Fast solutions
21 October 2024
Sloan Lubrication Systems introduces its Quick Ship program

Sloan Lubrication Systems, founded in 1922, manufactures, installs and services force-feed lubrication systems, serving gas compression customers worldwide.
Sloan said its new Quick Ship program guarantees customers with urgent needs the rapid delivery of up to 8,744 SKUs with standard 2-day shipping, and same day or next day expediting available for a fee. This covers 104 of Sloan’s most critical products like filters, gauges, indicators, and monitoring devices, and includes several custom-built components assemblies – divider blocks, check valves, and commonly used lubricator boxes.
Quick Ship comes at a time when many lubrication system parts manufacturers are pulling back from the gas compressor market or extending lead times on components critical to operations, according to Eric Sloan, director of Marketing and Business Development at Sloan.
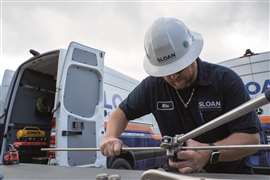
“Quick Ship is just one way we are doubling down on the gas compression market which has been the core of our business for decades,” Sloan said. “It is also a major part of an internal imitative we launched this year that we call ‘frictionless business partners,’ where we are making changes necessary to provide our customers with the most frictionless experience possible. With Quick Ship we are making big investments in inventory and processes to make sure we can support our shipping goals to keep our customers up and running when they need it most.”
Avoiding downtime
When a compressor goes down, getting it back up and running is often an expensive proposition. Beyond the expense of unplanned maintenance, there are many cases that a shutdown means an entire process stops. The cost of process shutdown can be significantly more than the cost of repair when lost profits are considered. When a compressor goes down due to a failed lubrication system, more often than not the required spare parts are not on hand. In circumstances like this, standard lead times measured in weeks are a problem.
“Our first line of defense is always education,” Sloan said. “We try to make sure that our customers know what scenarios they are likely to run into over the life of their systems, and we try to make sure they know how to quickly solve them. Part of this is having the needed spare components and maintenance items on the shelf. Our systems often run reliably for a decade or more with very little maintenance through, and after a few years that initial training does not do much good. Spare parts are used and not re-ordered, and eventually the knowledge to repair fades and the needed parts are not on hand when something goes wrong. This is where Quick Ship fills a gap in our program.”
Added services
Sloan also recently introduced several other products and services. Sloan Service Plans offer regular preventative maintenance services to keep lubrication systems for critical machinery in good operating condition while extending their warranty. Sloan’s service plans are designed to provide a offering to fill a gap created by the trend towards reduced facility staffing and loss of knowledge as experienced equipment operators retire. Compressor lubrication systems are critical to reliable operation, and too often they do not receive the proper maintenance they need to run reliably, leading to down time and increasing the potential for damage.
Another recent offering from Sloan is its TriCip lubrication system, enabling up to a 90% reduction in compressor cylinder lubricant by combining a proprietary lubricating fluid with advanced monitoring and controls. The benefits of this degree of lubricant reduction are significant. Lubricating fluid is often one of the biggest line items on annual operating budgets, and reducing the cylinder lube by 90% has the direct benefit of reducing that expense. Direct cost is only a fraction of the overall benefit though, because compressor cylinder lubricant is once through – meaning it is injected into the compressor cylinders and then carries over into the process. Some of it is removed by filters and knockouts, but much of it ends up in the pipeline as a gas stream contaminant, where it can have significant negative impacts like reduced throughput, metering station contamination, and damage to end user equipment like gas turbines.
“With nearing 200 units in the field and hundreds of thousands of successful run time, this proven solution is changing the equation of compressor lubrication,” said CJ Sloan, CTO at Sloan Lubrication and the inventor of TriCip. “We are reducing the cost of lubricant on the front end, and drastically decreasing the expense of excessive lubricant on the back end. And it reduces the carbon footprint of operations, so it really is a win, win, win for compressor operators.”
C.J. Sloan said compressor operations are changing and the challenges that operators face are changing too. In such a dynamic industry it is common for a small subsystem like force feed compressor lubrication to be ignored as long as it is running. It is hard to keep up with preventative maintenance on such a small but complex system. When something goes wrong it is crucial to get the needed parts quickly, and this is the scenario that a program like Quick Ship is designed to fix, CJ Sloan said.
