Soaring demand funds telescopic-boom innovation
10 April 2023
Record-breaking 2022 business returned North American demand for telescopic-boom aerial work platforms to pre-pandemic levels. Now boom manufacturers and rental giants are projecting 2023 outlooks for continued growth despite tangible economic uncertainties.

Of course, product innovation in rough-terrain telescopic boom product lines flourishes when industry cash flows reach the kind of peaks we’re seeing today. Expect strength in infrastructure, manufacturing and commercial construction to support continued development of these machines’ capacities, reach, safety and sustainability.
Soaring demand for access equipment
Already strong demand for rough-terrain mobile elevating work platforms (MEWPs) soared in 2022, with new investments in microchip manufacturing taking off since August passage of the CHIPS Act adding megaprojects to the brisk pace of developing logistics and data centers. Demand at rental companies – the biggest buyers of telescopic-booms – reached new peaks.
“Our fourth-quarter results capped an outstanding year, during which we set records for revenue, profitability, margins and returns,” says Matthew Flannery, chief executive officer of United Rentals. Capital spending on rental equipment at the world’s largest equipment rental company climbed to $3.44 billion. United’s 2023 outlook projects a 20 percent increase in revenue into the $13.7 to $14.2 billion range.
Herc Rentals’ equipment-rental revenue leaped 34 percent to a record $2.55 billion with a 5.8 percent increase in overall pricing and 32 percent volume jump driving nearly all of the company’s 32 percent increase in total revenues to $2.74 billion. Fleet growth led to a 27 percent increase in rental-equipment depreciation to $536 million. Herc’s 2023 guidance anticipates $1.0 billion to $1.2 billion for net rental equipment capital expenditures.
It’s hardly a surprise, then, that Oshkosh Corp. net sales of its JLG aerial work platforms surged more than 21 percent in 2022 to $1.95 billion. Aerial work platforms made up about 51 percent of the JLG brand’s net sales.
Net sales in what the Terex corporation calls its aerial-work-platform segment (referring to the full Genie brand) were up 14 percent to $2.5 billion in 2022. The Terex 2023 outlook for the segment expects a 6.7 percent increase in net sales into the $2.6 to 2.7 billion range.
Innovation fueled by market needs
The rising cash tide is lifting product innovation. Telescopic-booms continue to get increased platform capacities – a bonus related to implementing 2020’s ANSI A92.20 safety standard. The integrated load and tilt sensors required to comply offer opportunities to improve platform capacities.

Load sensors assesses the weight in the work platform and will only allow the machine to operate at full performance if it is within the MEWP’s rated capacity.
Skyjack recently improved its SJ45 T+ and SJ66 T+ telescopic boom lifts with both models’ new restricted capacities at 1,000-pound maximum, and 750 and 660 pounds, respectively, unrestricted.
Power-train updates to the SJ45 T+ power train identified an opportunity to power it with a 25-horsepower engine.
“In conjunction with its ECOstart anti-idling option, this change will reduce fuel usage up to 40 percent,” says Corey Connolly, product manager at Skyjack.
Six models in Genie’s new Xtra Capacity (XC) range – in 66-foot, 71-foot, 86-foot, 91-foot, 131-foot and 141-foot working heights – will work with 1,000-pound platform capacities in a restricted lifting range, and 660 pounds unrestricted.
LGMG launched four new models of high-capacity H-Series telescopic boom lifts in 2022. The Chinese manufacturer sells its 72-foot T72J, with a maximum, restricted platform capacity of 992 pounds and unrestricted capacity of 661 pounds, in North America. The H-Series booms are Deutz-diesel-powered, four-wheel-drive machines with oscillating axles capable of 45 percent gradeability. The booms will operate at a maximum chassis tilt of 4.5 degrees.
JLG added smart hydraulic cylinders managed by the inclinometer to independent axles on the machine’s four corners, creating a unique Self-Levelling boom. Each wheel automatically follows the contour of the terrain, keeping the chassis level on changing slopes of 10 degrees or less. The only model in the series at press time is the 670SJ.
In addition to reducing or eliminating time required to level the work area, a self-leveling lift also can reduce the time to position a lift at various work locations. A consistently level chassis maximizes the lift’s reach capabilities and reduces the need to use a larger-than-necessary lift on some jobsites. Smoother ride reduces operator fatigue and makes safer passage for people and equipment in the platform.

