How can construction tackle the skills shortage?
17 October 2022
A hot global job market has put additional pressure on construction companies looking for talent – a key way to attract and keep them can be through upskilling, writes Jack Roberts.

The global construction industry finds itself in a rather odd situation. It is caught in a storm of disparate trends pulling apart the very sinews that hold a construction firm together: the ability to find and keep skilled, dependable workers.
On paper, it ought to be easier than ever for contractors and OEMs to attract young workers to their companies. Construction machines today are technological marvels with features that would have dazzled operators a decade ago.
Powerful new semi-autonomous guidance systems with 3D graphics combined with interactive, in-cab display screens now put precision control and high production within reach of even the most inexperienced operators.
And these very same systems can supercharge the capabilities of experienced operators – allowing them to post daily production numbers that would have been unthinkable on older machines.
The ‘office’ operators work in has also evolved tremendously. Most modern machine cabs feature ergonomically laid-out interiors, with 360-degree views, comfortable seats, heat, air and even stereos.
Hydraulic control systems reward an operator with a feather-light touch and modern coupler systems mean that operators rarely have to leave the cab to change attachments.
The work is out there, too. Construction markets worldwide today are generally robust with plenty of work available.
Markets have seen strong growth thanks to government investments in new infrastructure as well as renewal and repair. To meet these demands, construction firms are happy to pay good wages for skilled, dependable operators.
Attracting younger workers to construction
Despite this, young workers with the ability and desire to learn are hard to come by. Even in normal times, this would be a worrisome problem.
But, by an odd quirk in demographic timing, this young worker shortage is hitting the global construction industry at a time when older workers, highly skilled workers and operators are beginning to retire in large numbers, leaving owners with a vacuum in knowledge and skills.

“Naturally, this is a bigger problem in some global markets than others,” notes William Chimely, senior director, North America and global training and publications, Komatsu.
“In Asia, for example, operating a machine is seen culturally as a more revered, honored, role in a company. So, it’s difficult for a young person to get the training required to move into the cab of the machine.
“The bigger issue is that technical education for young people has fallen off all over the world. Trade schools and public schools used to provide elementary training for a career in trades.
“But we’ve migrated away from that with more of an emphasis on four-year degrees. So that talent pipeline that the industry used to depend on for new workers has dried up.”
Operating construction equipment
This sentiment is echoed by Jason Hurdis, global market professional, Caterpillar Global Construction and Infrastructure. “We have done amazing things to make the machines easier and more attractive to young people. But we now face numerous other challenges that are complicating things,” he says.

“The basic issue is simply attracting young people to this industry. That means finding a way to make it more glamourous. And really, that shouldn’t be hard to do. Because you can make a good living in skilled trades. The problem is, young people aren’t aware of that reality. We need to change that.”
Cat has been proactive in working to raise awareness about operating construction machinery.
In 2019 Cat debuted its Global Operator Challenge, which allowed operators from all over the world to compete for prizes and the honour of being named the top equipment operator in the world.
“We’ve got to raise awareness out there,” Hurdis says. “And Cat believes this global competition is a great way to do that.”
What are the benefits of a career in construction?
The operator shortage problem is one that will not resolve on its own – the industry needs to re-establish a talent pipeline.
But, given the dire state of affairs, it’s also time to begin looking for new ways to reach out to younger employee prospects as well.
“For companies, the key piece to this puzzle is recruiting,” Chimely says. “You have to find a person before you can even think about training them. And the sad fact is, our industry is not even on the radar screen for many young workers. We’re battling to catch their attention, and we have positive things we can point to.”
For instance, Chimley notes, construction offers a degree of versatility that is uncommon in many other occupations. Worksites change regularly.
Operators get to work outside and build things they can point to with pride later on. While the days of cold, wet workers, shoveling away have largely disappeared, that image is still fixed hard and fast in the minds of many young people.
“What you have to do is get out in front of these young people and tell them your story – the industry’s story,” Chimely says. “Start looking for new places to do that. A contractor in Kansas in the US recently set up a booth at a job fair and came away with five new operator hires. You have to go where the workers are.”
“There’s a certain type of young person who is going to be inclined to be a machine operator,” Hurdis adds. “Kids who like racing, ATVs, custom cars and motorcycles, for example.
“So go where they go. Set up booths at country fairs. Set up booths at car races, antique car shows or ATV races or motorcross events. Customers I’ve talked with tell me they’ve found great candidates in places like those.”
At the same time, Chimely argues that you’d do well to look beyond venues like that and seek out new prospects in unlikely places.
“Out of sheer habit, many contractors naturally look for certain types of people who have traditionally been attracted to construction machinery,” he says.
“In the US, that generally means white, rural, farm kids. But that demographic is not large enough now to fulfill our manpower needs. Construction globally needs to reach out and touch a new, diverse, future workforce. In many cases, this can mean inner-city children.
“Many of them are good gamers. And the ‘gamifcation’ aspect of operating modern construction machines fits in perfectly with those abilities.
“We just need to reach out to these young people and make them aware that construction offers them a viable career option using those skills. We can’t just keep fishing the same old pond forever. It’s time to diversify.”
Can education reduce the skills shortage?
Perhaps the biggest stumbling block to bringing new talent into construction is the lack of training to prepare young workers for even entry-level operating jobs.
Fixing this problem will be a long-term effort, requiring outreach to trade and tech schools on a local level from contractors, OEMs and dealers alike.

