Can hydrogen engines turn construction green?
14 September 2021
Hydrogen combustion engines move to centre stage as construction aims for zero emissions, reports Graham Anderson
“We were thinking of the electric job site; now we are thinking of the hydrogen job site.” Those words of Tim Burnhope, chief innovation and growth officer at JCB, underline just how quickly strategies are changing as construction battles to minimise its environmental impact.
He was speaking about JCB’s work on a zero CO2 emissions hydrogen combustion engine, a development he believes will play a pivotal role in construction’s progress towards a more sustainable future.
The UK-based OEM has built and is currently testing a prototype backhoe loader with a new hydrogen motor. JCB is using and adapting established engine technology with readily available components: once the hydrogen is ignited the power is delivered in exactly the same way as in a diesel engine.
The result is a backhoe loader than can do everything its traditional diesel powered relative can do and behaves in the same way – with fuel costs that are expected to be very similar to diesel. Boringly normal, you might say.
That normality is something that excites its JCB developers. After all, if its customers do not adopt the technology, then we will not be making progress
“Our customers say only two things – don’t make it too complicated and don’t make it too expensive for the market they serve,” said Burnhope
Advantages of hydrogen
JCB’s hydrogen combustion engine has roughly the same size, weight and usability of its diesel equivalent which means the existing equipment does not have to be significantly redesigned and the operator training required is negligible. However, but there is still a long way to go yet, as Burnhope himself acknowledges.

“Our starting point was how do we leverage our expertise into hydrogen. There is a way to go to get it into production, but so far nothing that scares us,” he comments.
“The next step is to get to the market with some experimental products. We are looking to have products out there with some customers so that they can use them experimentally, for feedback and analysis. We reckon at the moment that we will be using these engines across our range, from mid-range backhoe loaders and telehandlers – about three or four tonnes upwards.”
Hydrogen power
The company’s journey towards the hydrogen combustion engine started with a challenge from chairman Lord Bamford which resulted in the creation of a specialist development team at its Power Systems factory in Derbyshire, UK.
JCB had long been working on clean diesel engines – according to the OEM, the diesel engines it makes today produce 50% less CO2 compared with machines manufactured in 2010. There are even more dramatic reductions in particulates and nitrogen oxides compared with 1999 levels.
The OEM has already launched a successful electric mini excavator and now has fourteen different models in its compact equipment range powered by lithium-ion batteries including telescopic handlers, scissor lifts, dumpers and forklifts. Then, in 2020, it developed a 20 tonne tracked excavator powered by a hydrogen fuel cell.
In a fuel cell, hydrogen and oxygen are combined to generate electricity, heat, and water.

Fuel cells that use pure hydrogen fuel are completely carbon-free, with their only by-products being electricity, heat, and water. This is fantastic for sustainability, but both batteries and fuel cells have their limitations.
JCB says that batteries are not practical for equipment with an operating weight of over six tonnes, such as backhoe loaders and large excavators. The batteries would weigh too much, cost too much and result in a loss of machine performance.
At the same time, fuel cell technology has unresolved technical and cost issues combined with concerns about security of supply.
“To be clear, we are not saying that fuels cells will never take off, but there is a long way to go. We have to be so careful that we do not go through iterations of design that mean the final products are not available until, say, 2050. We have to start reducing CO2 much, much quicker,” says Burnhope.
“The future is going to be about using the right solution for the right equipment. Low hours, low usage it will probably a battery. Bigger machines working in more remote locations where recharging is more difficult – the industry will probably be looking at other solutions. Then we think hydrogen will come into its own.
“It looks to us like there will be a fragmented market for batteries, fuel cells, hydrogen combustion –
with a market for each, depending on application. We are open-minded to all technology that can help us on the road to zero CO2, but we believe that hydrogen combustion will get us to zero CO2 a lot faster.”

To date, JCB’s hydrogen combustion prototype has been running for a couple of thousand hours and the company intends the design life to be at least the same as its diesel equivalent.
The JCB developers have been liaising with academic engineers and metallurgists on aspects of the engine development while trying to perfect the fuel mix. The result is a turbo-charged internal combustion engine with a fuel-to-air ratio of one part hydrogen to 100 parts air, a solution that is delivering zero emissions and exciting early results.
So far, the capacity of the hydrogen tanks on the current prototype backhoe are, in the words of one of the engineers, probably not quite enough to do a full day’s work. It is worth pointing out though, that it is a first prototype machine and there is a lot of development and learning still to do.
Obviously, one option to consider is increasing the capacity of the fuel tanks, but further improving machine efficiency through design changes could reduce the amount of fuel required, an approach that can be applied to all types of machine, regardless of what fuel they use.
What are the supply chain issues?
Perhaps the biggest obstacle to the successful commercial development of the hydrogen combustion engine will not be the engineering or technical challenges, but political and regulatory support combined with the need to establish relationships with new suppliers.
Certainly JCB is keen to see the development of a hydrogen sector that will spur the growth of the necessary supply chains. According to Burnhope, “We are not looking at this as a sales opportunity to other manufacturers; we are doing this in the hope that others will look at what we are doing and will get involved.”
Hydrogen’s potential to help combat climate change has only been fully recognised in recent years. For a long time it was more or less ignored by regulators and politicians alike.
Yet the potential of hydrogen combustion engines was first recognised over 200 years ago.
In 1806, French inventor Francois Isaac de Rivaz designed the first internal combustion engine which ran on a hydrogen/oxygen mixture.
In the many decades since, dozens of automotive visionaries, inventors and engineers have flirted with hydrogen combustion engines, but none have been developed commercially.