Three work modes take advantage of the capability:
- Self-leveling mode enables the machine to work with full functionality at height on slopes up to 10 degrees.
- Travel mode can be used when the boom is stowed to move faster across the job site.
- Shipping mode allows the entire machine to be lowered after it is in position on a truck, reducing its travel height.
The electrification elephant
As product development stabilizes around compliance with new safety standards, the dominant outside influence on telescopic-boom innovations has been shifting toward electric power trains.
Analysis of global construction media company KHL’s directory of new equipment introductions shows 40 to 50 percent of new construction-machine models launched in the first half of 2022 were electric. About a third of them were aerial work platforms.
In addition to the big yellow earthmovers’ investments, Oshkosh bought $25 million worth of Microvast and Terex made a Series A investment in Acculon. In December, Manitou Group announced its acquisition of an 82 percent stake in easyLi.
“By internalizing this (EasyLi’s) expertise, we are going to be able to study machine-battery interactions in depth and thus continue to reduce total cost of ownership for our users,” says Michel Denis, Manitou president and CEO. “This operation is in keeping with our research and development plan to accelerate our energy transition.”
The 2015 Paris Agreement on greenhouse gasses stimulated government regulation, and demand for electrification of internal-combustion equipment. Cities and counties here and abroad with poor air quality had enacted local emissions standards even before 2015.
Where emissions levels must be accounted for and/or monitored throughout the duration of some construction projects, demand from users for hybrid and electric machines has risen. The cost to implement low-emissions technology is coming down, and advances in electrified equipment continue to improve performance at greater efficiency.
In the same way equipment manufacturers have found that electric power trains cut total cost of ownership, other industry stakeholders are finding side benefits to electrification that stoke motivation for manufacturers and users to buy electric booms.
Investing in environmental, social and governance (ESG) stocks has gone mainstream, so publicly traded lift makers and users have elevated sustainable booms to a business imperative. The Paris Agreement resulted in a system of corporate carbon-emission reporting that helps investors choose ESG stocks. Investment funds scrutinize carbon reports not just to gain sustainability cred, but also as they discover that companies with strong ESG ratings often deliver strong stock performance.
One of three categories, or “Scopes” in the parlance, of carbon emissions companies must report counts indirect carbon. For manufacturers, Scope 3 includes all of the emissions created by the products they produce throughout those products’ useful lives.

Scope 3 emissions are particularly important to access equipment makers because carbon emissions from use of their products, typically measured by their energy consumption, can make up as much as 85 percent of the company’s total carbon emissions. Designing more efficient machines is the biggest lever they can use to improve carbon reports.
The electric-boom pitch
Electric booms are more than just a stock-price builder. The precise controllability of an electric power train, compared to internal combustion driving hydraulic systems, makes an electric machine do the job not only without producing local emissions but also requiring far less total energy. The difference can be dramatic. A rare example of fully electric access equipment, JLG’s DaVinci all-electric scissor lift, uses 70 percent less energy than a conventional electric scissor.
This is where boom development is headed because it reduces operating costs and carbon emissions. Access equipment designers are just waiting for electric-component makers to develop actuators in the sizes needed to power booms.
Just replacing the diesel engine with the instantaneous torque of electric motors significantly reduces energy consumption. With diesel sometimes as costly as labor, the shift is well under way.
Genie’s latest telescopic boom introductions are the S-60 DC electric and hybrid S-60 FE booms. Said to be the industry’s first lightweight, four-wheel drive electrified telescopic boom lifts in the 60-foot height class, both models reach out more than 40 feet with maximum platform loads of 660 pounds on a 6-foot jib.
Genie’s decision to produce a hybrid 60-footer in addition to an electric one acknowledges one of the limitations of electric access equipment, particularly rough-terrain machines. The hybrid option underscores the challenge a significant portion of users face keeping electric machines charged on construction sites before the electrical infrastructure is in place.
The hybrid can work a long stretch on a single load of energy. Both the S-60 DC and the S-60 FE deliver a full day of 100 percent electric, four-wheel drive performance on a single battery charge. And Genie says the hybrid S-60 FE can work more than a week on a single tank of fuel.
The FE boom’s intelligent control system keeps batteries charged and the machine ready to work by using both regenerative braking and automatic engine start and stop. By recharging batteries while the boom works, the S-60 FE can help eliminate downtime caused by plug-in charging.
Maintenance-free, absorbent glass-mat (AGM) batteries are standard on the FE, and flooded lead-acid batteries are standard equipment on the DC. Choices of 25-horsepower Kubota or Kohler diesel engines for the FE eliminate need for after-treatment or low-sulfur fuel.
The wheels of both machines are driven by four sealed AC electric motors that provide torque similar to hydraulic drive motors while using 30 to 40 percent less energy. Four-wheel drive plus electronic traction management and oscillating axles enable 45 percent gradeability in rough terrain.

