Tunnelling: Underground sucesses
03 June 2011
Top of the tunnels list is the world's longest transport tunnel, the 57 km long twin bore, high speed railway tunnel underneath the Gotthard Pass in Switzerland's high Alps. A significant milestone was achieved last year when one of the Herrenknecht Tunnel Boring Machines (TBMs) driving the eastern tube of the 8.5 m diameter bores broke through to set a new world record for the longest tunnel.
Ten years of excavation, half by drill and blast and half by TBM, under mountain cover of up to 2500 m, had involved work with incredible rock pressures and high rock temperatures up to 50° C.
Full completion of the total 152 km of tunnels and side caverns was achieved in March when another Herrenknecht ended the second western tube. Lining work continues and railway and signal installation will follow before the first high speed trains run in 2016.
An enormous 650 m work train, christened the "Worm" is being used for re-profiling some of the tunnel, cleaning it, installing drains and forming the linings. It is supplied by Herrenknecht subsidiary Maschinen und Stahlbau Dresden (MSD).
Gotthard is not the only tunnel on the high-speed link. Work has also begun on the 15.4 km long Ceneri twin bore tunnel further south in Italian speaking Switzerland, passing under the 1100 m Monte Ceneri near Locarno.
The drill and blast drives are using primarily Sandvik 1300 three-boom rigs and with a long ceiling suspended back-up train system from Rowa. Two drives each north and south are heading out from a central cavern accessed by a side adit driven two years ago by a Robbins main beam TBM at Sigorino. Breakthrough is due in 2016.
Progress on the dramatic Alpine links is also underway in neighbouring Austria now fully committed to construction of the Brenner Pass tunnel, another deep-level flat-gradient tunnel deep under the mountains for heavy freight trains and superfast 250 km/hour passenger trains.
The 55 km long twin bore tunnel will almost match the Gotthard and, if a link into an existing bypass tunnel at the Tyrolean capital of Innsbruck is taken into account, will exceed it. Pan-European trains heading for Berlin, Germany in 2025 from Italy will connect straight into the bypass giving a total underground length of 62.7 km.
Italy committed funds last year and Austria this year for work on the twin main drives to begin in 2016. Unlike Gotthard, the Brenner will have a third central service tunnel 6 m in diameter which has already been underway for some time in order to explore the rock conditions. A 10.5 km drive from the Italian end completed last year under an € 80 million (US$ 115 million) contract with a seven company Austro-German-Italian consortium led by Pizzarotti and Condotte. Italy's Seli supplied the 130 m long support train behind a behind a 6.3 m diameter reconditioned Aker Wirth cutter head.
A second drill and blast south from Innsbruck, Austria has so far found better rock than expected giving hopes the main drives might have better rock conditions than previously thought.
The Brenner is part of a key route for the Trans European Network (TEN) from Palermo, Sicily to Berlin, Germany and eventually Scandinavia. German Federal Railways is currently building more than 20 tunnels on a new 85 km section of high speed line between Nuremberg and Erfurt and more on the link on to Leipzig.
Though mainly small, they include four significant projects on the southern section, the 3.8 km long Eiberge tunnel and the 2.7 km Reitersberg, both are twin bore drill and blast projects as are two longer ones, the 8.3 km Blessberg and the 7.4 km Silberberg. Wayss & Freytag, Bilfinger Berger, Max Bögl and Bickhardt Bau are about halfway through the work.
On from Erfurt are three more tunnels, two of which, the Finne at 7 km and the Bibra at 6 km are almost continuous with only a small valley separating them. Bibra's recently finished twin bores through dewatered sandstone were also driven by drill and blast by contractor Porr Tunnelbau of Austria.
On the Finne tunnel, contractor Wayss & Freytag in joint venture with Max Bögl and Porr Tunnelbau, faced heavy faulting and water inflow. Two dual mode Herrenknecht Mixshield TBMs were used in sealed slurry mode for the first 1500 m, switching to open shield excavation with spoil conveyors for the remainder.
