Caterpillar’s passion for paving

Partner Content produced by KHL Content Studio
20 June 2024
The European Commission recently estimated that – taking into account motorways, secondary and local roads – Europe’s road network totals a little over 19 million kilometres.
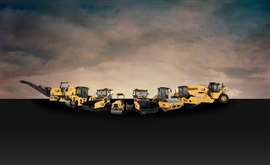
Incredibly, much more is needed; the Trans-European Transport Network, known as the TEN-T, calls for many more roads as part of a policy to develop a more efficient transport infrastructure across the European Union.
High-quality highways are demanded, and there is a sense of urgency, with European authorities targeting completion of the core network by 2050.
At the same time, there are major problems with ageing road networks across Europe, and road rehabilitation is required at an increasing rate.
To deal with the huge demand for new roads and road repairs, construction businesses are investing in equipment that can efficiently deliver smooth, consistent surfaces.
And as materials prices continue to rise and the skilled workforce diminishes, construction businesses are looking to reliable and productive equipment, to ensure maximum profitability on road projects.
These machines often need to be robust enough to cope with the rigours of roadwork applications at altitude, in extreme weathers and on challenging terrain.
They must also feature the technology to ensure optimal delivery and minimal waste, in terms of both materials and time.
The paving division of Caterpillar focuses on road construction, which boasts a wide range of equipment, from reclaimers and compactors, to pavers and cold planers.
Soil compaction
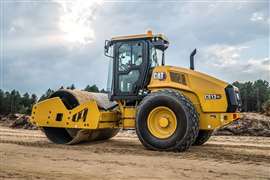
As soil compaction must be completed before other phases of road construction can proceed, it’s vital that compaction equipment is both efficient and reliable.
Caterpillar boasts 14 models of vibratory soil compactors, with operating weights from below 10,500kg up to almost 19,000kg, including both smooth and padfoot configurations. The product line includes both standard and performance models, to match application and usage.
Taking the CS13 GC as an example, the machine’s performance revolves around an exclusive eccentric weight design, that improves reliability and reduces noise. The machine’s auto-vibe function also aids consistent compaction.
As an option, the 12,655kg smooth drum machine can make use of a padfoot shell kit, which allows for compaction of semi-cohesive or cohesive soil applications.
David Fabro, paving business development manager at Caterpillar, says of the Cat GC vibratory soil compactor line, “Operator comfort and ease of use were primary design drivers with these machines.
“It has an ISO-mounted cab and rubber floormats that helps reduce noise and vibration and operators like the intuitive controls layout and the levels of comfort, especially with the option of the air suspension seat.”
As with most Cat machines, fleet management is optimised via the VisionLink system, delivering data such as maintenance requirements, machine hours, location, fuel usage and idle time.
Furthermore, the system’s application programming interface (API) enables the use of VisionLink across mixed fleets.
Road reclamation
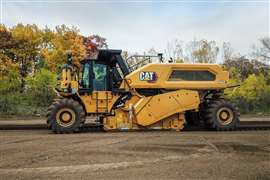
On rehabilitation projects, where deteriorated roadways must be stabilised, road reclaimers will pulverise the original asphalt layer and mixing it with the base material.
The reclaimers add asphalt emulsions or other binding agents, either during pulverisation or during a separate mix pass.
The process provides a homogenous material on which to lay a surface course, and is a crucial stage, ahead of laying asphalt.
If full-depth reclamation and soil stabilisation is required, machines need to be powerful robust and efficient.
The Cat road reclaimers line comprises the smaller RM400 and RM500 models, as well as the large RM600 and RM800 models, both of which are powered by powerful Cat Stage V engines.
Visibility of operators is a key feature of the machine, along with enhanced manoeuvrability.
Rolf af Klinteberg, a product application specialist with Caterpillar, says of the RM600 and RM800, “Sight lines are optimised with a full left-to-right sliding cab, meaning visibility to the cutting path is excellent, with floor to ceiling glass and an angled pane on the right-hand side that gives a clear view to the leading edge of the cutting chamber”.
