Trench success: IRN visits a Geneva project using rented shoring struts
03 February 2014
An unassuming apartment block project on the outskirts of Geneva is helping UK rental company Groundforce introduce its hydraulic shoring technology to the European market. Murray Pollok reports from Switzerland.
The private apartment block currently being built at Chêne-Bourg in the suburbs of Geneva will not – by the time the first residents have moved in by late 2014 – appear any different from the many others surrounding it.
If unremarkable in appearance, what does single it out as something a bit different is the technique used to shore up the deep excavation during construction – a set of 16 hydraulic shoring struts in two layers stretching across the 26 m wide site.
These massive struts – 0.61 m in diameter on the bottom layer and 0.51 m on the top – support the 12 metre deep excavation over its full 80 m length and are being used in place of traditional temporary steel frame shoring. It is the first time that the Swiss-based contractor Implenia has used the system and also its first application in Switzerland.
Jean-Pierre Binétruy, geotechnical engineer and project manager at Implenia’s foundations division, tells IRN that the company normally favours the tried and tested structural steel frames, in part because they know how to do it that way, but also because they already own the steel.
At the Chêne-Bourg site, however, space is at a premium, with the site bounded on one side by a busy road and on one of its long edges by an existing apartment building. So cramped, in fact, that the project offices have to be cantilevered over the excavation.
“It is a very difficult site and it will continue to be a difficult site until the end of the job”, says Mr Binétruy.
The block comprises seven storeys, including three basement levels to a depth of 12 m below ground level. This required a 0.6 m thick concrete diaphragm wall enclosing the entire 26 m by 80 m site.
Normally, Implenia, working with earthworks contractor HTP, would have progressively installed a steel shoring frame - anchored at the walls and with intermediate vertical columns placed on piles in the base of the excavation. This frame would have comprised a dense latticework of horizontal, longitudinal and vertical beams, making it difficult for the main building contractor Belloni to progress with the internal concrete walls and flooring slabs.
Instead, Implenia decided to try out hydraulic struts, a system that it first saw at a foundations exhibition in Piacenza, Italy, in 2012 where it was being displayed by Groundworks, the trenching equipment division of UK rental company VP plc.
Groundworks, which rents an array of trenching, shoring and piling products as well as the more sophisticated hydraulic struts, worked with Implenia and civil engineering design engineer ESM & Fiechter Ingenieries to come up with a design for the project. This comprised two sets of eight struts, the lower struts using Groundforce’s 250 t capacity MP250 units and the upper set comprising smaller, 125 t capacity MP125 units.
All 16 run in the same direction, with ample spacing between each vertical pair to allow for lowering of formwork panels and other building materials.
The struts were installed two at a time by Implenia, starting in mid-June, while the earthworks contractor used a Komatsu PC240LC with long digging arm - rented from French company ENCO - to excavate the clay. The struts were due to be removed in mid-November.
Mr Binétruy says the Groundforce struts would not be appropriate for simple excavation jobs, but in this case, the density of the steel frame structure would have made it very difficult for the contractor.
“There are two ways of seeing the time benefits”, he says, “For the contractor it has saved something like a week. And for us, it has taken just 20% of the time required to install a steel frame solution.”
There are other benefits. “For safety it is much better”, he continues, “The tower crane operator doesn’t have to think as much as with the steel frame. And for the client, [there is a cost saving because] we don’t need to use vertical support beams for a steel frame, and don’t need reinforcement of the concrete base slab.”
Installing and managing the struts has been straightforward. “We are used to hydraulics”, says Mr Binétruy, “so it has not been so difficult.” (The only minor issue has been the level of the second basement slab, which will require Implenia to raise the lower set of struts before the concrete is poured.)
Groundforce has installed strain gauges in the two struts adjacent to where the tower crane is sitting, which represents the ‘worst case’ loading. Implenia engineers have hand-held gauges, supplied by Groundforce, that show the strut loadings in real time.
The lower struts are measuring up to 90 t loads, including a 20 t ‘thermal’ load during hot weather when the steel expands. The upper struts, which connect directly to the capping beam on the concrete wall, are taking a basic design load of around 40 t. The struts are deforming by around 8 cm downwards due to the loadings, which is well inside the design limit of 12 cm.
Amsterdam-based Peter Richardson, an experienced piling and foundations engineer who is acting as a consultant to Groundforce in Europe, says the project is an important one; “It is an opening to a completely new market, with the biggest contractor in Switzerland, who are already talking to us about two new projects. It’s a significant project, but also a successful start.”
Mr Binétruy says he can envisage the Groundforce technology being appropriate for around half of the excavation jobs that Implenia undertakes. That could be good news for Groundforce, given that Implenia builds something like 90% of all basement projects in Geneva.
For David Williams, managing director of VP’s Groundforce division, the Geneva contract is another step towards his vision of introducing hydraulic strut shoring technology to the mainland European market, substituting the temporary steel frame solutions that are so prevalent there, and particularly in Germany.
Groundforce has been working on this for three years, with a European headquarters in Frankfurt and stock yard in Hannover already established. Projects have been carried out in Germany, Denmark and Italy (where it is working with local partner Interwell, a dewatering and excavations contractor).
“We have a number of contracts across Europe”, says Mr Williams, “We recognised the German market was most mature for trench shoring – the best place for us to put our feet down.
