with EU sockets and is looking at producing a US version too.
And Measurable Energy is just one of a number of green tech start ups designing energy management systems designed specifically for construction sites.
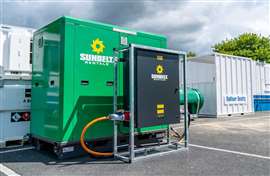
Balfour Beatty, in collaboration with Sunbelt Rentals and internet of things (IOT) specialist Invisible Systems has been rolling out its Eco Lync energy management system across its construction sites since 2020.
Rather than being connected to smart sockets, Invisible System’s Eco Lync (also sometimes known as EcoNet) runs through a consumer unit cabinet on the outside of the cabin, enabling the system to monitor not just the energy consumption of devices inside the site cabin but also electric devices used on the broader site.
Although this means that the system finds it harder to switch off individual unused heaters or monitors at a granular level, it means that the AI is capable of prioritizing the power needs of all of the electrical devices working on the site and managing demand on a power constrained site. This means that it would be able to reduce power to perhaps a drying room or staff canteen in the short time that a hydraulic lift or tower crane is operating, allowing a site to operate entirely on cheaper grid electricity or on a smaller number of diesel generators, reducing overall fuel consumption and carbon emissions. When multiple supplies are available, the technology is able to select the most efficient.
AI systems optimising construction site power
Balfour Beatty started trialing the system at site cabins on its East Leeds Orbital Route project and, within six months reported an 83% reduction in carbon emissions across the site due to the fact that it was able to switch to running on grid supply, actively manage electric vehicle charging and optimizing the heating, hot water and external lighting running schedules. The company is rolling the system out on any of its sites with more than six cabins.
“The outcomes achieved from our mutual collaboration with Sunbelt and Balfour Beatty will serve as a benchmark throughout the construction sector,” says Pete Thompson, Invisible Systems CEO. “Our solution enables the construction industry to work towards carbon-neutrality by leveraging the Internet Of Things.”
Meanwhile Bouygues says it has been installing sensor-based energy management automation system AutoMate, created by tech company Gaia Group on a number of its site offices.
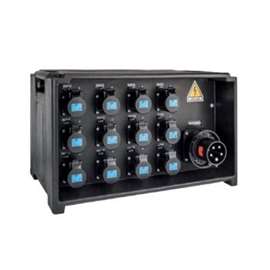
Like Eco Lync, the AutoMate system uses AI to divert power away from non-essential usage and supplies additional power where and when it is needed. To do this, it employs a range of hi-tech sensors and gadgets including geofencing technology to switch off lights and heating when staff leave the facility and to turn them back on again when it detects staff returning to the site. Sensors detect rain and automatically turn on drying facilities.
Back at Measurable Energy, Wright says that more and more contractors are starting to use energy management systems on site, often combining the offerings of more than one provider to gain maximum savings.
“I think the biggest barrier we’ve faced so far is that we’re telling people about a problem that they weren’t really thinking was a problem – or at best may have been slightly aware of – so it takes time to get that buy in.”
|
STAY CONNECTED
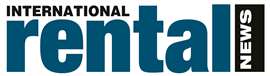


Receive the information you need when you need it through our world-leading magazines, newsletters and daily briefings.
CONNECT WITH THE TEAM
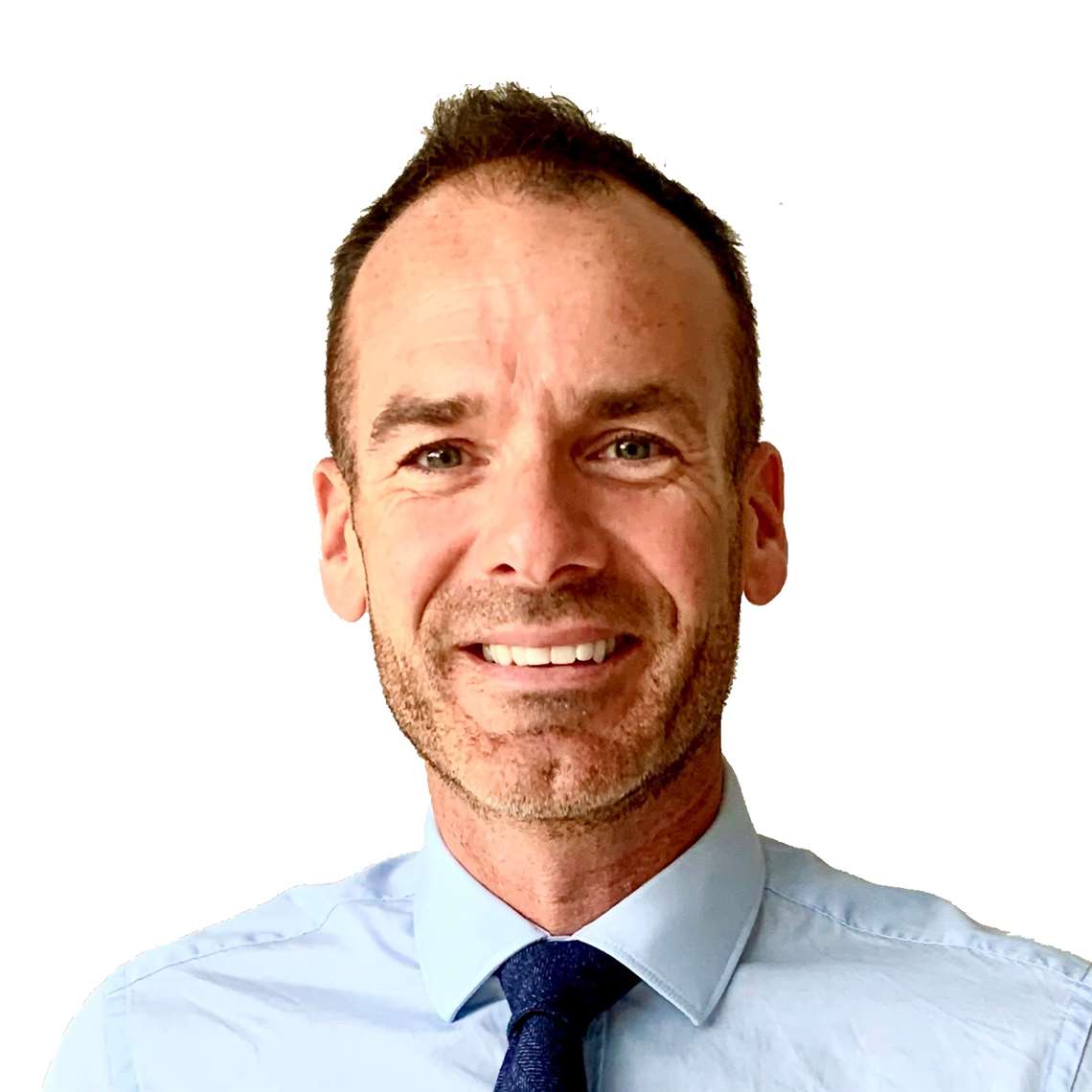
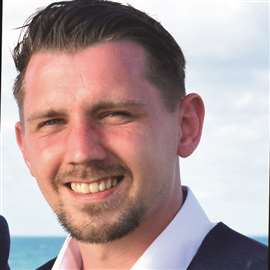