A history of machine control: part two
10 February 2023
This is the second part of an article on machine control, to read part one click here.
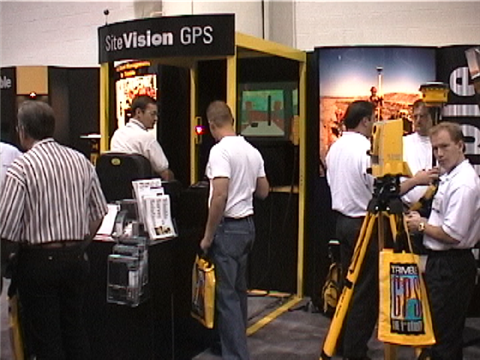
In brainstorming sessions, Trimble application engineers came up with the idea to put two receivers on the blade – making way for the Moving Baseline RTK technology.
Mark Nichols, then Trimble’s general manager for construction, remembers how that came about. “At the time, we had developed moving baseline technology for Japanese car manufacturers to truth the newly developed dynamic cruise control system.”
In traditional RTK, operators use a static base on a known point with rovers moving relative to the static base for centimeter accuracy. For the cruise control truthing, the engineers had the base move. A receiver was placed on a pace car and the vehicle with cruise control.
With the RTK positioning, the manufacturer can see a centimeter-accurate vector between the two units, and can subsequently calculate a precise heading from the vector – thus validating the cruise speed set by the cruise control solution.
Soon after, Trimble introduced BenchGuide, essentially a GPS-based leveling system for mining. This technology utilised off-the-shelf Trimble hardware and cabling to provide a shovel operator a centimeter level height on the bench of a mine.
Bryn Fosburgh, who joined Trimble in 1994, added, “The unique part of this system was that we used developers from our survey controller team to develop at the time an easy to use and intuitive user interface that made it effortless for a shovel operator to utilise the system.”
Machine control and civil construction
Then they moved to civil construction. On a piece of heavy equipment, this same system (two receivers on the blade) could be used to measure the vector across the blade providing slope and rotation. One receiver provides centimeter positioning of the blade, and the moving baseline algorithm provided the slope of the blade and how much it had rotated in any direction.
By 1999, the team was ready to test in the field, and Arthur Taylor, another key member of the development team, provided the venue – his father’s construction company, Taylor Contracting. “We put it on a grading machine to test and could immediately see that it sped up iterations and design changes,” said Nichols.
The first official commercial deployment of the system, which cost US$50,000, was in Elgin, Illinois, in August 1999 on a John Deere 750 dozer. The operator was a 55-year-old man who had never used a computer in his life. Kurt Maynard, [Field Engineer] and current business development manager at Trimble, recalled, “He was confident in his laser system, but wary about the GPS. After 30 minutes of verifying the GPS versus his paper map, he threw the maps off the back of his bulldozer and continued on with GPS.”
“It was a huge step for the industry,” Nichols added, “We advertised the system as a stakeless grade control system. The first customer would only buy the system under the condition that he could get his money back. The system was installed, and two weeks later he called to buy another one. That’s how well accepted the technology was in the industry after a short time.”
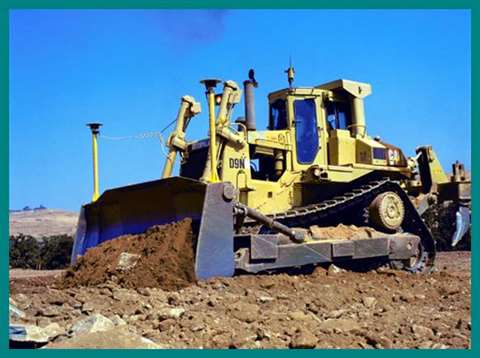
The system offered compelling benefits. It gave the operator a degree of independence and flexibility, reduced rework, fuel consumption, machine operating hours and had a measurable ROI. Productivity improvements ranged from 15-25% depending on the application.
“As soon as someone tried it, they bought it,” added Nichols. Trimble would introduce its first GPS based stakeless grade control system at ConExpo in 1999.