Electric drives propel the two booms with 70 percent fewer hydraulic components in the drive chassis than comparable booms using hydraulic drive motors, an advantage Genie claims will reduce maintenance costs by 10 percent.
At the 2023 American Rental Association show, Genie President Simon Meester said, “For more than 55 years, the Genie team has been focused on delivering quality solutions that meet jobsite and equipment owners’ needs. That is reflected in our product line-up, which is already more than 70 percent electrified, and growing.
“I’m excited to have an opportunity to show customers how our newest models can offer a lower total cost of ownership, a strong ROI, and, in many cases, lower jobsite emissions too.”
At about 17,700 pounds, the new blue booms are a third lighter than comparable models, which gives them broader access to jobs requiring low floor loading and makes them easier to transport.
Manitou marketing claims customers will save more than 20 percent in total cost of ownership on its electric machines in the average year, and the French company is aiming for 43 percent of its machine models to be low-emissions by 2030. The company has consolidated its roll-out of electric and hybrid aerial work platforms and telehandlers under its Oxygen Series. Manitou offered electric and hybrid version of virtually all new self-propelled booms launched in 2022.
Putting access in place
Development influences in response to complex market, emissions and regulation aside, rough-terrain telescopic booms continue to advance along their basic value proposition: taking people to work at height on unimproved job sites.
JLG now offers Quad Tracks for its 60-foot 600S (with a restricted maximum capacity of 1,000 pounds) and 66-foot 660SJ telescopic boom lifts. The tracks are also available through the aftermarket on other two-wheel steer models. Quad Tracks are triangular rubber-track systems, that bolt directly to the lift’s standard wheel hubs. This quick-change option can increase machine utilization and flexibility for working on a range of challenging surfaces such as sand, mud, gravel, grass, paved streets with curbs, potholes and sharp transitions.
The tracks improve floatation for minimal rutting of the job site, improve operator comfort over obstacles and create no “break-over” effect climbing obstacles such as curbs. Quad Tracks can be swapped out for regular tires when work conditions change, or for use on other models.
Measuring 34 inches high by 54 inches long by 18 inches wide, Quad Tracks minimize impact on ride height, maximum drive speed and the machine’s total width. A 600S or 660SJ boom mounted on the tracks does not require wide-load transport accommodations for transport.

“Quad Tracks offer an alternative solution: the ability to convert a normal, wheeled JLG boom lift into a highly capable, tracked machine,” says Randi McClure, Marketing Manager for JLG Boom Lifts. “This allows operators to cover a wide range of applications on multiple job sites with one machine.”
Genie says its S-80 J TraX is the only tracked, telescopic boom in the 80-foot class. The jibbed telescopic boom will lift 660 pounds to its maximum platform height of 80 feet and 55-foot horizontal reach. With tracks installed, the S-80 J weighs 28,700 pounds, 4,200 pounds more than when it is mounted on tires.
Genie also offers TraX on its 40-, 45-, 60- and 65-foot booms. The patented track design for two-wheel-steer machines will swivel vertically up to 20 degrees, improving the boom’s effective terrain range to 45 percent grades and smoothing the ride on rough ground. Maximum steer angle with TraX is 30 degrees.
STAY CONNECTED
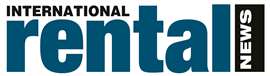


