SPMT market is propelled by infrastructure projects
15 October 2024
The SPMT market is strong because users keep finding highly creative solutions using these versatile machines.
The advent of self-propelled modular transporters, known globally as SPMTs, opened the door for a new avenue of rigging innovation. Primarily, SPMTs were developed to move huge cargoes from one place to another. The modular design allowed SPMT systems to be built as wide and as long as required.
While they were primarily a transport mechanism, new features gave SPMTs the ability to become heavy lifters and tailing devices.
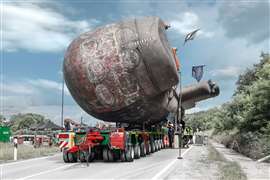
According to Roland Fischer, North American Sales Manager for TII Scheuerle and TII Kamag, customers have specific needs when they are adding a SPMT to their fleets.
“Primarily, customers are looking for the safest, most cost efficient and reliable way to accomplish their objectives to move heavy and large structures in a safe and efficient manner,” Fischer said. “TII-Scheuerle SPMTs can lift and move virtually all heavy loads as can be witnessed by watching our growing customer base on a daily basis.”
There are only a handful of SPMT manufacturers that produce these machines for North American customers, including Goldhofer, TII and Cometto (a Faymonville Company). Enerpac also competes in the SPMT market, generally with smaller scale SPMTs. Enerpac Tool Group recently acquired DTA, a leader in the industrial heavy loads transportation industry, designing and manufacturing mobile robotic solutions for handling heavy and special loads. According to Enerpac, this acquisition will advance the company’s pure-play industrial tools and solutions strategy by adding automated on-site horizontal movement products to complement its heavy lifting transport product portfolio.
Innovation in the design and development of SPMTs continues to advance, according to Fischer.
“Telematics, a cloud-based system, provides remote maintenance, diagnostics and troubleshooting support from our factory or service partners,” he said.
TII has also developed an online parts ordering app that gives customers another avenue for operating and maintaining their SPMTs in an effective, safe and efficient way, he said.
E-propulsion is another innovation that Fischer said is generating a lot of excitement.
“E-propulsion will be incorporated throughout the entire family of TII SPMT products,” he said.
As well, battery operated power packs are being upgraded for longer and more efficient usage.
“TII-Scheuerle is developing the next generation of a battery fed Power Pack Unit (PPU),” Fischer said.
The biggest challenges in the SPMT market in North America continues to be product availability, especially the parts needed to manufacture these machines.
“By this I mean the ability to get all the parts needed to manufacture the equipment in a timely manner,” he said. “Another challenge for our customers is keeping the equipment maintained properly when considering the high volume of jobs in today’s growing market. Fortunately, we have put many systems in place that allow us to support our customer base with reasonable delivery times, field support, training and technical support so they can perform their jobs efficiently.”
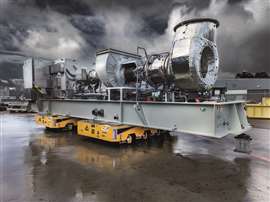
With the demand for SPMTs so high, there has also been a demand for repairing and refurbishing older SPMTs.
“This is a very important topic,” said Fischer. “TII Group has been building SPMTs for 40-plus years and we are very proud to see that nearly all of them are still in operation. We do, in fact, offer refurbishment and repair at TII group facilities in Germany as well as in Florida or onsite at a customer’s location through our sales and service partner TPSE, Inc.”
Goldhofer and Cometto also offer these services to their customers SPMT fleets.
One idea that is getting traction in the market is to pair different brands of SPMTs. While this isn’t commonplace, it is being done, although the manufacturers would rather see their brands exclusively paired.
Unconventional usage
A big user of SPMTs with a huge global fleet of all brands, Mammoet has used SPMTs in a variety of unconventional ways. Recently, the company turned SPMTs into giant forklifts for an offshore wind farm off the coast of France.
Situated about 12 kilometers from the island of Yeu, the Îles d’Yeu and Noirmoutier project marks the fifth offshore wind farm to be commissioned in France. It will be home to 61 offshore wind turbines, with an individual capacity of 8 MW. With an estimated annual production capacity of 1,900 GWh, it will generate enough electricity for approximately 800,000 people per year.
A client of Mammoet for many years, BOW Terminal approached its engineers to assist with the marshalling, movement and temporary storage of the offshore wind turbines’ transition pieces (TPs), which were being fabricated in Belgium. TPs are traditionally moved using crawler cranes or SPMTs fitted with a gantry system that requires assembly and rigging to be connected at a height over 20 meters.