“What’s more,” says Klinteberg, “the RM600 and RM800 have front and rear mounted cameras with on-screen configurable guidance lines, so operators have even more fore and aft visibility.”
It’s crucial that, as the road reclaimer progresses, it continues to deliver the optimum mix quality, by keeping the rotor at the correct depth, while the speed of the machine remains constant.
The advanced electronic controls of the road reclaimers allow the operator to instantly modify material gradation on the move, by simply adjusting the front and rear mixing chamber doors, monitoring adjustments via an easy-to-read indicator on the touch screen display.
Paving
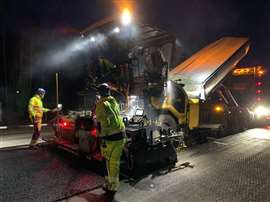
While tracked pavers offer benefits for larger and more complex road projects, wheeled pavers boast excellent mobility and are generally a good choice on applications requiring a lot of paver movement and relocation.
Today, urban street development is both a growth industry and an increasing challenge for construction businesses. These businesses must balance the need for high-quality paving with the necessity of completing projects quickly to maintain profitability.
Caterpillar recently launched two paver models onto the European market, primarily with urban road construction in mind. Both have three undercarriage type offerings (wheel, steel track and Mobil-trac system). They come with two redesigned screeds, the SE47 VT and the SE50 VT.
The AP400 and AP500 wheeled pavers sit in the compact-to-mid-sized category, and both provide consistent material flow across the screed, through the use of an enhanced feeder system with 355mm diameter augers. This system, along with enhanced tamper-bar and deflector plate profiles provide smooth flow to the screed plates at both narrow and wide paving widths.
The paving widths of the SE47 VT is from 2.4m to 4.7m with a maximum of 6m, while the SE50 VT ranges from 2.55m to 5m with a maximum of 6.77 for the AP500 and can extend the maximum width to 7.64m for the AP555.
David Fabro says, “The dual carriage design of these screeds enhances rigidity while the symmetrical extenders provide consistency from side to side to improve mat profile.”
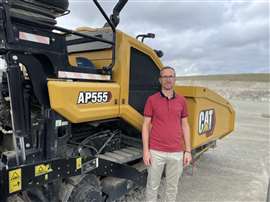
“They’re easy to set up and very versatile, which is perfect for highways, airports and mid-sized applications.”
The compact dimensions and relatively light weight of these pavers makes them easily transportable, as well as being highly manoeuvrable on site. The AP400’s operating weight is 14,581kg, while the AP500 weighs in at 15,430kg.
Both wheeled paver models can travel up to 16km/h and can be fitted with front-wheel assist, with an extra option on the AP500 of all-wheel drive, which Fabro says can be “beneficial when pushing heavy loads”. Both tracked paver models are recommended on softer base materials and with a 6km/h transport speed for the steel track version and up to 11 km/h for the Mobil-trac System.
Asphalt compaction
Whether using hot or warm mix asphalt, there can be no delay in compaction once the asphalt is laid down. To ensure the removal of air voids from the structure, the density of the road surface must be increased – usually by an average of 10-15% – to ensure the maximum lifespan of the road.
“This is a critical element of the road construction process,” stresses Rolf af Klinteberg, “as you need to strike the right balance between compaction, smoothness and speed. If the roller’s drum is too narrow, it will take too many passes to completely cover the paved surface; if it’s too wide, it could lead to non-uniform density, with compaction runs overlapping.”
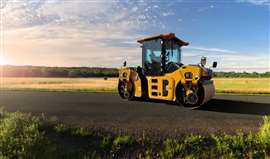
To this end, Caterpillar manufactures a wide range of tandem vibratory rollers, from as little as 1.6 tonnes to over 16 tonnes.
At the larger end of the series, the CB7, 8 and 10 can have ROPS or fully-enclosed cabs and are designed to tackle intermediate applications, including urban streets and highways.
