Hydrogen fuel cells in material handling equipment
25 June 2024
One of the most popular fuels for powering lift trucks is propane. During a recent Engine Technology Forum webinar about propane autogas, Gavin Hale of the Propane Education & Research Center (PERC) said propane drives about 600,000 forklifts in the United States.
Electric power sources, however, are making headway in forklifts. Jacob Whitson of non-profit CALSTART cited 2021 market research that indicated nearly 250,000 battery electric forklifts will be sold in the U.S. by the end of 2029.
Also gaining momentum are hydrogen fuel cell electric forklifts. A spokesperson for the U.S. Dept. of Energy (DOE) said via email that there are currently more than 60,000 such machines deployed across the U.S. This is up from 20,000 in November 2018, per DOE’s Fact of the Month published at that time.
Material Handling Variety
And it’s not just forklifts. Hydrogen fuel cells are making their way into a variety of material handling solutions.
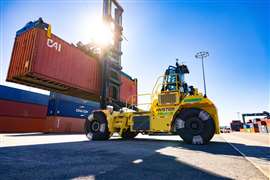
“While the use of advanced electric power sources, like HFCs (hydrogen fuel cells) or lithium-ion batteries, is generally more mature for lines of smaller, lighter-capacity equipment like forklifts, it is worth noting that HFC adoption is growing in other types of material handling equipment, such as container handling equipment commonly used to move shipping containers at ports,” said Lucien Robroek, president of Global Technology Solutions for Hyster Company, via email.
“In fact, applications that use container handling equipment are among those with the greatest potential for HFCs,” he said. This is due largely to the machine’s high load capacity and the need to run practically 24/7/365.
FCEV vs. BEV
Robroek said that there are a variety of factors that contribute to choosing a fuel cell electric vehicle (FCEV) over a battery electric vehicle (BEV) in material handling applications. These include energy sources, fleet size, running times, available space, sustainability goals and the regulatory environment.
“In general, though, the time required for charging and the time that equipment can run on a charge have historically been key challenges for battery electric power in high-capacity applications with heavy duty cycles,” Robroek said.
For example, he said that for IC-powered operations having duty cycles that last the equivalent of several eight-hour shifts, switching to a battery electric solution may mean investing in additional forklifts to address machines that must be taken temporarily out of service for battery recharging.
“Fuel cells, on the other hand, do not need to be recharged,” Robroek said. “Instead, operators refuel a tank of hydrogen, similar to the time spent refueling an ICE.”
He added that innovations in battery electric machines have made it possible for forklifts to operate for a full eight hours before needing to recharge.
“For operations that don’t require trucks to run continuously across multiple shifts or ones that can accommodate a larger truck fleet, battery electric may be a strong fit,” Robroek said.
Grid Stability
However, another challenge for battery electric equipment is the power grid, which Robroek said requires an assessment of local grid stability.
“The average household uses 29.5 kWH per day,” he said. “In contrast, charging a fleet of 100 container handlers with a 260 kWH battery pack once each day requires over 20,000 kWh — enough demand that could overload grid capacity.”
Smaller fleets coupled with the ability to charge overnight or with a staggered charging schedule may not be as much of an issue, particularly when the grid is robust, Robroek said.
Fueling Infrastructure
According to Robroek, fueling for FCEVs requires on-site hydrogen fueling stations and, depending upon a company’s hydrogen sourcing strategy, storage.
“Hydrogen fuel can be delivered to storage and fueling stations or generated on-site,” he said. “The amount of hydrogen an operation uses is a critical factor in determining what method of hydrogen sourcing makes sense.”
When fueling a single vehicle, for instance, an organization may choose to simply take delivery of hydrogen tank bundles for smaller volumes or a tube trailer for larger volumes, Robroek said. However, on-site hydrogen generation makes sense once consumption passes 800 kg per day or if delivery distance becomes an issue.
“As for the handling and storage of hydrogen fuel, operations must store it in a secure location that is clean and dry and refer to the operator or service manual for proper storage temperature and environmental conditions,” Robroek said. “Operations must also eliminate all ignition sources within 25 ft. of the storage area and cannot perform hot work — work that requires an open flame — within 25 ft. of the storage area.”