Receive the information you need when you need it through our world-leading magazines, newsletters and daily briefings.
CONNECT WITH THE TEAM
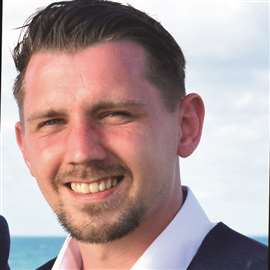

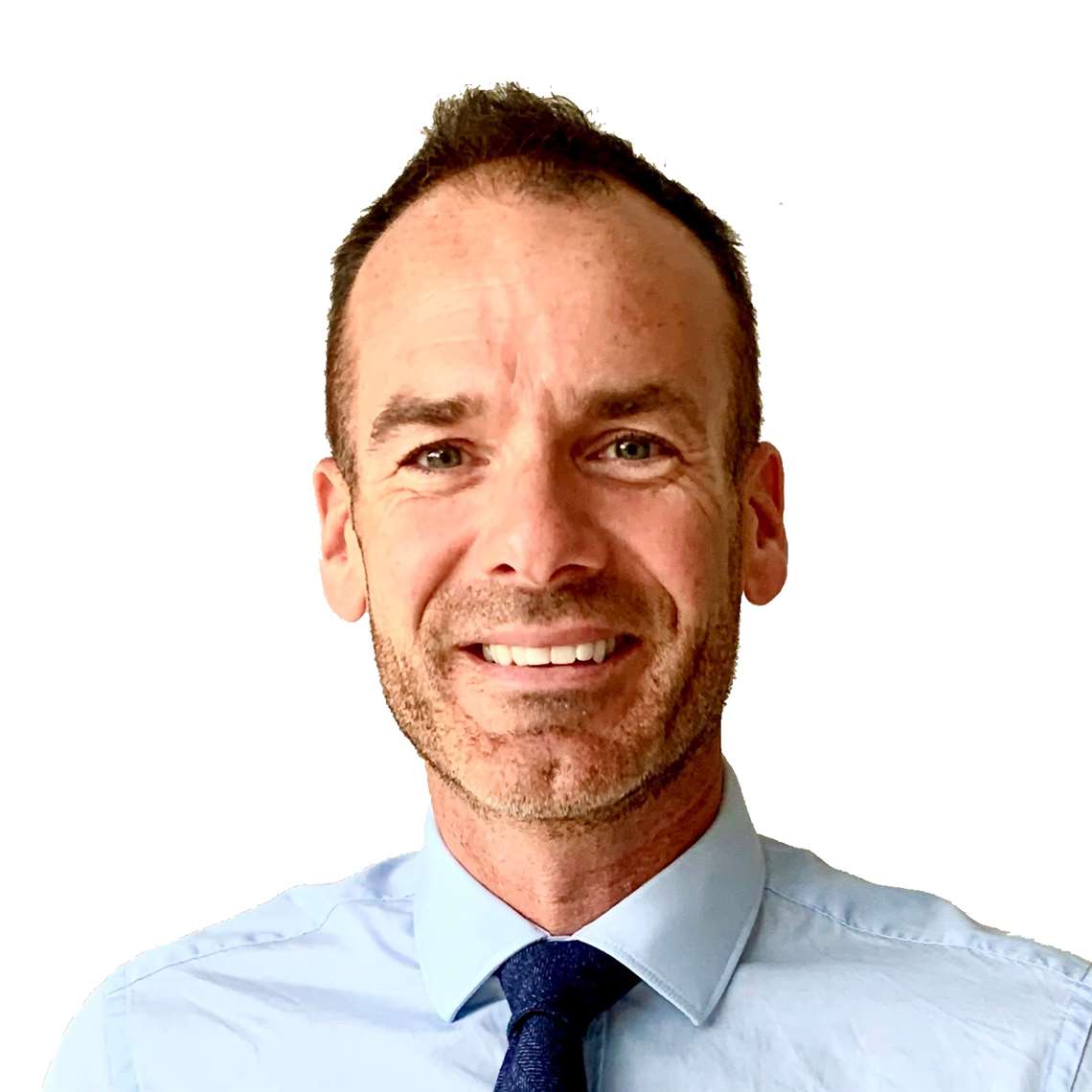