Achieving zero-emissions means electrifying entire job sites
10 June 2024
If the world wants to advance electrification in construction then it means electrifying entire job sites, says ZQuip’s managing director Chris LaFleur.
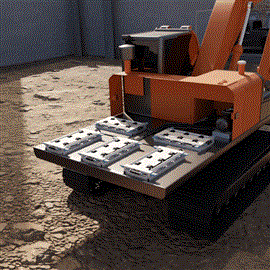
There’s a problem with how the world is advancing electrification, specifically in construction.
If the goals for electrification include aggressively reducing emissions, slashing the amount of energy required for manufacturing, and curbing the consumption of raw materials, then buying electric construction machines one at a time and dropping them into a job site is neither productive nor efficient.
The construction industry is pouring money and effort into the design and development of electric solutions yet adoption lags.
In contrast, 41,320 diesel-powered excavators alone were purchased in North America during 2022, according to analysts at Off-Highway Research. If the purchase of off-highway electric vehicles spiked overnight, what is a sustainable solution for using tens of thousands of diesel-powered vehicles that could last decades?
According to a report from consulting firm Roland Berger, the push to electrify off-highway vehicles stems, in part, from government regulations to lower emissions and noise as well as a desire for fuel efficiency.
“Emission standards in the US, Europe, China, and India are increasingly becoming stricter. Although heavy-duty vehicles still aren’t required to meet specific CO2 targets, that could change as early as 2025 … ,” notes Roland Berger’s research. “Leading industrial manufacturers including Komatsu, CAT, Hitachi, John Deere, and Volvo expect between 20-50% in fuel cost savings for electrified off-highway vehicles.”
Roland Berger goes on to predict that compact and mining vehicles will lead the road to electrification. There is already innovation with machines like all-electric skid steers from Bobcat and mining trucks made by Epiroc, along with charging technology to support this equipment. Some mining equipment OEMs have created services for battery-swapping on their massive electric-powered vehicles to increase run time and mimic the way owners of cordless hand tools swap batteries to keep working. There are 18-mt payload loaders now working on mining sites with up to 450kWh of usable battery capacity and swappable batteries. The idea of swappable batteries is terrific, but the batteries in one OEM’s mining vehicle can’t be swapped with another manufacturer’s machine.
Regardless of the environment, construction professionals ask themselves two things: What is the amount of work I can get done in a day, and what is the cost of that work?
Electrifying job sites
Instead of focusing on electrifying specific vehicle makes and models as standalone projects, the world of construction should electrify job sites and entire vehicle fleets.
This means separating the machine from the battery. Consider the concept of modularity, in the form of a high-voltage battery module, which would propel the adoption of electrification. By analyzing what must happen on a zero-emissions job site to complete a day’s worth of work, project managers could then decide how much battery capacity their machines need. For example, when workers use a drill, they choose the correct size battery for the work planned or make sure they have enough spare batteries on hand.

For construction machines, ensuring enough run time is critical. To do this, OEMs and customers feel as if they must equip their machine with the largest battery possible (e.g., 800kWh) to get things done and have energy to spare. Maximizing the size of your battery only maximizes the machine’s price tag.
The challenge isn’t maximization but optimization. But even the oversized battery on a more expensive electric excavator doesn’t guarantee clearing a high hurdle to adoption: Eliminating range anxiety and getting the job done regardless of conditions.
To electrify job sites and achieve zero-emissions, the construction industry should begin converting existing diesel-electric construction vehicles to modular battery power. These converted machines can run on fast-charging, swappable battery modules that fit any make and model of machine. Plus, when the modules aren’t on a machine, they can serve as gensets: running lights, heating, or cooling trailers, and more.
Modularity in practice
Imagine converting a diesel-powered Caterpillar excavator to an electric model while doing the same with a Komatsu wheel loader and Bobcat track loader, and then, being able to use the same size battery module across the three machines running on a job site.
The excavator might require three or four high-voltage battery modules, the mini track loader one module, and the wheel loader two. The combination of battery modules on each machine would discharge sequentially, although they could be programmed through software to provide power in parallel.
This approach gives customers zero-emissions machines with the exact battery capacity for the job to be done. Let’s say the excavator runs low on energy. The wheel loader can pull up alongside and connect one of its battery modules to “top off” the excavator’s module or even lend one of its battery modules with the help of a telehandler. With a model like this, machine operators could swap batteries between machines, carry out machine-to-machine charging with a high-voltage cord, or quickly charge a machine from a standalone module or fast-charging system.
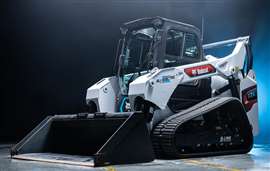
Consider a construction site with six machines using interchangeable battery modules; two need 800 kWh of battery capacity while four require 400 kWh each. The total energy for the day equals 3.2 mWh, or twenty-three140-kWh battery modules. In contrast, the traditional all-electric vehicles that some OEMs are making come equipped with, say, an 800-kWh battery on each of the six machines mentioned above. In this scenario, the owner would pay 50% more for battery capacity that goes unused. The value of modularity is twofold. First, all machines have a fast-charging power supply that is swappable. Second, energy capacity matches the work required. In other words, the job site always has the right amount of power when needed. Equipment owners and renters shouldn’t pay for power they don’t need.
Part of the promise of electrification is incorporating software that controls and monitors functionality that isn’t possible with legacy diesel-hydraulic machines.
The concept of a swappable battery module across all types of machines would include a software layer that enables an electric motor, smart controller, and thermal kit to regulate the battery module’s temperature to operate efficiently in all climates.