These fuel-efficient machines come with Eco-mode and automatic idle shutdown and are simple to operate, with straightforward dial indicators and an intuitive touchscreen display.
At the same time, there is no shortage of onboard technology, including compaction control and flexible vibratory systems.
The CB7 has a standard compaction width of 1500mm, while the larger CB8 and CB10 machines can compact at a width of 1700mm.
Options on these larger compaction machines include top down 360-degree views, using cameras mounted on each corner of the cab, as well as a fully rotating seat, so operators are always facing the direction of travel.
Caterpillar also offers strategically placed LED lighting – along the sides of the machine, as well as on drum surfaces and edges, giving operators the confidence to progress jobs efficiently at all times.
Cold planing
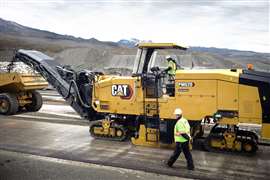
One of the first machines on site can also be the final piece in the road construction puzzle – cold planing.
All roads have a finite lifespan, at the end of which, they may have to be rehabilitated, generally beginning with a milling or planing process.
Depending on the amount of damage the asphalt has suffered, a cold planer is often used, either to remove part of the existing pavement to help restore a smooth surface, or to remove the full depth of asphalt, along with the sub-base materials.
Getting the right machine for the job is key, according to David Fabro, who says, “Cold planing machines must be heavy enough to provide the traction and stability required to remove the required depth of pavement surface.
“Our large cold planers use integrated technology to achieve milling precision, along with System K rotors and a Cat track design with advanced steering and traction control.”
At the heavier end of Cat’s cold planers are the PM600 and PM800-Series models. These machines can mill from widths of 2010mm to 2505mm.
The PM620 has an operating weight of over 33 tonnes, and a gross power rating from its Cat C18 engine of 474kW/636 HP.
These are powerful and heavy machines, but are able to cut through road surfaces with extreme precision. Equipped with automated grade control systems, the cold planers can mill accurately to specified elevations, grades or cross-slopes.
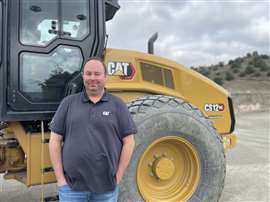
The largest cold planer in the series is the PM825, which weighs in at 37.5 tonnes and features a 601kW/806HP C18 twin turbo engine, providing 21% more gross power than the PM620, based on standard engine performance testing.
This high-production, half-lane machine is designed with the capacity to complete a controlled full-depth removal of asphalt and concrete pavements in a single pass.
Cold planers are heavy duty machines, designed to operate under the most challenging conditions. It is imperative that their critical components are both robust and accessible for servicing and maintenance.
A prominent feature of a Cat cold planer is its System K rotor, designed to minimise wear and maximise material flow, with a cutting pattern that moves material from the outside to the centre, for extraction.
The toolholder and base block elements of the rotor are made from abrasion-resistant high-strength alloys, while the large heat-treated surface areas on the toolholder protect the base block, increasing its useable life.
The road ahead
Caterpillar’s position as the world’s largest manufacturer of construction equipment has to some extent overshadowed its strong showing in the roadbuilding industry.
In fact, Caterpillar sold its first piece of paving equipment some 40 years ago and has been developing its road construction division ever since.
Furthermore, the latest machines bring with them Cat’s renowned durability, efficiency and advanced technology, as well as an unmatched level of support.
With this in mind, as the development of Europe’s transport network continues, we can expect to see Caterpillar’s road division continuing to develop alongside it.
This article was produced by the KHL Content Studio, in partnership with product experts from Caterpillar.
STAY CONNECTED
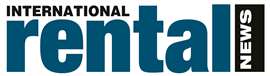


Receive the information you need when you need it through our world-leading magazines, newsletters and daily briefings.
