How are crawler cranes aiding wind energy and infrastructure projects?
18 November 2024
With increased demand from infrastructure projects and a global shift towards renewable energy, the global crawler crane market continues to grow. This crane type’s high load capacities and long booms are proving useful for wind farm construction. Niamh Marriott reports.
Manufacturers that include HSC, Kobelco, Liebherr, Manitowoc, Sany, Tadano, XCMG and Zoomlion are leading the industry, offering cranes with high lifting capacities and versatile boom configurations. Their cranes are not only crucial for traditional construction and industrial applications but are also widely used in the wind energy sector as the world moves towards sustainable renewable energy.
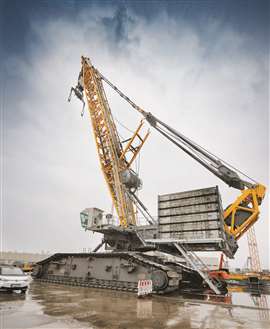
Crawler cranes, defined by having a tracked chassis, provide stability and mobility under load (pick and carry) on a range of terrains. This crane type is favoured for large scale lifting projects due to strong lifting capacity and long reach. The features also lend this crane type to lifting work taking place in unusual or remotely situated construction sites.
Given the growing focus on infrastructure development and renewable energy, the crawler crane market is expected to continue expanding, with major advances in crane technology continuing to help meet a diverse range of project requirements.
Offshore operations
As a leading manufacturer of crawler cranes, Liebherr is known for advanced engineering and high-quality machines. Its crawler cranes are widely used in construction, wind energy, and infrastructure projects. The company’s crawler cranes offer various boom configurations and load capacities to suit different needs.
“The market for crawler cranes is currently very good. We continue to see growth for classic industrial applications, but demand is growing in the wind power sector in particular, driven by the climate targets of many countries,” says a spokesperson for Liebherr.
“On the one hand, there are the large number of onshore wind turbines, but the growth in offshore wind turbines is also generating the need for large crawler cranes, eg. for port handling. This will be an important area for [our] LR 12500-1.0.”
In 2023, heavy lift giant Sarens took delivery of the first unit of Liebherr’s new 2,500 tonne capacity crawler crane, the LR 12500-1.0, with more orders following.
Liebherr’s crawler cranes, such as the LR 13000, are among the largest in the world. The LR 13000 has a maximum boom length of 144 metres and a lifting capacity of 3,000 tonnes, making it suitable for large scale industrial projects, including heavy lifting in shipyards and power plants.
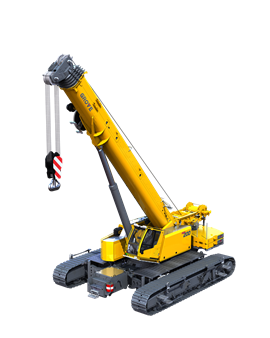
For wind farm applications, the Liebherr LR 11000 is a popular choice, offering a boom length of up to 126 metres and a load capacity of 1,000 tonnes. The LR 11000’s ability to lift heavy turbine components at great heights makes it ideal for erecting wind turbines.
Heavy duty
American manufacturer Manitowoc will begin shipping its largest Grove hydraulic crawler (GHC) telecrawler crane – the new GHC200 – to customers later in 2024. Featuring a 56.4 metre main boom and 181 tonne maximum load capacity, the new model is said to deliver heavy-duty lifting power in applications that require high capacity at various radii in tough job site conditions, such as swampy and mountainous terrain.
The GHC200 was unveiled to dealers and customers at Manitowoc’s Crane Days event in May at the company’s factory in Shady Grove, Pennsylvania, USA.
“We have seen substantial growth within our telecrawler offerings, and our new model launches continue to contribute to this success,” says JJ Grace, product manager for GHC cranes at Manitowoc. “One market trend we have seen is the growth and demand for larger telecrawlers. To meet this demand, the GHC200 is our latest and largest telecrawler offering.”
Typical applications for Grove telescopic crawlers include utility work or lifting work on infrastructure projects, Grace says.
When it comes to unique applications, Manitowoc has seen its crawlers assist with barge work (barge charts are standard), pile driving and foundation jobs.
“One of the latest is an assist crane on a wind farm to build some of our Manitowoc MLC product,” says Grace. “Then, they stayed on the job to do pick and carry work or even used a tailing crane.”
