Can retrofit electrification really work for construction equipment?
20 June 2023

As construction equipment manufacturers continue to widen the range of electrically powered machines, some companies have started to explore retrofitting existing diesels to make them electric.
Earlier this year, Manitou Group announced that it had signed a deal with rental company Kiloutou to retrofit used diesel telehandlers with electrification kits.
Meanwhile, in the US, Alta Equipment announced late last year that it was launching a new business segment called eMobility, which aims to convert truck fleets and heavy equipment to electric power.
The idea has obvious benefits. Not only can machine owners reduce their carbon emissions but extend the life of their equipment at the same time.
Manitou’s initiative is still in the early stages. Over the next two years it will test the technical and economic feasibility of electrifying telehandlers, with the first phase being carried out on a high-reach telehandler in Kiloutou’s rental fleet.
The company is in the process of dismantling and reassembling it with an electrification kit before testing it in real-life conditions.
After that, the company will extend the electrification kits to other machines in the Kiloutou fleet in 2024.
A viable alternative?
So could retrofit electrification work across different machine classes in the construction sector?
And could it provide another viable alternative when it comes to reducing carbon emissions?
It should be technically feasible for most types of machines, says Alex Woodrow, managing director at KGP, a specialist automotive technology consultancy.
“If it’s a fully hydraulic machine, then it is fairly straightforward,” Woodrow says.
“You could electrify it by taking the engine out and the pump which would have been driven by the engine, and replacing it for an electrically driven pump, batteries, an inverter to run the motor, a motor of some sort to drive the pump and an on-board charging system.”
Woodrow also sees the potential to do this for nearly all types of machines. He points to the mining sector where rigid dump trucks offer a lot of space for a retrofit kit once the engine has been removed.
A lot of the machines are also diesel electric, in the sense that the diesel engine acts as a generator but the final drive is electrically driven, making a conversion easier.
And he can see the potential to do something similar with excavators used in underground mining, which are often fully hydraulic.
An obvious win in mining equipment, in addition to reduced carbon emissions, is the fact that electrically driven machines will improve air quality at the same time as keeping expensive machinery running for longer – an important consideration when air handling is typically 50% of the cost of an underground mine.
However, there won’t necessarily always be the same level of incentive in construction applications.
“On the compact side, you would probably go for a dedicated electric machine already,” says Woodrow.
“For larger machines you would do it on a case-by-case basis.”
He can see a use for machines like specialised wheeled excavators for use on railways, where electrically powered alternatives don’t currently exist, for example – machines with conventional engines could be bought now and retrofitted later.
But he is more sceptical about whether it would be worth it for mid- and large-sized machines with a transmission like a wheeled loader, where some manufacturers already offer electric machines.
Meanwhile, in the materials handling sector, a new tethered electric machine, which will be cheaper because it doesn’t require an expensive battery, may also make more sense than attempting to retrofit an old used machine.
In fact, Woodrow generally sees the case for retrofitting construction machinery with electrification kits as fairly limited, perhaps taking a share of the market in low single digits in percentage terms.
“I think there are cases where it might work, if it’s a really expensive, niche machine and you want to extend its life. It might make sense for some larger construction equipment. And if you’ve got a big fleet that’s got low hours then you might consider it.
“But I think increasingly a new off-the-shelf electric machine would be the most cost effective,” says Woodrow.
Incoming legislation could make retrofit less attractive
Meanwhile, Woodrow raises the prospect of incoming legislation governing battery durability could make the case for retrofit electrification less attractive.
Work for such legislation is currently underway in Europe, with plans for a battery passport – a digital record system that will list information about every industrial or electric vehicle on the EU market with a capacity over 2kWh. Data will be required from a host different parties including battery producers, automotive OEMs and repurposing companies.
Legislation isn’t yet planned for non-road applications but Woodrow expects it to follow. “Retrofit may sound appealing to start with but when you look into all the details, I think the cost and complexity involved for a small share of machines will be prohibitive,” he adds.
STAY CONNECTED
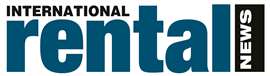