And it would send information to equipment owners, rental companies, and distributors, so they know what kind of job their machines are doing and how much energy they are consuming. Knowing well in advance that a battery module is running low enables an operator to swap a module in less time than it takes to fill up with diesel.
If a rental company owns the machine, the battery module’s software alerts the firm to deliver one or more modules to the job site. The machine gets its fresh battery module when it’s convenient for the operator to pause and swap batteries. This eliminates range anxiety and ensures the equipment owner is only paying for the battery power they need for the work on that job site, for that day.
Making diesel-electric conversion work
Converting diesel machines to battery-electric using a modular approach tackles the issues slowing adoption. Here’s how it can work: The conversion process requires removing the diesel engine, fuel tank, counterweight, and hoses. The rest of the hydraulics remain the same. In fact, with a battery module harness retrofitted into the footprint of the engine, the electric conversion simply becomes a clean way to spin the machine’s hydraulic pump. One or more battery modules serve as a counterweight. And with the engine removed, mechanics will find it far easier to access the hydraulics for repair and maintenance.
With every machine converted, the value for owners, operators, rental firms, and distributors climbs because one standard battery module powers any machine, anywhere in the world. If the industry can move from focusing on selling electric machines to electrifying job sites and entire fleets, the industry will achieve a low carbon footprint in the most productive economical way.
Chris LaFleur is managing director of ZQuip.
STAY CONNECTED
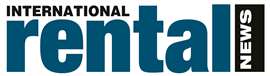


Receive the information you need when you need it through our world-leading magazines, newsletters and daily briefings.
CONNECT WITH THE TEAM
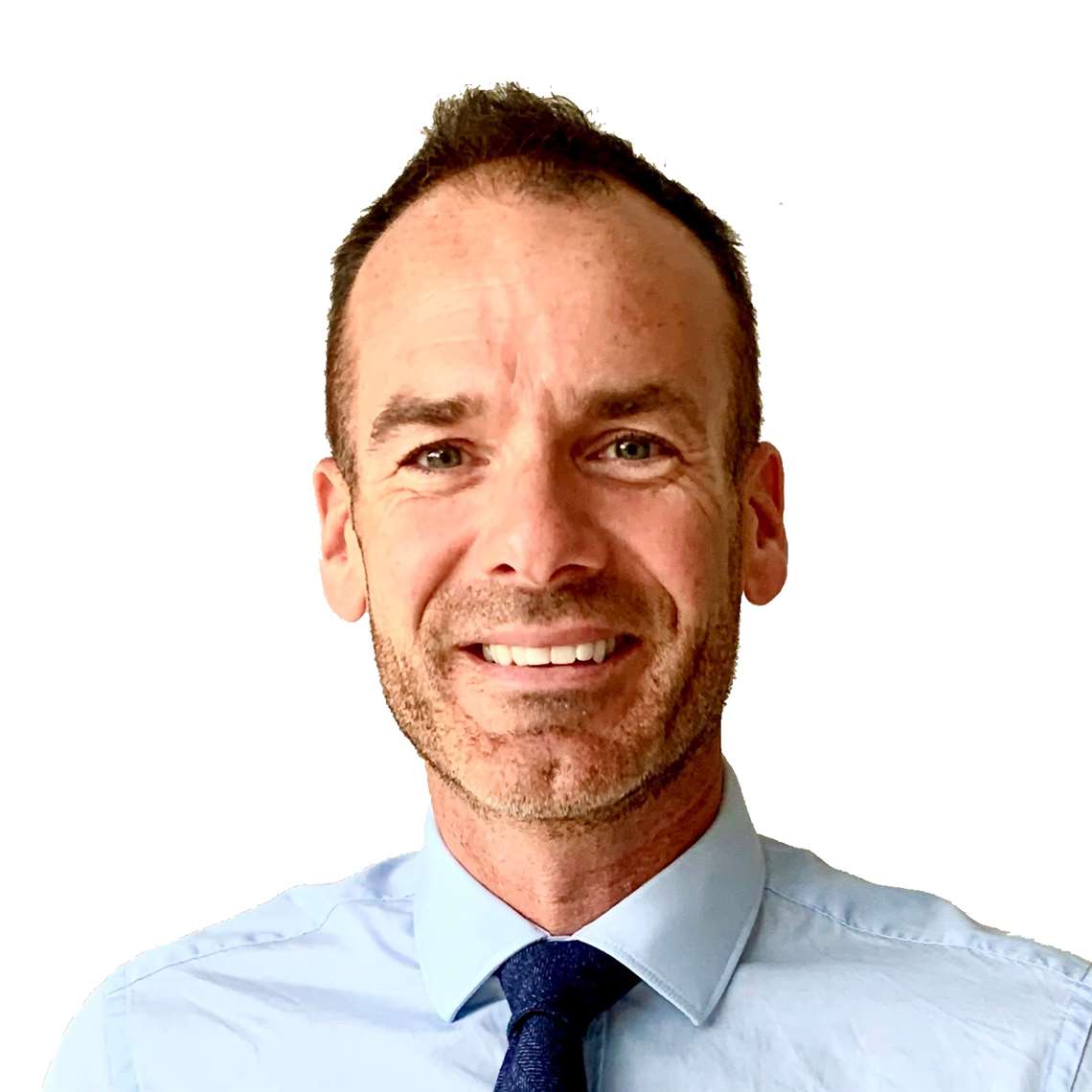
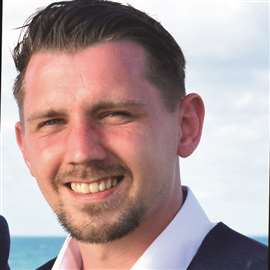