Large models
The Manitowoc 31000 is the company’s largest crawler cranes, with a maximum boom length of 125 metres and a load capacity of 2,300 tonnes. It is used in the construction of large infrastructure projects, such as power plants and bridges. For wind energy, the Manitowoc MLC650 is frequently used due to its maximum boom length of 104 metres and a lifting capacity of 650 tonnes, making it capable of installing the tall towers and heavy nacelles associated with modern wind turbines.
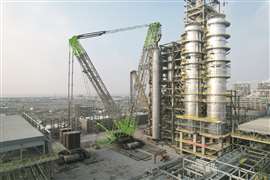
Chinese manufacturer Zoomlion has grown to become a major player in the global crawler crane market, with significant sales in Asia, Europe, the Middle East, Africa, and Latin America.
Known for its cost-effective solutions, its cranes are used in construction projects throughout Asia and beyond.
The Zoomlion ZCC89000 is a heavy-duty crawler crane and one of the largest models in Zoomlion’s lineup, designed for large lifting tasks in industries such as construction, energy, petrochemicals, and heavy infrastructure. It is particularly notable for its high lifting capacity and advanced design, making it suitable for demanding projects like power plant construction, petrochemical installations, and large wind turbine erection.
Earlier this year, the manufacturer claimed two more world lifting records for its 3,600 tonne capacity lattice boom crawler crane on a project in China.
Between 3 and 8 January the ZCC89000 crawler crane with double lattice booms lifted three giant chemical processing vessels, the heaviest of which weighed more than 3,000 tonnes. Zoomlion claimed two world records, one for the heaviest single lift and the other for the fastest lifting speed.
In wind farm applications, the Zoomlion ZCC9800W crawler crane is frequently used due to its 168 metre boom length and 800 tonne lifting capacity, making it ideal for erecting tall wind turbine towers and handling large rotor blades.
Super lifts
Sany is another major Chinese manufacturer offering a wide range of crawler cranes, including models designed for heavy lifting in the construction and energy sectors. The company has made significant strides in the development of cranes suitable for renewable energy project applications.
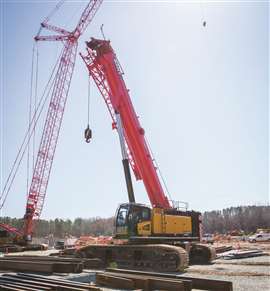
The Sany SCC86000TM is one of the largest crawler cranes offered by the company. This giant boasts a maximum boom length of 126 metres and a lifting capacity of 3,600 tonnes, making it suitable for super-heavy lifting in industrial and infrastructure projects.
In the wind energy sector, the Sany SCC4000A crawler crane, with a boom length of 120 metres and a capacity of 400 tonnes, is commonly used. Its design allows for the efficient installation of wind turbine components, including the nacelle, rotor blades, and tower sections.
The company’s focus on creating specialized cranes for the wind energy sector has made its models particularly popular for wind farm installations, both onshore and offshore.
Wind work
Crawler cranes are crucial in the construction of wind farms due to their high lifting capacities and the ability to handle large, heavy components such as turbine towers, nacelles, and rotor blades. The installation of modern wind turbines, which regularly now exceed 100 metres in height and require lifting heavy parts to great elevations, necessitates the use of cranes with extended boom lengths and significant lifting capacities.
TRACK STAR
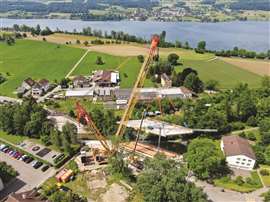
Switzerland-based Toggenburger used a Tadano CC 38.650-1 lattice boom crawler crane with a 66 metre boom to lift and place the 230 tonne Aabachbrücke bridge in Niederuster, Switzerland.
The bridge’s parallelogram shape and sensitivity required precise load distribution, achieved through strand jacks that controlled individual lines to prevent structural damage.
The crane was assembled in two and a half days. Erection was assisted by an AC 140 all terrain crane and 20 trucks transporting components to the site. The lift involved manoeuvring over challenging terrain and setting the bridge down with precision.
“Space at the work site was extremely tight [but] an experienced team with the right crane can execute complex lifts safely and accurately within schedule,” adds Manuel Widmer, Toggenburger’s large scale project manager.