By staggering the drives the contractor was able to use only one bentonite slurry spoil plant for each machine in turn saving money. Cross connections by drill and blast are being completed as is lining work, with opening scheduled for 2016.
The same contractor, this time in the Locobouw consortium with France's Vinci Grand Projects and with two local companies MGB/CFE and CEI-de-Meyer, is facing difficult challenges on a new railway tunnel underneath the docks in Antwerp, Belgium.
The 6 km long twin bore rail freight tunnels to service the huge container port must pass just under the river Scheldt and a wide ship canal with almost no cover. A huge concrete slab has been poured into a dredged space in the canal bottom to serve as a roof for the twin Mixshield TBMs from German maker Herrenknecht. To deal with high water pressures in soft sands and clays these are capable of working in pressure up to 4 atmospheres. The 7.5 m diameter drives are currently about halfway.
Such machines pale into insignificance compared to the giant TBM which has recently arrived in Italy for building the Sparvo tunnel on Italy's A1 Autostrada upgrade in the mountainous area between Bologna and Florence.
Giant TBMs
Two bores of 2.5 km are needed by client Autostrade per l'Italia, one each way for two lanes of road and an associated emergency lane, requiring a finished width of
13.6 m. Construction width means the earth pressure balance machines have an external diameter of 15.6 m, claimed by German maker Herrenknecht to be the largest TBM made so far.
Contractors Vianini Lavori, Toto Costruzioni Generali, and Profacta will use the one 4300 tonne machine for both bores - the first northwards drive is now getting underway.
Such giant machines are becoming a more familiar sight following the completion of a road tunnel drive in Shanghai and another crossing of the Yangtze at Nanjing, China.
Now one is likely to be seen in the US where the Washington State Department of Transportation has signed a US$ 135 million contract for the Alaskan Way tunnel project in January this year, with a joint venture of Dragados USA and Tutor Perini.
The scheme will create two large diameter 2.7 km long tunnels to replace the existing waterfront elevated highway structure through the busy city.
The two bores, one above the other would each carry two lanes of traffic and have additional 2.5 m safety lanes. Design build studies will determine the exact diameter but it will be substantial. As the client points out "members of the team delivered the comparable 49.5 ft (15.2 m) diameter Madrid M-30 highway tunnel in Spain."
Another giant TBM project reached breakthrough just north of the US, on the Canadian side of the Niagara Falls. This time the machine is a hard rock main beam machine from Robbins, with a diameter of 14.4 m, which has battled through a difficult 10.5 km long drive for a new power supply tunnel for the Sir Adam Beck generating plant, one of the first hydroelectric power stations in the world.
The Queenston shale gave considerable difficulties to main contractor Strabag, requiring the tunnel alignment to be raised by 45 m early on to move it into more stable rock. Crews had to safely scale down loose rock from the tunnel crown.
The Robbins machine managed to achieve two records for
11 m+ diameter boring - 468 m in one month, and 153 m in one week. The Niagara Tunnel Project was initiated in June 2004 by Ontario Power Generation and drives began in 2006. Two years of work still remain for concrete lining.
Another major hard rock drive is just reaching completion, this time in Manhattan, New York, US where the two machines which began a complex of tunnels for the East Side Access in 2007 were due as iC went to press. The tunnels will bring trains from Queens side of New York into a giant tunnel complex underneath Grand Central Station. This is formed from four upper and four lower tunnels created by forks in the access drives. One Seli and one Robbins TBM made first a 2.1 km top tunnel and then withdrew for a lower level branch to be formed.
The upper and lower tunnels then each split into left and right. Below the station additional side branches were bored to create a complex of four upper and four lower tunnels. The joint venture of Dragados and Judau which constructed the tunnel now has a US$ 500 million contract to excavate around the two levels of four tunnels to make giant twin caverns for the underground station which should see service in 2016.
In February, Manhattan also saw completion of the first
2.1 km long bore of the new Second Avenue subway line from 96th Street to 65th Street using a reconditioned Robbins TBM. The machine has been pulled back and started the second slightly longer 2.3 km drive for the twin bores in late March, the first 60 m through frozen ground. It will drive all the way to the end of the first phase section at 63rd Street.