In 2000, Trimble acquired Spectra Precision, a move that would expand the company’s machine control portfolio to include the automated blade control with robotic total stations. Soon, these talented engineers would combine innovations to deliver an automated 3D grade control system initially on a dozer, then a motor grader and, more recently, on an excavator.
However, before spotlighting more recent advances, no machine control story would be complete without reference to Caterpillar – and the ultimate goal to remove the need for survey stakes.
Caterpillar’s new technology
Caterpillar has been an innovator in the big machine world since its founder invented the first commercially successful track-type tractor in 1904, the diesel engine and the radio remote-controlled track loader for slag removal in 1968.
Years later, the RTK research contract from the 1990s with USACE helped facilitate the company’s innovation in 3D machine control with GPS in parallel with Trimble’s efforts.
Caterpillar’s research program reached a point where it had very advanced software running on the machine and good back office support, but the R&D team needed a commercial GPS partner. They picked Trimble because they could get the GPS receiver as well as the two-way wireless communications system. That led to the development of the Computer Aided Earthmoving System (CAES) for bulldozers and excavators, which was first introduced Black Thunder Mine in Wyoming in 1995. The system showed if the operator was above or below grade, but didn’t control the blade automatically.
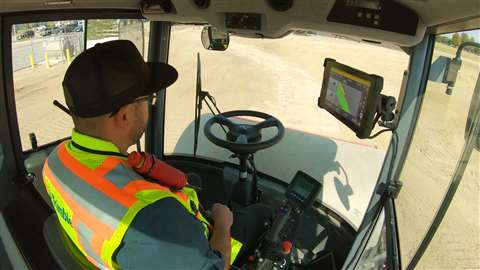
“This happened to be with a very progressive customer who already used our GPS survey equipment to more efficiently put in survey stakes,” recalls Fosburgh. “The preproduction machine control system eliminated the stakes altogether. This was the start of a big shift, where the surveyor’s role on projects started to become more like that of a data manager.”
Forrest added, “While this effort validated that machine control was a real possibility, it also drove Trimble to improve the field-readiness of our solutions to work in rugged mining and construction environments.”
That early partnership would form the basis for the formation of the Caterpillar Trimble Control Technologies (CTCT) in 2002 to develop machine control and guidance products for both the mining and construction industries, for factory or aftermarket installation on any make or model of equipment regardless of manufacturer.
What next for machine control?
The advancement of machine control continues, now with greater focus on increased automation of other elements with a clear eye on autonomy.
For instance, Dynapac and Trimble partnered in 2020 to develop commercial-ready autonomy functionality for Dynapac soil rollers that include automated steering and speed functions. In 2022 Trimble introduced Horizontal Steering Control functionality, becoming the industry’s first automatic steering control solution for soil compactors, further addressing the global labor shortage with automated workflows that deliver the quality of highly trained operators.
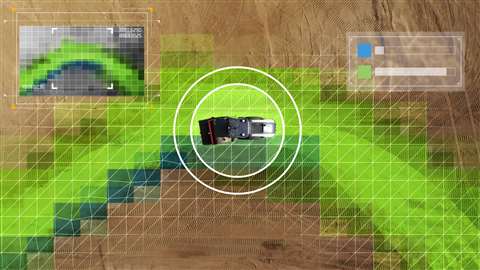
Add in advancements that range from autonomous self-levelling and blade control systems to unmanned paver fleets and it’s clear that the industry is well on its way to achieving unprecedented operational improvements. Embedded AI, machine learning and 5G are enabling the development of ‘expert operator’ machine automations, and broadening the applications of machine control systems.
It’s an evolution that the early innovators of machine control could have only dreamed of. In 2000, after Trimble had committed to GPS-enabled machine control technology, Forrest envisioned the future. “We knew there was a benefit to controlling grade, but we knew even then it was just a foundational step,” he said.
“We have always imagined a scenario where all of the machines on the jobsite talk to each other in real-time – and that crews could receive real feedback about their work. We’re doing that to a great extent in mining. However, in construction space, it’s not embedded in the workflows – yet. We have the technology and the mindset to fully automate the construction continuum just like we imagined 20 years ago.”
STAY CONNECTED
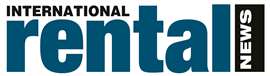


Receive the information you need when you need it through our world-leading magazines, newsletters and daily briefings.