STAY CONNECTED
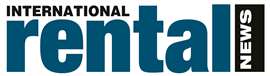


Receive the information you need when you need it through our world-leading magazines, newsletters and daily briefings.
CONNECT WITH THE TEAM
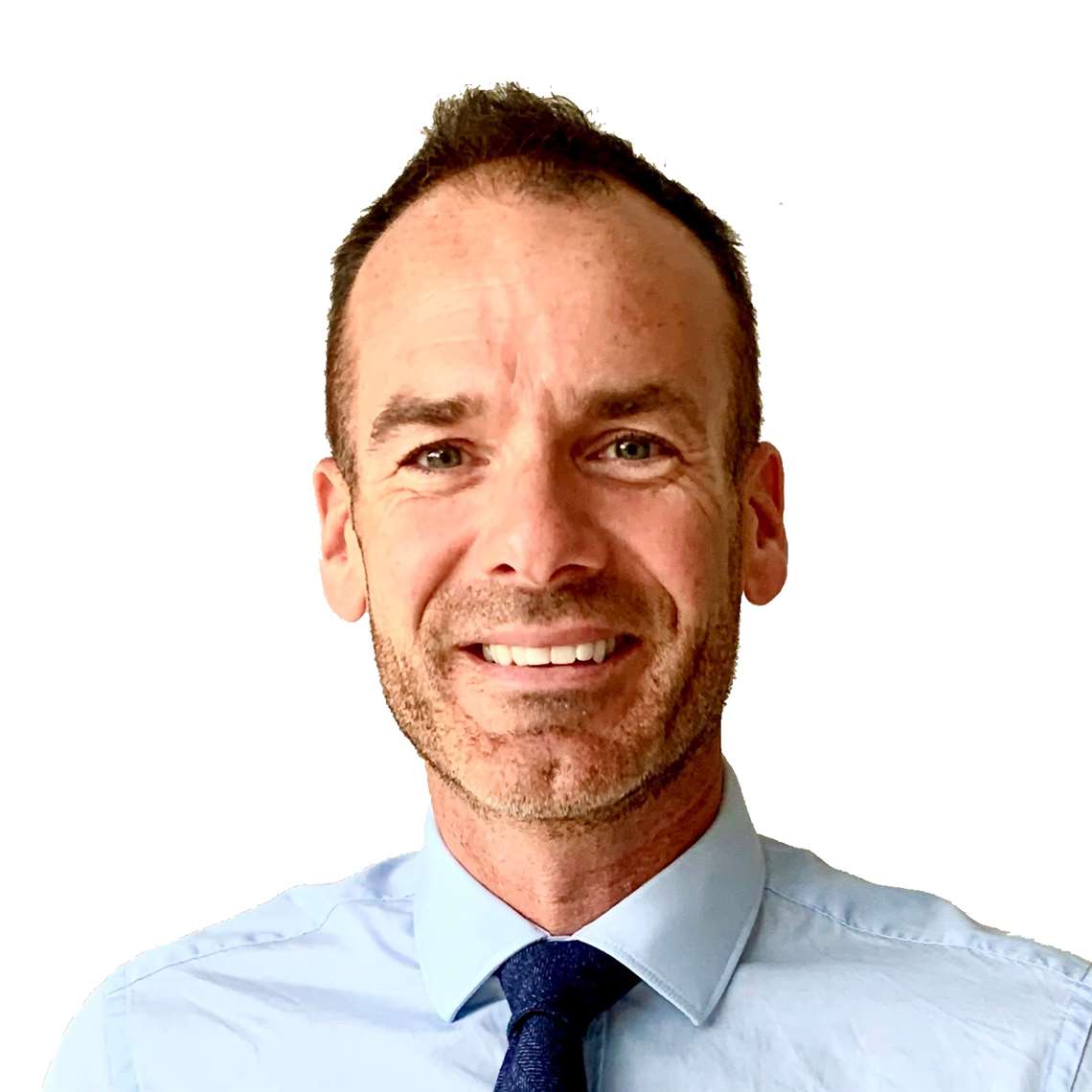
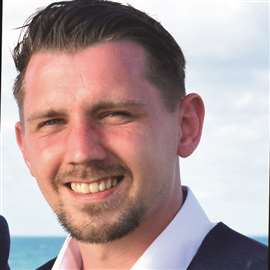