STAY CONNECTED
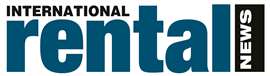


Receive the information you need when you need it through our world-leading magazines, newsletters and daily briefings.
CONNECT WITH THE TEAM
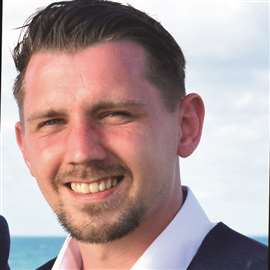

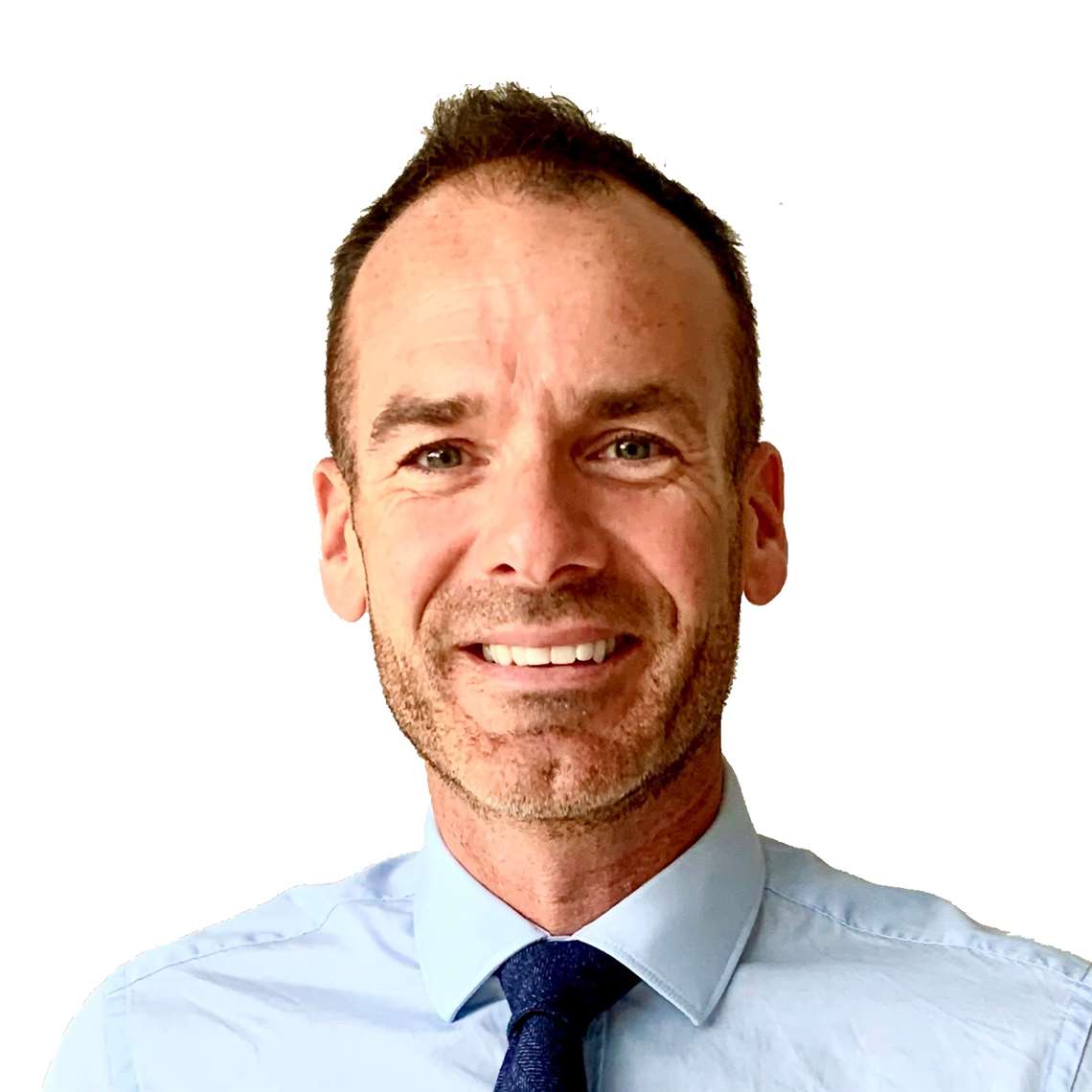