CONNECT WITH THE TEAM
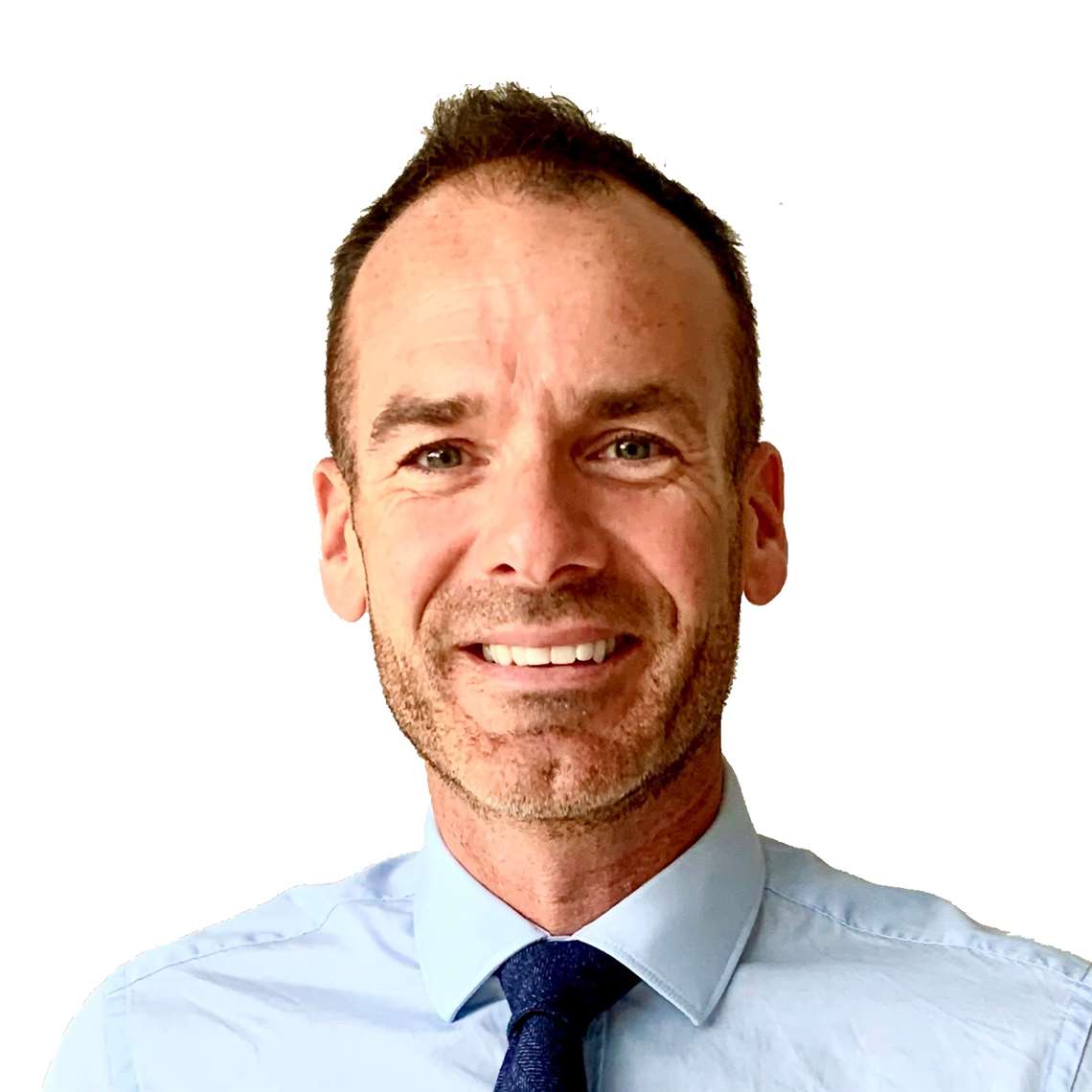
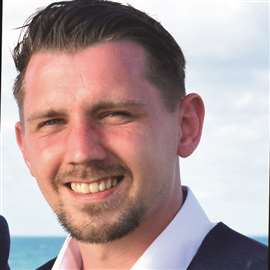