Meanwhile major tunnelling is underway in Mexico City where a Robbins Earth Pressure Balance (EPB) machine, the largest in the country at 10.2 m diameter is over 3.5 km along the route of the capital's Metro Line 12, the 'Gold Line'.
It began work in February last year in watery clays but now moves into mixed sandy ground with boulders up to 800 mm, which it is designed to cope with, though requiring conversion of the muck system and conveyors at a halt in the Eje Central cut and cover station site.
Three other Robbins machines of 8.93 m diameter are waiting to start work on drives for the huge 60 km length of the Emisor Oriente Wastewater Tunnel, probably this summer. German maker Herrenknecht has also supplied three machines for the huge scheme.
Large scale wastewater tunnels are underway in the Middle East where this spring the emirate of Abu Dhabi let the third contract for its 41 km of deep sewage tunnel, a US$ 270 million contract for 16 km of 4 m internal diameter tunnel. The central 15 km long section is being driven with three 6.3 m diameter EPB machines under a US$ 200 million contract and a second 10 km long, 7 m external diameter drive has also been awarded.
China too is boring water tunnels, with work in several cities continuing on metro schemes where large number of Herrenknecht and Robbins machines have been used. But it also has water tunnels like the Pinglu scheme were breakthrough of a 25.4 km long drive was achieved late last year by a 4.8 m diameter Robbins double shield TBM used by contractor, the Sino-Austria Hydraulic Engineering Company, a joint-venture led by Alpine Bau. The work is for the Yellow River Water Diversion Project.
China is also turning more and more to advanced equipment reports Sandvik, with the contractor Department #1 of the Tunnelling Bureau using two Sandvik Axera T11 jumbos for work on a twin bore rail tunnel.
The 13.3 km long Chang Hong Lin in low mountain foothills up to 420 m deep in mainly shale rocks has two drives of 10 m height and 13 m width. Sandvik said both have gone much faster than with traditional hand held pneumatic drills.
Immersed tubes
Lastly, immersed tube tunnels have also seen major success. In South Korea the Busan Geoje link opened this year including a 3.7 km long immersed tube which as 48 m depth is the deepest in the world for roads.
Specialist Dutch firm Strukton, which aided the work, is busy with dredging partner Van Oord in the Netherlands for an extraordinary immersed tube project which includes floating a 130 m precast tunnel section underneath the 110 year old Amsterdam central station where a giant 20 m water filled cavity has been created supported by massive pile walls. The section for the North South line metro goes in this summer and then three other pieces will extend the tunnel across the river Ij.
In Vietnam, this June sees the opening of South East Asia's first immersed tube tunnel, the Thu Thiem underneath the Saigon River, part of Ho Chi Minh City's US$ 600 million East-West Highways Project. The designer was Japan's Pacific Consultants International and contractor for the four section tunnel was Obayashi. For the challenging waterproofing of the four 92.4 m long sections, each 33.3 m wide and 8.9 m high, the team used the Stirling Lloyd Integritank system.
Meanwhile, February saw the Danish government announce that it favoured an immersed tunnel design for the € 5.1 billion (US$ 7.3 billion) Fehmarn link between Germany and Denmark. Construction of the 18 km link is due to start in 2014, with completion in 2020.
Good health
The range of major tunnelling projects around the world certainly paints the picture of an industry in good health - not only because of the sheer number of schemes, but also the increasing size and complexity of work being undertaken. And schemes like the Fehmarn Link also illustrate the popularity of tunnelling, compared to more conventional solutions like bridges in some cases.iC
STAY CONNECTED
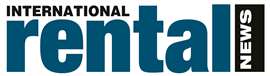


Receive the information you need when you need it through our world-leading magazines, newsletters and daily briefings.