Another way to internally nurture talent is via the use of apprenticeship programmes, notes Thomas Lee, product manager, Doosan Infracore North America. “We are aware of apprenticeship programs available in North America for aspiring operators,” he comments.
“We encourage construction companies to partner with these apprenticeship programs and give new operators the opportunity to cut their teeth on the latest heavy construction equipment.”
Lee adds that dealers play a role in continuing education of heavy equipment operators. “We are aware of dealers within our organisation who regularly work with their customers to provide not only equipment operation training but the dealers also train operators on how to properly service the equipment.
“Much of this training is done during the company’s off season or slower times of the year,” he says.
New ways of training workers are having a tremendous impact on quickly providing untutored young people with the skills needed to be an effective machine operator. Among the most powerful of these new teaching aides are machine training simulators.
Every equipment operator, regardless of skill level and experience, comes to the table with different strengths and weaknesses,” explains Alan Limoges, product manager construction, CM Labs Simulations. “The key for employers in battling the labour shortage is to meet those people where they are.
“Construction equipment simulation is one way to both onboard entry-level operators and cross-train, benchmark, re-train, or upskill existing operators.”

Limoges says that today’s simulators are data and analytics-driven, which is essential to optimising training time and correcting unsafe behaviors.
This means that training techniques move away from a checklist approach, and instead target specific skills that make people more efficient and safer.
“Companies and trainers now can use data collected for each student to analyse past behavior and then apply that information to create specific learning paths that develop the most appropriate skills,” he notes.
“This approach also makes training more personal. With data analytics, training can tackle skill deficiencies for each person, which elevates their individual skill sets to a much higher level, rather than applying a single learning objective across an entire classroom.”
Mentorship programs in construction
Once an employee has been identified as a promising prospect and received some basic training to get them started on a machine, Reome says providing them with an older, experienced partner who can act as a mentor is one of the simplest, yet most powerful, training tools available at virtually every construction company in the world.
“Establishing a mentorship program is so important,” he stresses. “Because that’s how you impart passion about the industry and the work to a young employee. It’s a simple way to set a young person on a positive career path and keep them on it.”
There is a final – yet critical – aspect of finding employees that cannot be overlooked: pay. “Wages and salaries are leading indicators for how well an industry can recruit workers,” Chimely says. “Construction has been lagging behind other industries. We’re in a hot global job market right now. A rising tide lifts all boats. And workers – quite simply – are going to go where the money is.”
Construction has a bright future to offer new workers – what is vital is that the sector ensures that this message is heard around the world.
STAY CONNECTED
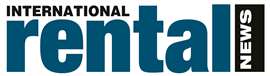