“There are basement projects all over Europe – it’s about finding the projects that the system will work best on. It’s not the best for every job.”
Groundforce has also been selling the technology further afield, with both United Rentals in the US and Coates Hire in Australia recognising the rental potential and adding the struts to their own rental fleets. (United Rentals in particular is expanding its specialist rentals activities, with trench shoring playing a key role in that.)
In Europe, Groundforce takes a hands-on role in projects, using its own engineers to come up with designs for particular jobs.
“I want our European business to be as big as Groundforce in the UK”, says Mr Williams, “We have an ambition to double Groundforce by expanding in Europe and would like to achieve that within five years. We can’t be reliant on UK GDP growth alone.” That would mean the division reaching annual revenues of £75 million by 2018.
That kind of lofty financial target, however, is not on the agenda at Chêne-Bourg, where the engineers sit in the cramped site office discussing the technical niceties of trench shoring.
One of them brings up the possibility of using struts to reduce the thickness of concrete diaphragm walls, thereby cutting material costs. David Williams is quick to spot an opportunity; “I like the idea of thinner walls and more struts…”
STAY CONNECTED
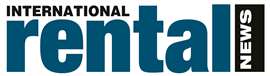


Receive the information you need when you need it through our world-leading magazines, newsletters and daily briefings.
CONNECT WITH THE TEAM
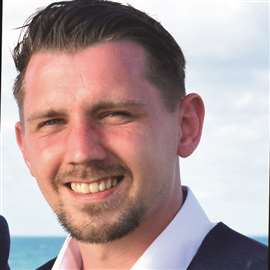

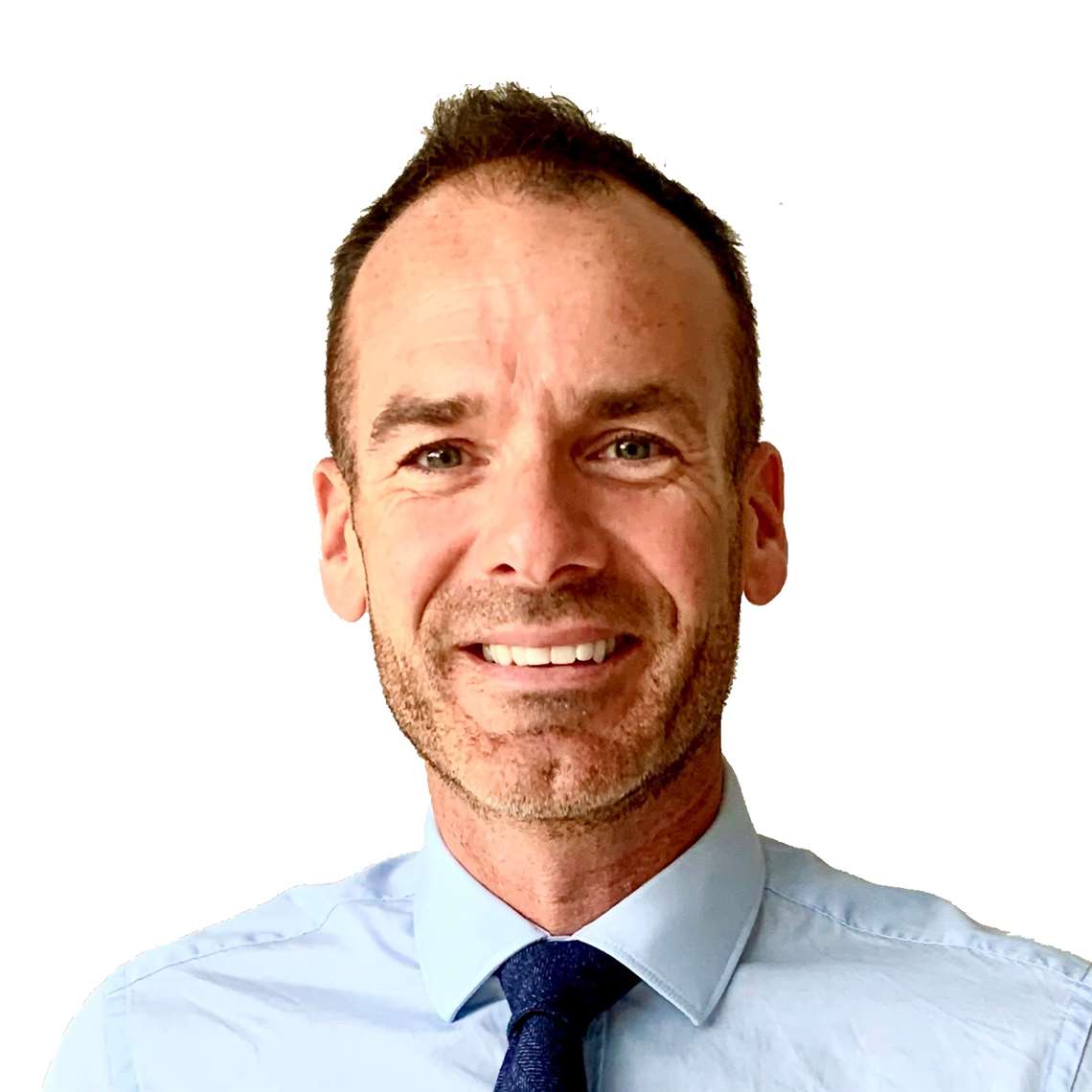