Street Smarts: Trucking’s Emissions Pushback Begins
22 July 2024
Major industry players voice concerns over EPA’s aggressive emissions regulations.
In a previous Street Smarts column, I noted that major problems concerning the looming U.S. Environmental Protection Agency (EPA) 2027 diesel exhaust emissions regulations remain unresolved, particularly for long-haul segments of the trucking industry. My growing feeling is it’s time to develop a more reality-based solution to help trucking transition to a zero-emission industry as soon as possible – with as minimal disruption to business and supply chain issues as possible.
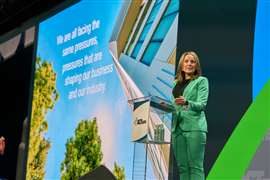
There have been signs of brewing discontent in the industry for well over a year now, and I’ve been wondering when some sort of a pushback against these regulations would begin.
Well, I need wonder no more.
At the Advanced Clean Transportation (ACT) Expo in Las Vegas, May 20-23, two major players in the trucking industry sounded the alarm about the owning and operating costs of battery-electric trucks. Both J.B. Hunt and Ryder System now have enough operational experience and data piloting battery-electric trucks to draw some real-world conclusions.
Their findings are alarming – if not entirely surprising.
Uncompetitive and Inefficient
Shelley Simpson, president of J.B. Hunt Transportation Services, spoke from the mainstage on May 21, warning attendees that, based on the fleet’s initial data, battery-electric trucks are currently far too expensive to offset any benefits they deliver. Equally problematic, the trucks themselves are “uncompetitive and inefficient.”
Simpson warned attendees that battery-electric truck acquisition costs are up to three times that of a diesel. Fleets must also contend with payload penalties of between 4,000 and 12,000 lb., and charging time and frequency render them very unproductive compared to diesels.
“It’s not economically viable to incorporate zero-emission vehicles into our fleet at scale right now,” Simpson said. “But it is important that we begin to test and to pilot these technologies.”
Infrastructure has emerged as a serious long-term barrier to the widespread deployment of electric trucks, as well. Simpson had a sobering assessment on that front, too.
She noted that the American Transportation Research Institute has found that the U.S. would need to generate 40% more electricity than is currently produced today if all 276 million registered cars and trucks in this country were electric vehicles.
“In order to fast-charge a single electric truck, you would need the same amount of energy it takes to power 600 homes,” she said. “To put that into perspective, the fast-charging infrastructure needed to support J.B. Hunt’s entire fleet, if it was all electric, would be the same as that required by 1.4 million households, or about 1% of the U.S. population.”
A Tough Sell for Fleets
The following morning, in his own mainstage address, Robert Sanchez, Ryder System CEO and chairman, told ACT Expo attendees that the business case for electric trucks is more expensive for fleets than first anticipated.
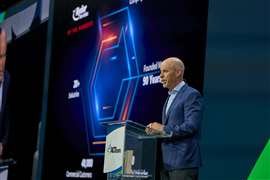
Sanchez acknowledged that when looking at diesel versus electric in light-, medium- and heavy-duty commercial vehicles, Ryder fleet managers expected to see some cost increases for adopting battery-electric vehicles (BEVs). But Ryder did not expect to see the magnitude of those costs – which he said was a major problem.
“We found that there was a significant barrier to conversion in the total cost of transport, or the TCT,” said Sanchez.
He went on to explain that TCT factors in the cost of vehicle, fuel or electricity, driver wages, as well as other factors that go into transporting the same load the same distance and in equivalent delivery times. Based on those numbers, he said, the business case for converting to BEV technology just isn’t here yet.
More to the point, Sanchez said Ryder found that the average load today requires nearly two additional electric trucks and more than two trailers to deliver the same load in the same time as currently transported by a single heavy-duty diesel truck. That’s more than double the TCT at the end of the day.
“I think most of you would agree that this is a tough sell,” he commented.
Ryder also looked at the range and payload requirements needed to achieve equivalent diesel delivery targets and uncovered some fairly alarming numbers.
For example, in light-duty applications, Sanchez said it currently costs an average of about $170,000 a year to run a single diesel Transit van. But for electric delivery vans, that cost increases an estimated 3%, while the acquisition cost of the vehicle itself nearly doubles.
The numbers become more problematic as the trucks get larger, he warned.
For example, looking at Class 8 truck operations in Georgia, Sanchez noted it costs a fleet about $291,000 to run a diesel-powered truck. In California, by comparison, that number is about $334,000 per year.
But given current BEV range and payload limitations, Sanchez said it could require nearly twice the equipment and more than twice the labor compared to a diesel truck for fleets to deliver the same loads. So, in Georgia, an electric truck would take $622,438, and in California, the cost would increase to $648,712 to deliver those same loads.