Receive the information you need when you need it through our world-leading magazines, newsletters and daily briefings.
CONNECT WITH THE TEAM
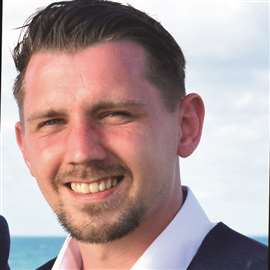

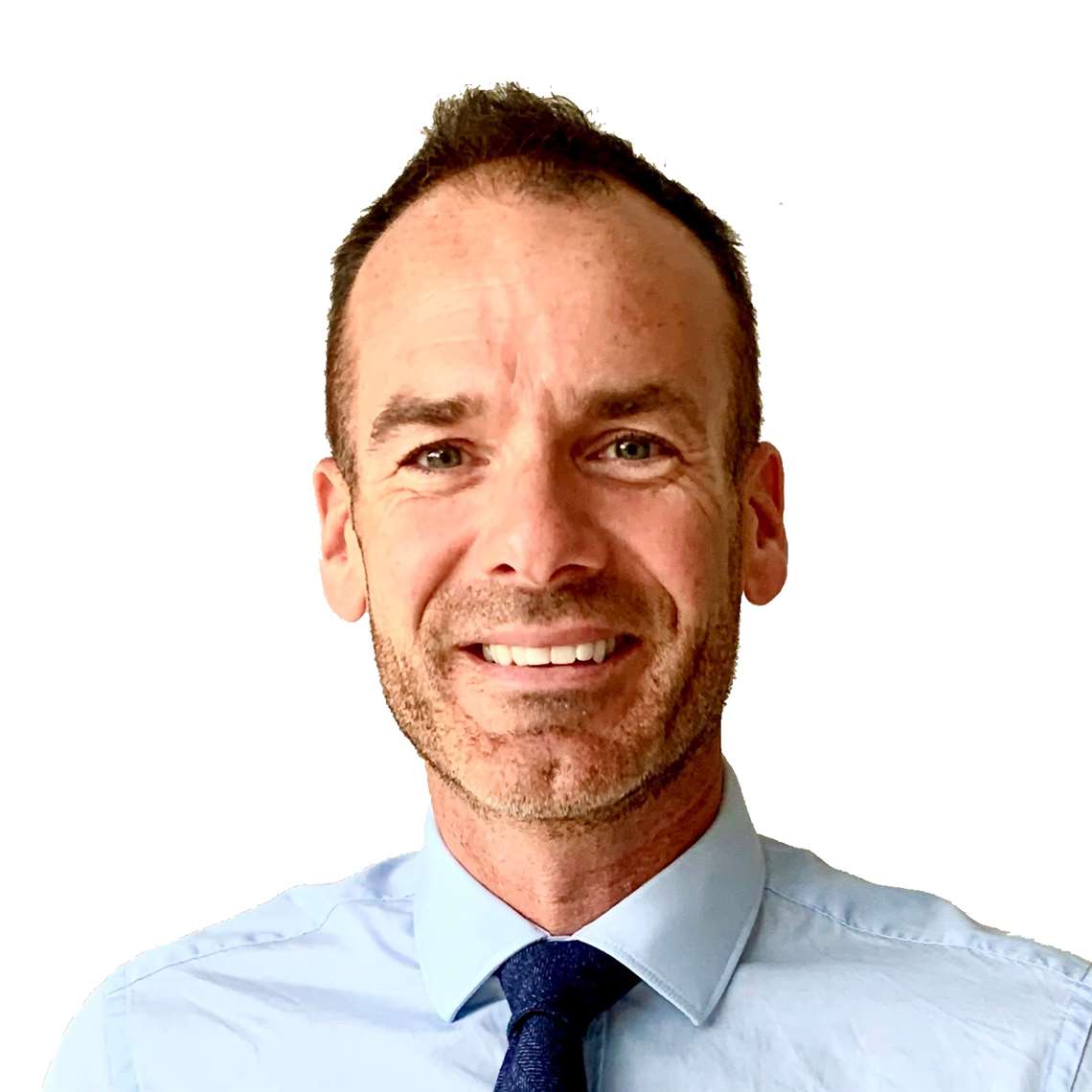