STAY CONNECTED
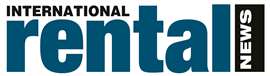


Receive the information you need when you need it through our world-leading magazines, newsletters and daily briefings.
CONNECT WITH THE TEAM
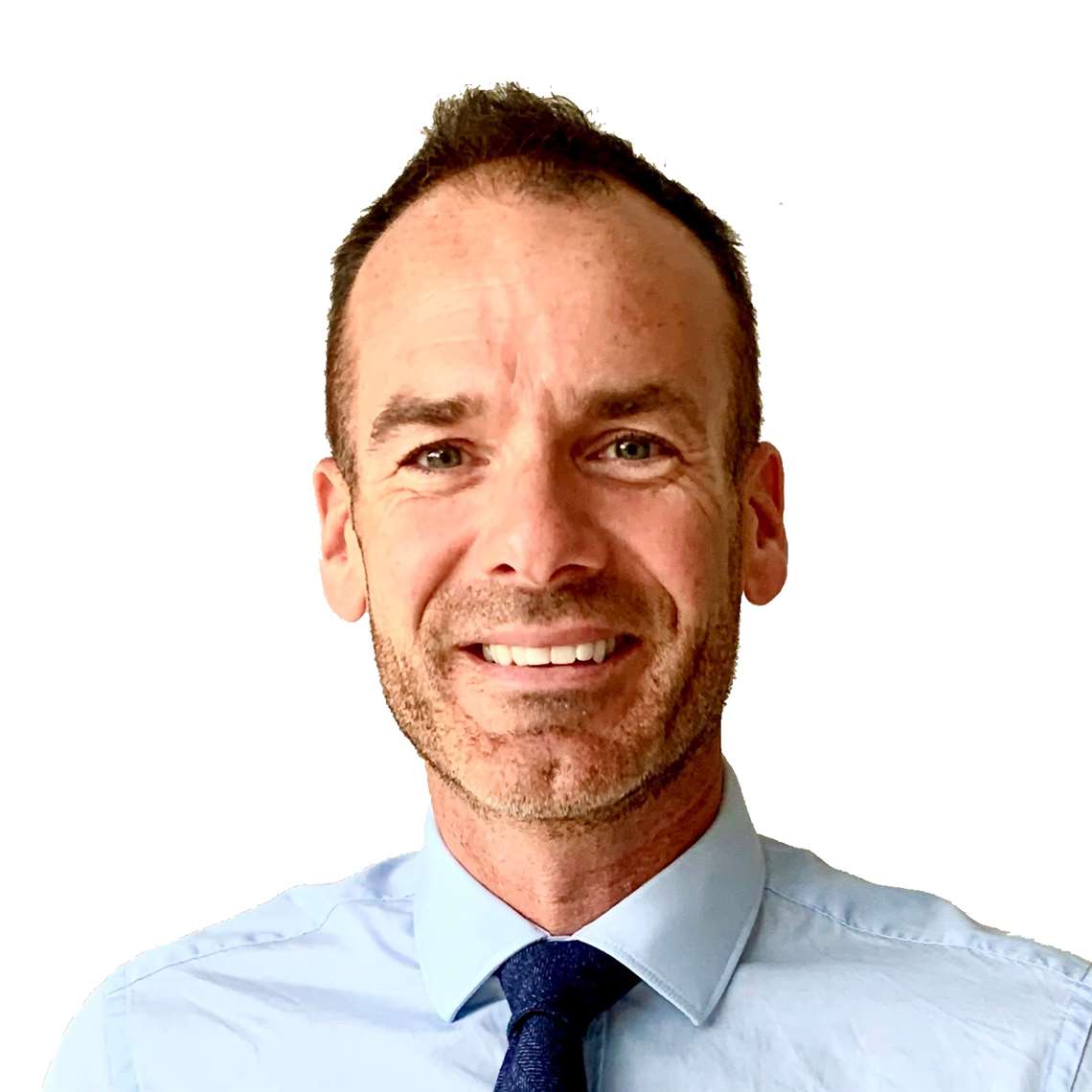
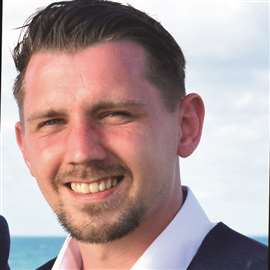