Today, JCB’s enthusiasm for the technology is matched by some of the biggest names in construction and beyond. Those working on hydrogen combustion engines include Liebherr, engine manufacturer Cummins, German engine development specialist FEV, UK engineering consultants Ricardo and aerospace giant Airbus. Even Formula 1 is looking at it.
All hope that their innovation and commitment means a global market can be successfully developed. Liebherr has said little about its work to date, but Cummins announced in July that it has begun testing a hydrogen-fuelled internal combustion engine.
“We are thrilled about the potential of the hydrogen engine to reduce emissions and provide power and performance for customers,” said Srikanth Padmanabhan, President of the Engine Segment at Cummins.
“We are using all new engine platforms equipped with the latest technologies to improve power density, reduce friction and improve thermal efficiency, allowing us to avoid the typical performance limitations and efficiency compromises associated with converting diesel or natural gas engines over to hydrogen fuel.
“We have made significant technological advancements and will continue moving forward. We are optimistic about bringing this solution to market.”

As a next step, the company plans to evaluate the engine in a variety of on- and off-highway applications and said that hydrogen engines offer OEMs and end-users the benefit of adaptability by continuing to use familiar mechanical drivelines with vehicle and equipment integration mirroring that of current powertrains.
European Clean Hydrogen Alliance
FEV, the leading international vehicle and powertrain developer based in the German city of Aachen, is another company going in the same direction. This is partly as a response to the European Union initiating the European Clean Hydrogen Alliance in 2020 with the aim of creating an integrated hydrogen market by 2030.
The EU’s move revived the debate on what would be the most appropriate way to use hydrogen and FEV has reached a similar conclusion to JCB. “The hydrogen internal combustion engine is a robust, cost-efficient option for zero CO2 transport. It can be implemented into the current production infrastructure relatively simply and offers potential for existing vehicles,” said Professor Stefan Pischinger, President and CEO, FEV Group.
Because hydrogen is a carbon-neutral fuel, only minimal amounts of carbon monoxide, carbon dioxide, and soot are produced from burnt lubricant. The main exhaust gas component is nitrogen oxide (NOx), but its low exhaust gas temperatures mean that – even without exhaust gas aftertreatment – the level of nitrogen oxide is already below the current limits.
Like JCB and others, FEV says that further research is needed, for example into the ignition system, crankcase ventilation, the fuel mixture and exhaust gas treatment. All companies involved want to see the engines tested long-term in working conditions onsite to flush out any concerns that have so far not come to light.
The possibility of hydrogen embrittlement – when metals can become brittle as a result of the introduction and diffusion of hydrogen into the material – is one subject of concern, although there have been no problems reported to date. Green groups also point out that the environmental benefits of developing hydrogen combustion engines depend on how the hydrogen is produced.
So-called blue hydrogen is derived from natural gas and its manufacture produces CO2 as a by-product, which has to be captured and stored. As a result, opponents argue that the uncertainty surrounding the storage technology means blue hydrogen is not a zero-emission fuel and should not be promoted as such.
On the other hand, green hydrogen is the production of hydrogen from renewable energy through electrolysis, a process that splits water into its basic elements – hydrogen and oxygen – using an electric current. The electricity used in the process can come from renewables such as wind, hydropower and solar energy.
Hydrogen combustion engines
Apart from the availability of green hydrogen, bigger obstacles are likely the need for political support, effective regulation and the establishment of crucial supply chains with new commercial partners. As one of JCB’s development engineers observed, “we are making a lot of new friends”.
The OEM is optimistic that supply chains will develop and that hydrogen production can be ramped up sufficiently to meet future demand, encouraged by reports of the many major corporations looking to enter the market.
But governments and regulators will need to agree international standards and rapidly develop policies for hydrogen production, distribution and storage. JCB Chairman Lord Bamford has stressed that opposition to fossil fuels should not lead to a blanket rejection the internal combustion engine in all its forms.
He said, “We believe that there should be continued use and development of internal combustion engine (ICE) technology; the use of fossil fuels in machinery may be phased out in the future but that shouldn’t mean that ICEs don’t have an important on-going role in helping to reach zero carbon dioxide emissions.”
One of the many organisations watching developments closely is ESTA, the European association of abnormal road transport and mobile cranes. Its members work on major construction, energy and industrial projects.