Receive the information you need when you need it through our world-leading magazines, newsletters and daily briefings.
CONNECT WITH THE TEAM
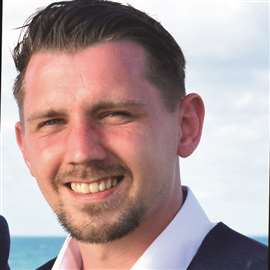

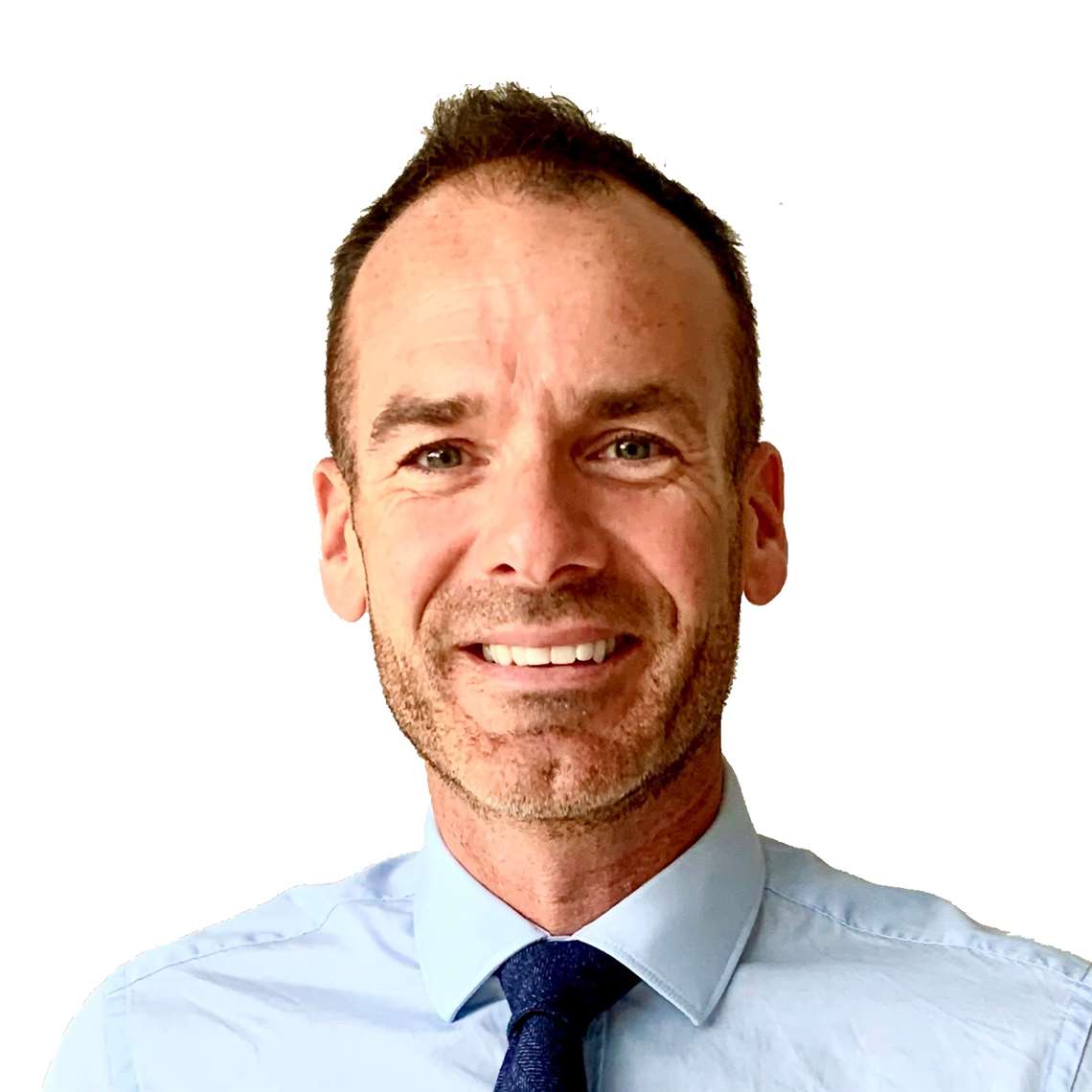