CONNECT WITH THE TEAM
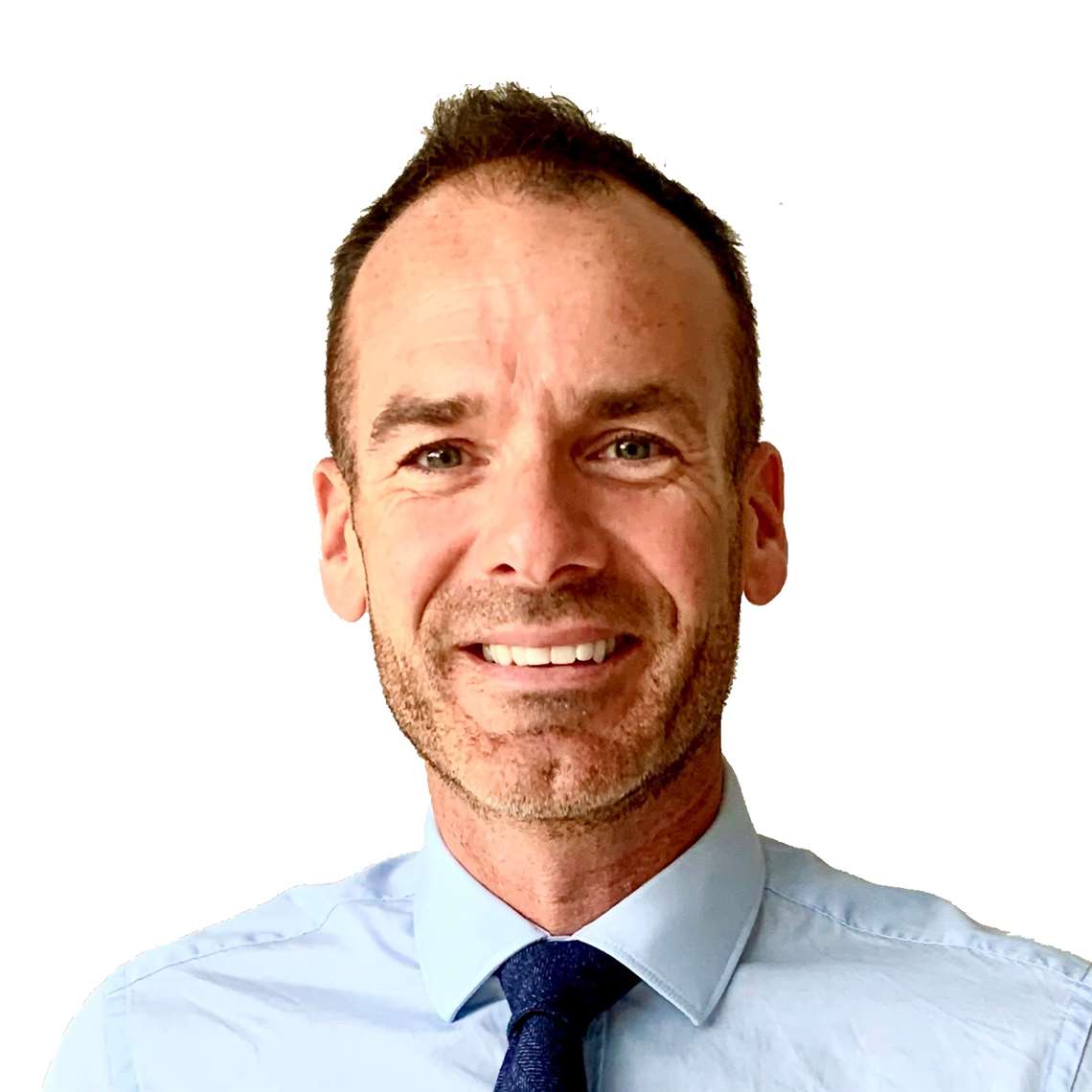
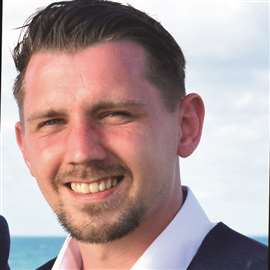