ESTA director Ton Klijn said, “The development of hydrogen combustion engines is very exciting. We can only hope that our political leaders in Brussels and EU member states keep up with the pace of change.
“If industry is to develop the new supply chains that will be required, we will need our politicians to show clear thinking and leadership – and that means agreeing the necessary regulatory frameworks and harmonised standards.
“We know from bitter experience – and our long campaign for harmonised European standards in abnormal transport – that such aims are far easier to debate than deliver. We can only hope that the climate emergency will induce a much greater sense of urgency.”
Without such agreements, the huge strides made by JCB and others in the construction and off-highway sector could well be in vain.
STAY CONNECTED
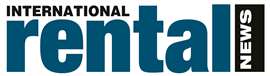


Receive the information you need when you need it through our world-leading magazines, newsletters and daily briefings.
CONNECT WITH THE TEAM
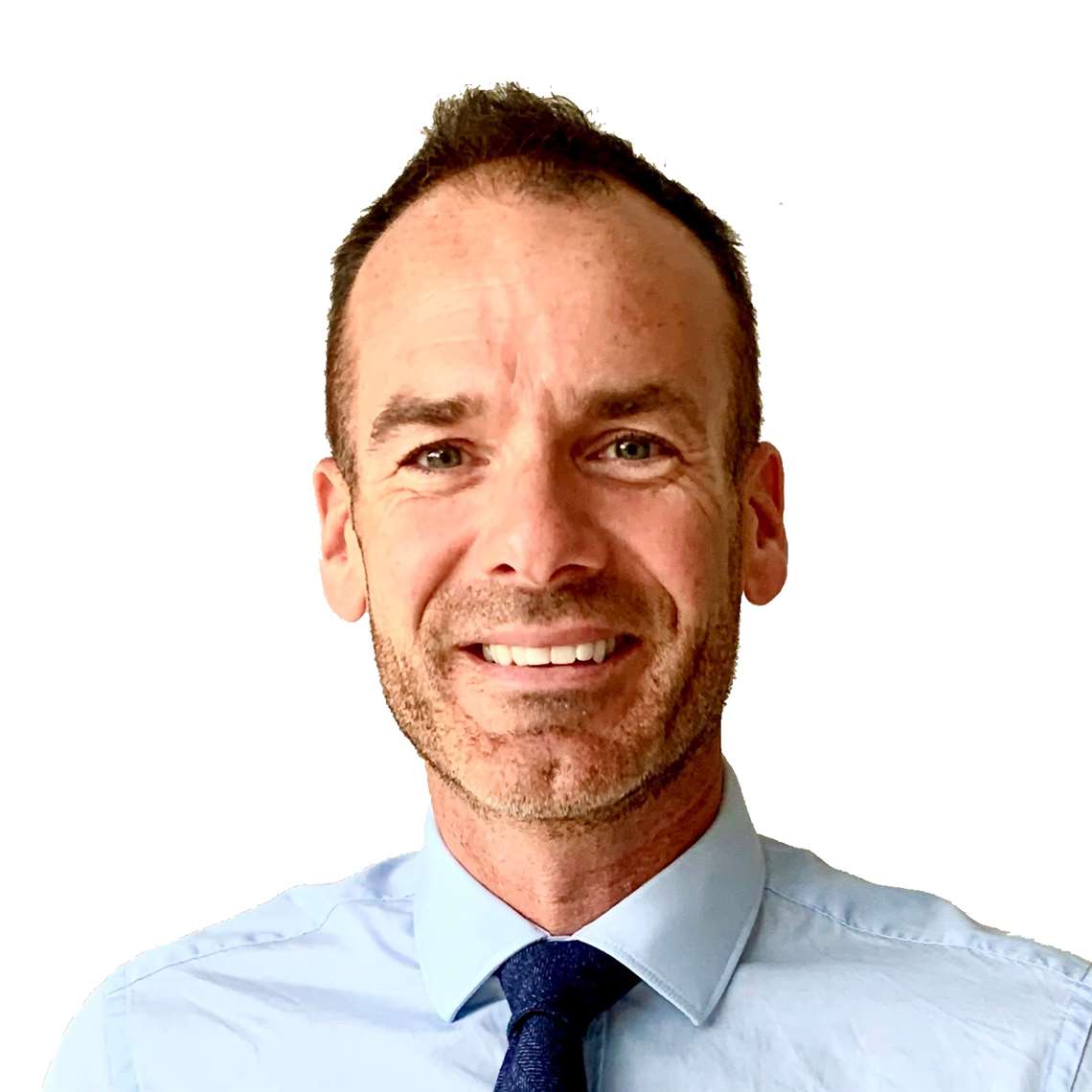
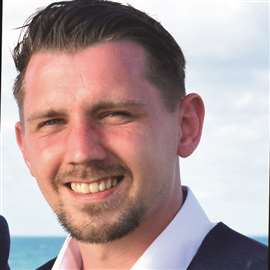