Street Smarts: New Jacobs tech ready for the road
02 January 2023

At the 2018 IAA Truck Show in Hanover, Germany, Jacobs Vehicle Systems – inventors of the famous “Jake Brake” diesel exhaust brake – announced it was working on a new, variable-cylinder system for heavy-duty diesel engines. After a long delay thanks to the COVID-19 pandemic, in early November, Jacobs was finally able to give journalists a first-hand look at its new Cylinder Deactivation (CDA) system, as well as a new Active Decompression Technology (ADT) system that eliminates diesel powertrain vibration when cranking or shutting an engine down.
Variable-cylinder technology – also called “displacement on demand” – is an electronic engine control system that activates or shut downs engine cylinders based on real-time powertrain need. The technology has been in common use on passenger car gasoline engines for over 20 years and the concept is simple to grasp: it gives the driver full V8 power at low speeds and gradually deactivates cylinders as the vehicle gains speed. The engine doesn’t need all eight cylinders to maintain highway cruising speeds, for example. So, the system will shut down four cylinders for optimal fuel efficiency until more power is needed – when passing, for instance.
Reducing emissions
Jacobs’ CDA will offer similar fuel economy advantages for Class 8 trucks and tractors, but that’s not its primary purpose on near-future powertrains, according to Steve Ernest, vice president of engineering & business development, for Jacobs. “CDA is a modular valve actuation technology that improves fuel efficiency by turning a six-cylinder engine into four cylinders or less, potentially improving the overall fuel economy by as much as 25%,” he explained. “However, CDA also reduces emissions by achieving higher exhaust and aftertreatment temperatures at low-load and startup.”
And that’s where Jacobs believes CDA will have the most benefit for fleets by helping them dramatically reduce low-load/low-speed diesel exhaust emissions, which will be a primary target for the next round of U.S. Environmental Protection Agency greenhouse gas emissions regulations for heavy trucks, set to hit in 2027. In a low load cycle, Ernest said a Class 8 truck equipped with Jacobs’ CDA and a selective catalytic reduction (SCR) system experienced NOx emissions reductions of 77% with 12% less CO2.
Jacobs has its CDA sights set squarely on diesel engine OEMs, added Robb Janak, director new technology, Jacobs Vehicle Systems. “Commercial vehicle manufacturers are looking for new and improved technologies to comply with stricter legal limits on CO2 and NOx emissions – in all parts of the world and ideally via one global engine platform. Cylinder deactivation is technically proven in the latest tests, such as Real Driving Emissions and CARB Low Load Cycle for heavy-duty trucks, to address these requirements.”
Jacobs’ CDA hardware has so far been demonstrated on more than 20 different heavy-duty engine platforms, Janak noted, covering 2.0 to 15 L engines, as well as 10 different heavy-duty truck road tests in North America, Europe, China, Japan, Korea and India. It has also undergone more than 27,000 hours and more than 200,000 miles of durability testing. There have been more than 8 billion test cycles on CDA components and over 470 million cycles of fatigue and overload testing.
Team-up with Tula
A key component to CDA has been Jacobs’ collaboration with internal combustion controls company Tula Technology, which was inked in 2019. The two companies are working closely together to combine Tula’s Dynamic Skip Fire (DSF) controls technology with Jacobs’ CDA, where DSF optimizes Jacobs’ engine cylinder shutdown management to best meet torque demands and eliminate vibration.
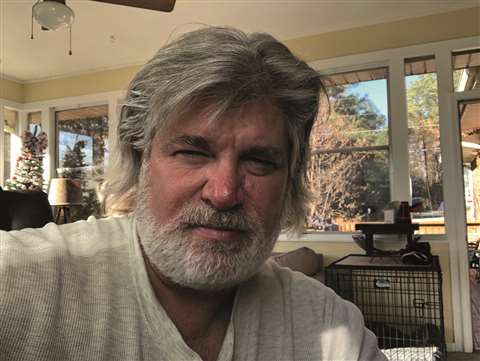
According to Janak, Independent laboratory testing has demonstrated that, when combined, Jacobs CDA hardware and Tula’s DSF achieve greater emission reductions. In DSF, Tula has developed an infinitely variable cylinder deactivation control system, integrating advanced digital signal processing and software with sophisticated engine control algorithms that can allow CDA to be used in a larger operating range of speed and torque than traditional CDA.
Jacobs new Active Decompression Technology works by keeping engine valves open and the cylinders decompressed. When switching off the engine, it “coasts” to a smooth shutdown without causing the cabin to shake – eliminating the famous “diesel death rattle” almost completely.
