3 key takeaways from the ag equipment electrification roundtable at Agritechnica
30 January 2024
While diesel engines remain the dominant sources of motive power for agricultural equipment, electrification is making inroads.
At Agritechnica 2023, Power Progress brought together industry leaders to discuss the current state of ag equipment electrification as well as its future in a roundtable discussion entitled, “Electrifying Agricultural Machines: The Quiet Revolution.” While much was discussed, and the entire roundtable discussion is available for viewing, here are three key takeaways from the event.
1. Electrification is currently most viable for equipment rated 125 hp or less.
Noting that Monarch Tractor’s Mark V all-electric tractor is currently being used primarily in vineyard and orchard operations, roundtable moderator Julian Buckley, editor of Power Progress International, asked Monarch president and co-founder Mark Schwager about the future for larger electrified tractors that could be used for more row crop applications, given that the heavier batteries required could counteract any power benefit.
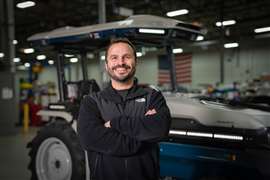
“Where we think the technology is applicable today is everything around under 125 horsepower,” Schwager said. “We can get the power/energy/weight equation correct.” He added that “90% of the market globally is below 100 horsepower,” making that portion of the market applicable for electrification.
That’s not to say 125 hp will always be the electrification ceiling for ag equipment. Schwager said technology advancements will eventually allow the limit to increase. “Typically, what you see in battery energy density improvement is 50% every five years at the cell level. Of course, there are things you can do at the pack level, as well, to increase that efficiency, and that is both on the volumetric and gravimetric side. But the intracell technology is the most important thing for increasing that energy density. So we do see the opportunity to bring it into larger and larger pieces of equipment.”
2. Automation and data collection mean electrification is about more than just net zero emissions.
David Stockbauer-Muhr, head of electric systems development, off-highway for ZF said that unlike with internal combustion engines (ICE), electrified powertrains can provide more actionable data, such as for predictive maintenance.
“The point is, with electric machines you will always get the information — how high the torque during the operation is, for example, also the speed,” he said. “And you can get out the data — how long this electric machine, for example, for the driver, is working over the operation hours. With the diesel engine, it’s not possible because the diesel engine drives the whole complete system. And then this is only some working activities — it’s not the same like driving. So out of this data, you can expect when the transmission is ready for some maintenance and such things.”
Regarding Monarch’s Mark V tractor, Schwager said the product’s future lies not in new features but in how it can gather and provide additional data. “I think that the big difference is how can we make the data that the tractor collects while it’s going around — without cost for fuel, without cost for labor — add value to the farm and collecting data, providing insights to farmers. That’s the next step on how not only we can add value using the automation, which is probably the most immediate value. How do we have year-over-year insights? How do we have actionable insights from the moment that the data is collected, where the farmer not only can understand what the tractor has received, but can give direction to the tractor to go perform? That’s the difference.”
3. Charging infrastructure challenges must be addressed to encourage adoption of electrified ag equipment.
An audience member asked the panel its thoughts in addressing charging issues specific to electrified ag equipment. “You always say, ‘We sell electric tractors,’ but we can’t power them on,” they said. “The stronger the battery, the longer it takes to put electrified energy in it, and it’s very expensive.”
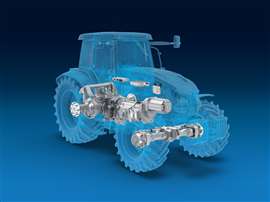
Schwager said Monarch has acknowledged the infrastructure limitations on farms in its tractor design. “Monarch did not choose to integrate DC fast charging on its tractor,” he said. “Why? There are no superchargers on farms. It doesn’t exist. What does exist on farms and in barns is a 220 V plug used for welding. That’s the available infrastructure today.”
He added that limitation required Monarch to develop a swappable battery, which accommodates the infrastructure while allowing for continuous operation.
“A 220 V architecture at 22 kW in Europe means that we have a five-hour charge time,” he said. “That doesn’t really work if you have to go 24/7. That’s why we have a swappable battery.”
Kari Aaltonen, director of engineering for AGCO Power, said AGCO has a demo of a microgrid concept for the specific purpose of addressing charging infrastructure on the farm. “Because there might be windmills, there might be solar panels, the generating of a diesel generator, batteries, to connect the energy sources and also the energy consumers, including the tractor,” he said. “That’s exactly the reason we want to support our farmers. We are not yet there, where we have to be in the future, but we are working on it.”