This project marked the first opportunity for Mammoet to showcase an innovation that makes TP handling safer and more efficient for the offshore wind energy sector. It transforms SPMTs into giant forklifts – resulting in an offshore wind marshalling solution that is faster and more secure, the company said.
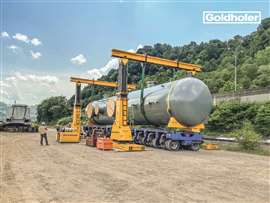
All 61 transition pieces were being shipped from Antwerp to BOW Terminal Vlissingen, the Netherlands. Each TP weighs 400 metric tons and measures 30 meters in height and 6 meters in diameter. Arriving by barge in fours, the TPs were lifted onto the quayside by a 1,200 metric ton crawler crane and placed onto temporary concrete supports. Each TP was then collected on a 2 by 14-axle line configuration of SPMT and moved to a temporary laydown area. There, they were placed on supports waiting to be called off, after which they were simply lifted and driven back from the storage area to a setup location on the quayside.
In the past, the SPMT trailers would be fitted with a gantry system that is constructed and parked over the top of the transition piece so it could be lifted from above. In this instance, Mammoet utilized a new attachment for the SPMT that essentially turned it into a giant forklift, allowing the units to be picked up more quickly and easily from underneath.
“BOW Terminal came to us and asked if we had a system like this available,” said Lars de Haas, project manager at Mammoet. “We explained that there was already a concept in progress, and we just had to develop it. This took around four months, including all fabrication and testing – which was carried out at BOW Terminal.”
The TPH800, as it is known, has a heavy lift capacity of 800 metric tons. It has two main cross beams that sit on top of two lines of SPMTs. From the cross beams hang two lower beams, which act like forklift forks. As the SPMTs approach the TP, the front cross beam lifts like a parking barrier to allow the lower beams to be slotted underneath the transition piece. Once these are in position, the front beam lowers and the TP is firmly locked into place by pinning both cross beams to both lower beams.
For offloading and loading the TPs, it is possible with the TPH800 to offer a RoRo solution that avoids the use of cranes. However, this was not the approach taken for this project. De Haas explained the reasoning.
“The crane was used here because bigger barges were needed in case of a roll-off, and we had to allow for the tide,” de Haas said. “In Vlissingen, there is about four meters of tide. Using a crane, you are tide independent and can carry out work 24 hours a day if needed.”
While the TPH800’s strength comes from its ability to provide a system for lifting and moving transition pieces that is safer and more efficient than pre-existing methods, Mammoet’s flexibility also played a part in the success of the project, de Haas said.
With a single barge shuttling between Antwerp and Vlissingen, arriving in a sequence ranging from seven to 10 days, Mammoet’s team was able to be both flexible and responsive in mobilizing a crew for the two-day windows needed to offload and store the TPs.
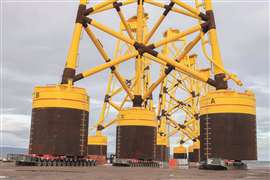
Rotating a submarine
Similarly, the transport of the 350-ton U17 submarine from the Speyer Technology Museum to its sister museum in Sinsheim, Germany was a spectacular showcase of SPMT technology. The Kübler team transported the submarine over land on 30 Scheuerle InterCombi axle lines. The challenging route and the special cargo required precise maneuvering and several balancing acts. This heavy haul involved the world’s first rotation of a submarine on a modular transporter.
In August, tens of thousands watched the progress of the submarine transport on television and the internet. The sub measured 90 meters long and 10 meters tall and had to pass under low bridges and high-voltage power lines, besides navigating along the narrow roads and streets of the hilly Kraichgau region. To pass safely under the obstacles, it had to be repeatedly rotated by 70 degrees or more around its longitudinal axis by means of a special piece of equipment. As a result, the tower was positioned to one side, and within a few minutes the height of the transport was reduced to the required clearance.
The transport began on the Rhine and Neckar Rivers, where the submarine was initially loaded onto a river pontoon positioned on 30 InterCombi axle lines from the TII Group. Both the loading and unloading of the transport – which weighed around 500 tons – onto the floating load carrier was a balancing and ballasting act. The 66-meter long and 11.5-meter wide pontoon had to be constantly re-leveled to compensate for the constantly changing load situation.
Before the roll-off took place in Haßmersheim, the teams from Kübler, Fischer Kran Transporte, Van der Wees and the Sinsheim-Speyer technical museums had to work together to jack up the U17 to a height of 1.4 meters using eight hydraulic cylinders so that the 30 Scheuerle InterCombi axle lines could then drive under the submarine again for the final landing.