When starting up, Janak explained, the engine is kept in a decompressed state that decreases cranking torque by 40% and allows the engine to spin up to twice its normal speed for smoother starting, faster priming of the fuel system and decreased wear on the starter gear, flywheel and other components. This can also allow the use of smaller and lighter batteries, cables and starter. Jacobs ADT also helps with driver retention by allowing them to rest better in hotel mode, without being repeatedly awakened by the diesel engine starting up or shutting down, Janak said.
STAY CONNECTED
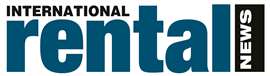


Receive the information you need when you need it through our world-leading magazines, newsletters and daily briefings.
CONNECT WITH THE TEAM
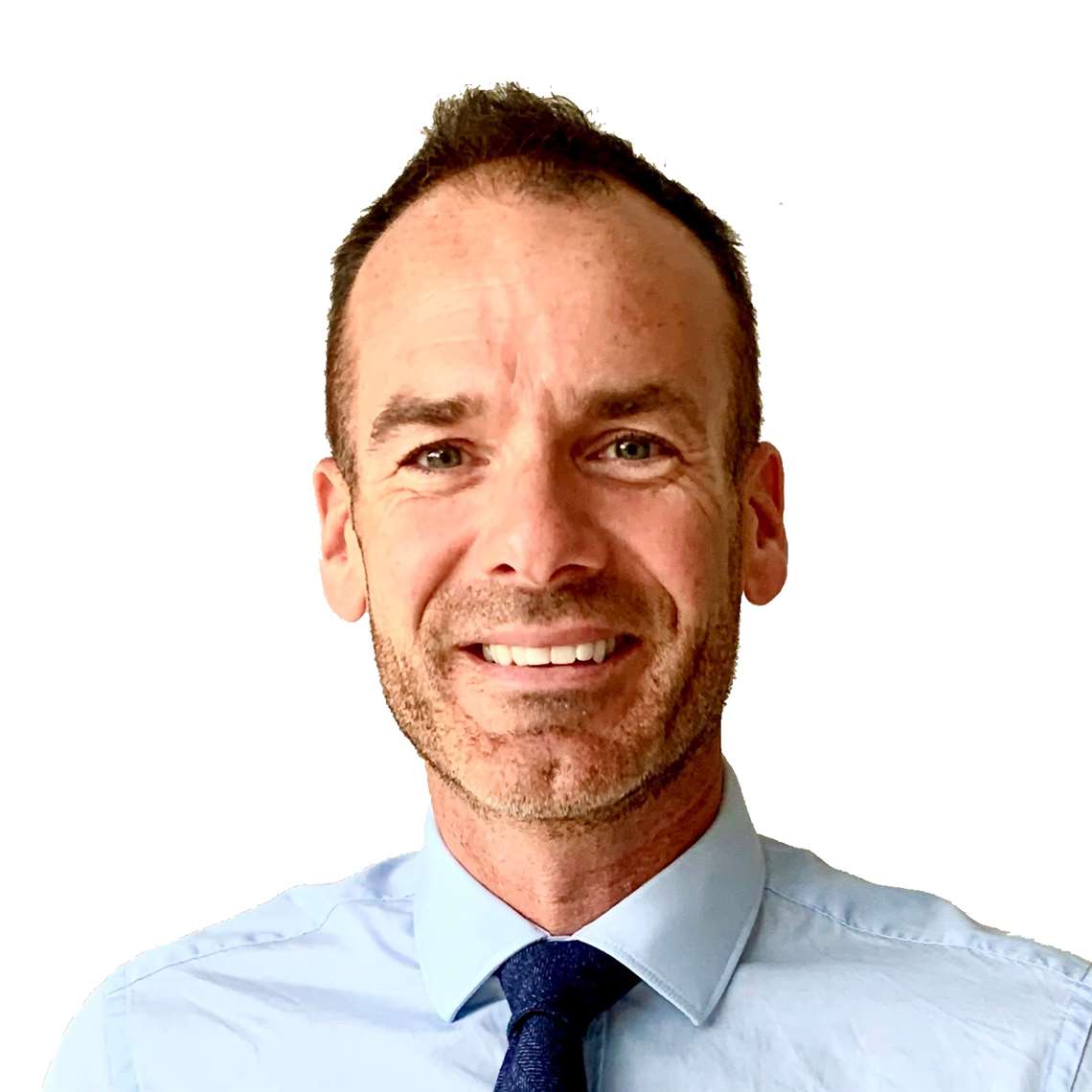
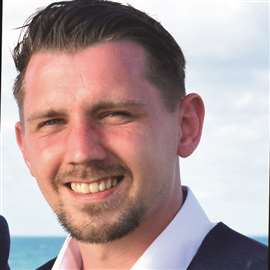