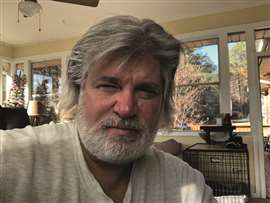
Overall, Sanchez said Ryder estimates cost increases of 94% to 114% to convert heavy-duty trucks to EVs and 56% to 67% to convert mixed fleets of 25 vehicles, depending on which state the fleet is in.
Still Early Days
Both Simpson and Sanchez noted that these are early days for electric trucks, and these numbers aren’t carved in stone. More electric truck production will bring acquisition costs down, for example, and faster charging times will definitely bring more favorable labor costs and driver efficiencies into play.
But these numbers highlight some very serious operational barriers to electric truck operation by fleets which are going to have to be dealt with before widespread adoption can be expected.
STAY CONNECTED
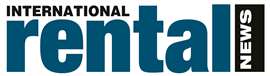


Receive the information you need when you need it through our world-leading magazines, newsletters and daily briefings.
CONNECT WITH THE TEAM
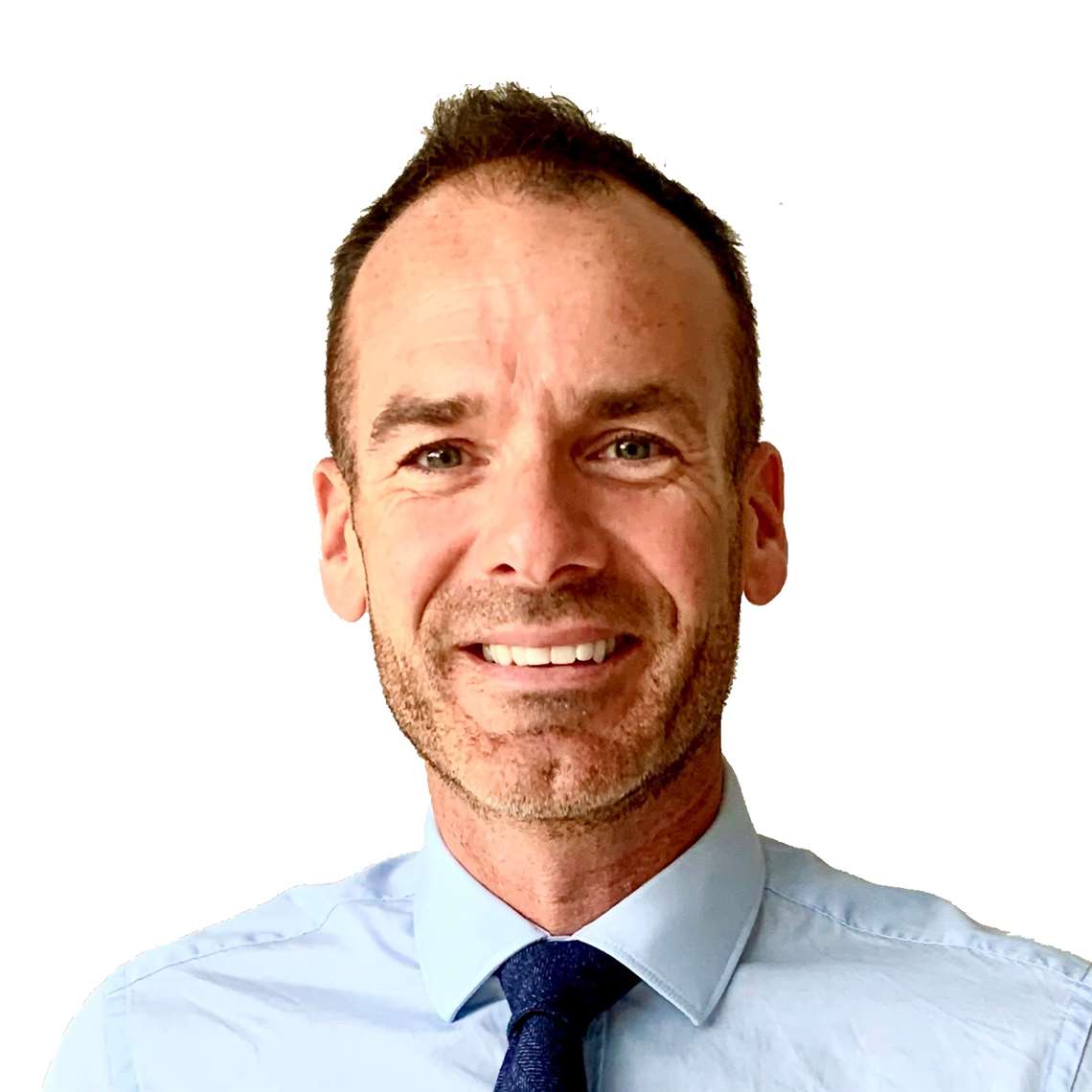
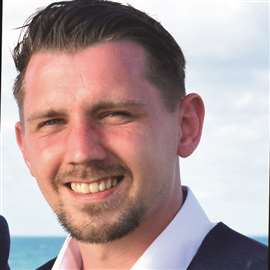