The final kilometer to the Sinsheim Technology Museum saw music bands and thousands of onlookers. The crowds gave the submarine a worthy reception while the Frieder Saam team took the last turn onto the museum grounds and parked the relic in front of its future location.
STAY CONNECTED
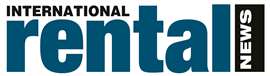


Receive the information you need when you need it through our world-leading magazines, newsletters and daily briefings.
CONNECT WITH THE TEAM
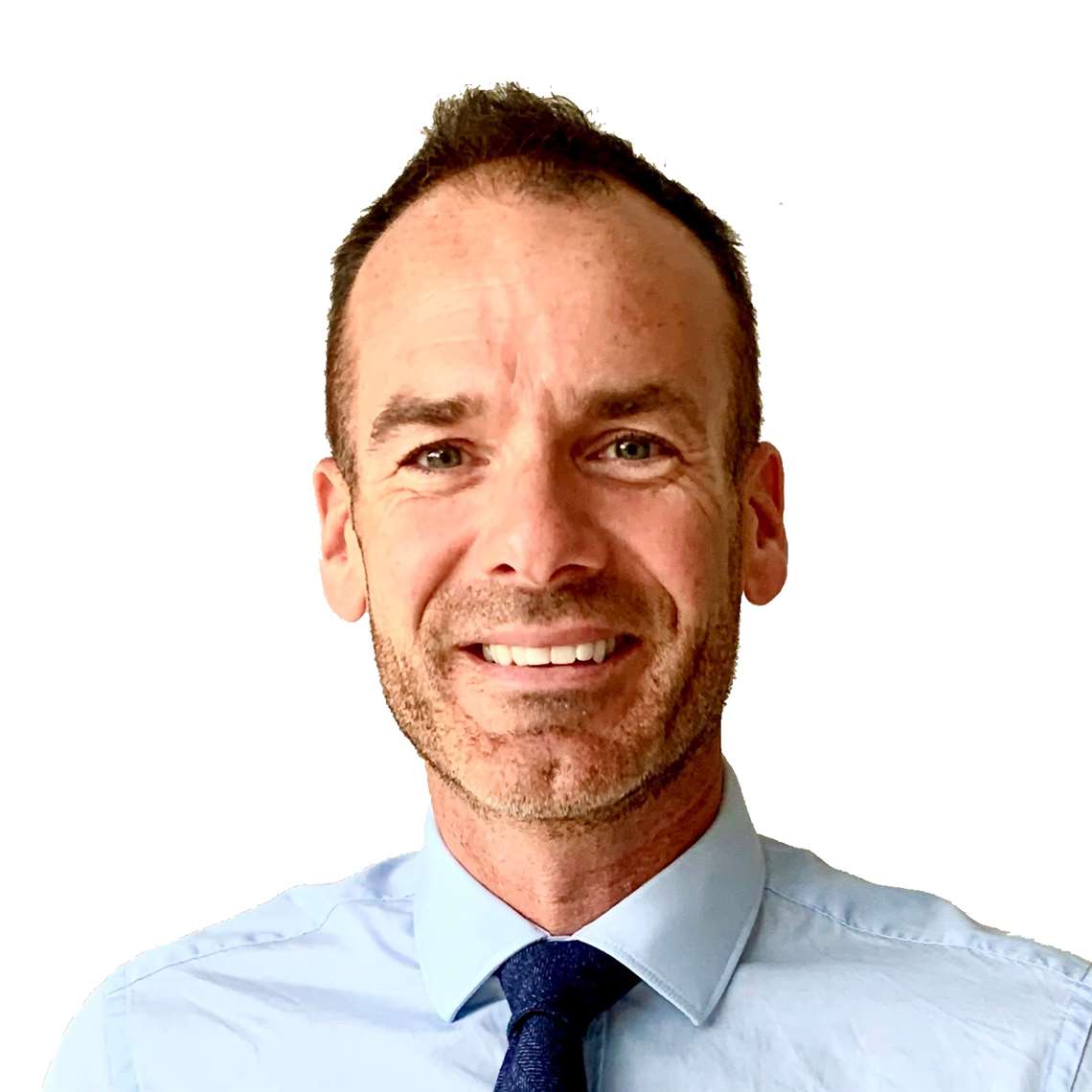
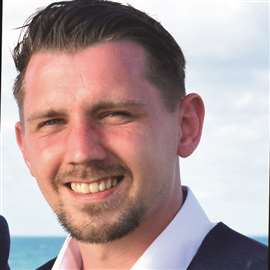