CONNECT WITH THE TEAM
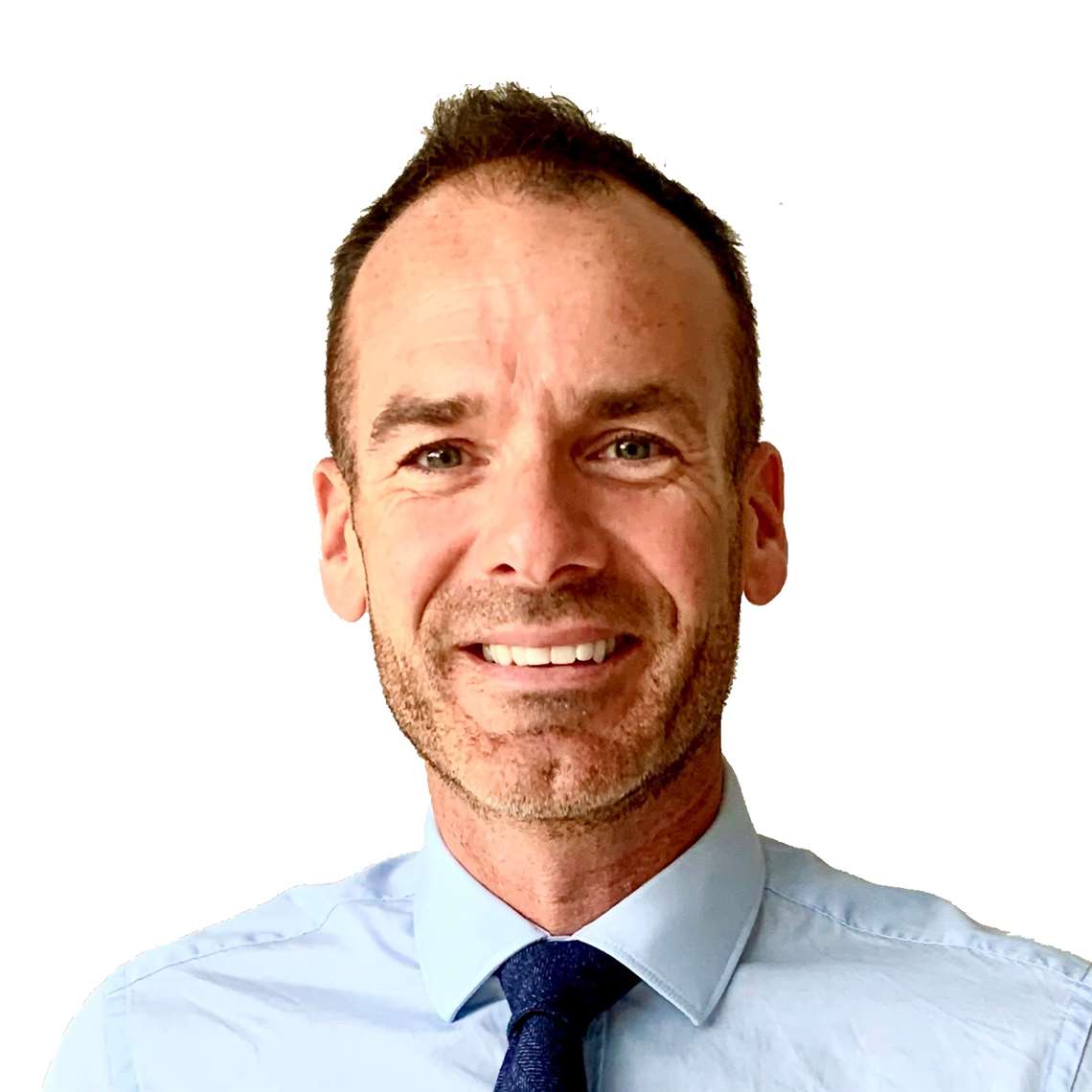
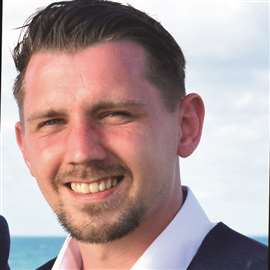