STAY CONNECTED
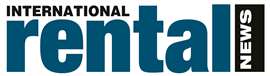


Receive the information you need when you need it through our world-leading magazines, newsletters and daily briefings.
CONNECT WITH THE TEAM
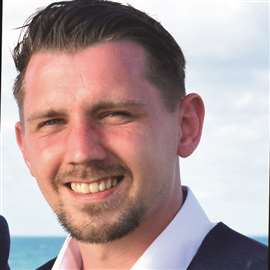

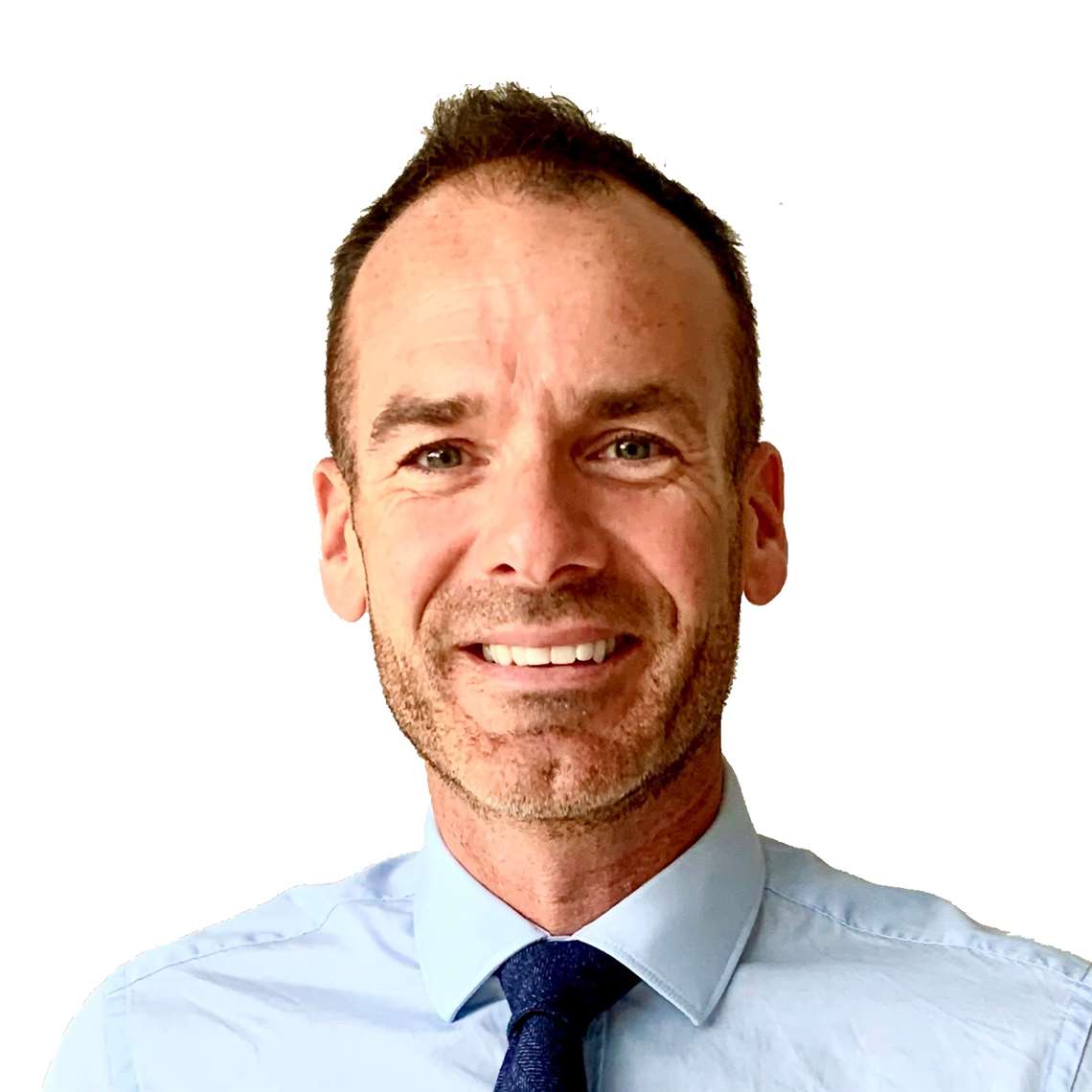