Inspection Gadget: The race to build AI apps for machinery inspections
10 March 2025
Tech firms are racing to come up with an app which can reliably inspect construction machinery for damage. Lucy Barnard speaks to Mark Turner, founder of Krank, which is set to unveil a second version of its Inspeq app at Bauma and finds out how it is targeting the rental sector.
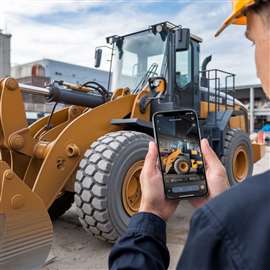
Imagine a future where you could use your smartphone to check the skid-steer loader you were about to buy had no significant engine damage or to generate a full inspection report when a customer returns a rented mini excavator to the depot.
That’s the vision behind a growing number of construction vehicle inspection apps which are currently being developed around the world in the belief that the traditional vehicle inspection process is ripe for innovation.
OEMs, start-ups and other contech firms are hoping that by combining large language models (LLMs) and other generative artificial intelligence, they can come up with a quick, easy, cheap and reliable way to use your phone to generate an inspection report for any piece of equipment and, eventually to spot damage.
Currently only in their infancy, vehicle inspection apps offer a vision of the future where rather than paying a mechanic to check if a machine is on its last legs, you can find out in just a few minutes on your mobile.
So far, however, the reality remains much more limited. Even the most advanced phone apps, only really provide an electronic checklist for machine operators to perform preventative maintenance checks and daily walk arounds.
Mark Turner is one of a growing number of entrepreneurs attempting to find a more sophisticated solution.
Having spent much of his early career selling and brokering large crawler cranes and construction equipment for F&M Mafco in the Middle East, Turner struggled to find an easy way to systematically organise the paper-based inspection reports required by clients when buying large fleets of equipment.
“Back then, the inspections themselves averaged around 45 minutes per crane,” Turner says. “But the real fatigue set in later. When I returned to the office or hotel after a long day’s work. I’d have to sit and complete the report, resize photos and file them correctly.”
As a result of that experience, Turner, who is now chief executive and founder of online equipment auctions site Krank, has spent a large part of the last few years helping to develop an app designed to help equipment inspectors speed up and simplify this process.
What does Inspeq do?
With the help of a team of 32 software developers based in Karachi, Pakistan, Turner has built Inspeq, an app which is currently available through Apple’s App Store and on Google Play. The app combines an AI automated transcription service with generative AI to enable an inspector walking around a vehicle to verbally go through a series of questions which the AI then can then transcribe that verbal description and order it into one of 20 standard inspection templates for a fleet buyer.
Using similar technology to the sort of automated voice systems banks use to help put telephone callers through to the correct service, the app offers prompts, and inspectors can complete their inspection in any sequence they like and then reorders it into the standard forms.
“To come up with a quick condition report, I just get my phone and start talking as I walk around,” says Turner. “I walk up to a machine, and I say, OK, so here I am in front of this Komatsu PC210 for example. And this is a 2022 model and I’m here in West Stow in Suffolk and since the weather is cloudy today, I haven’t got very good light.”
“And then I just walk around the machine, and I say the paintwork looks good,” he adds. “I can see there’s a damaged rear light here. Let’s jump into the cab and take a look at the meter reading. It’s got 7,000 hours on it. And at the same time the phone will give me prompts which we take from the report templates so then the AI pulls out all of the relevant bits and it starts filling out my report for me.”
And Turner says the tech is advancing rapidly, meaning that within a few months it should be capable of doing far more.
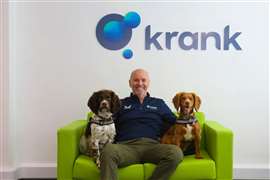
“So, we’re planning to launch version two at Bauma,” he says. “At the moment, the app doesn’t solve one major pain point which is taking photographs and video of the machine. You still have to take your report and then you have to go back and take your photos and videos.
“Version two will make it possible for you to issue a voice command to instruct the app to take a picture or video and timestamp it, so it appears in your report right next to the description. That’s a game changer.”
But, Turner says, even this version which can include pictures in a standard report is still a long way from his vision of the future. The ultimate goal for the app, he says, is for it to be able to recognize and quantify damage on a machine – something which would not only help potential purchasers identify problems but crucially which could be used by rental companies to complete the checking in and out of machines.
“So, recognising damage would be the next obvious step for us to take,” says Turner. “But it’s going to be V3. Already in V1 the AI understands some level of condition. So, if you say the paintwork is okay it will give it a fair rating based on what I’ve told it. Then, once we introduce imaging and video in V2 and the reports start coming in, then the AI will start to train itself further. Honestly, we’re probably about six months away from V3. It’s the next evolution.”
What could AI inspections do for rental companies?
Moreover, the company says that it is targeting rental companies in particular with the new app as it believes the new tech will soon be capable of understanding and comparing the condition of machines before they go out on hire and after they are returned. As such, Turner says the company is working with one major rental customer as a development partner.
“You can imagine, you’ve got a machine going out on rent. You take an inspection report and the customer signs off on it. When the machine comes back in you do another report and then the AI will generate a discrepancy report. We will programme the AI to understand a range or normal wear and tear on key components of the machines after consulting with our customers to arrive at that sort of range. And then the AI can potentially generate quotations for repair. So we’re creating that whole loop for the rental model.”
But will the tech really be able to spot the sort of concealed or complicated technical issues on a machine currently only visible to a skilled technician?
Turner says that like many AI applications, Inspeq is not being designed to replace the skills and knowledge of trained and experienced mechanics but rather to free them up to concentrate on the more technically demanding work.
“You still need human interaction, especially on more expensive pieces of equipment,” says Turner. “With something like a Cat D9, that costs you $300,000 you’re still going to want to have an expert inspector examine that.
“We’re probably now at about 85% accuracy for our transcription model but you still need an inspector to go through the missing blanks because it’s not a magic silver bullet. It won’t catch everything. But on the smaller stuff like a floor sander, you’re going to get to a point where the app will be automating that for sure.”
And the Inspeq team is not the only one working on developing an AI machine inspection app.
Apps such as Record360 focus on comparing before and after images of rental fleets. Others such as Snappii or workmule are designed to speed up pre-use safety inspections for plant equipment. And some major OEMs already offer mobile apps designed to help users check that their machines are working properly such as Caterpillar’s Cat®Inspect app.
Last year UK-based technology firm Spartan Solutions launched three AI-based co-pilots to help rental companies manage the quality of images taken of equipment, provide a predictive maintenance tool and improve text communication in its workshop and fleet management functions.
Nonetheless, Turner says that at the moment few other direct competitors are focusing on creating an app specifically designed for construction equipment inspections.
“We’ve got first mover advantage on this product but how long that lasts for is anyone’s guess,” he says. “This is something that is so fast moving. Like any AI model it will just keep improving itself. That’s what makes it so exciting and opens up so many possibilities.”
STAY CONNECTED
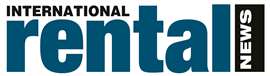


Receive the information you need when you need it through our world-leading magazines, newsletters and daily briefings.
CONNECT WITH THE TEAM
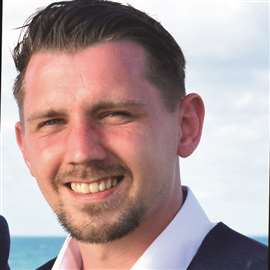

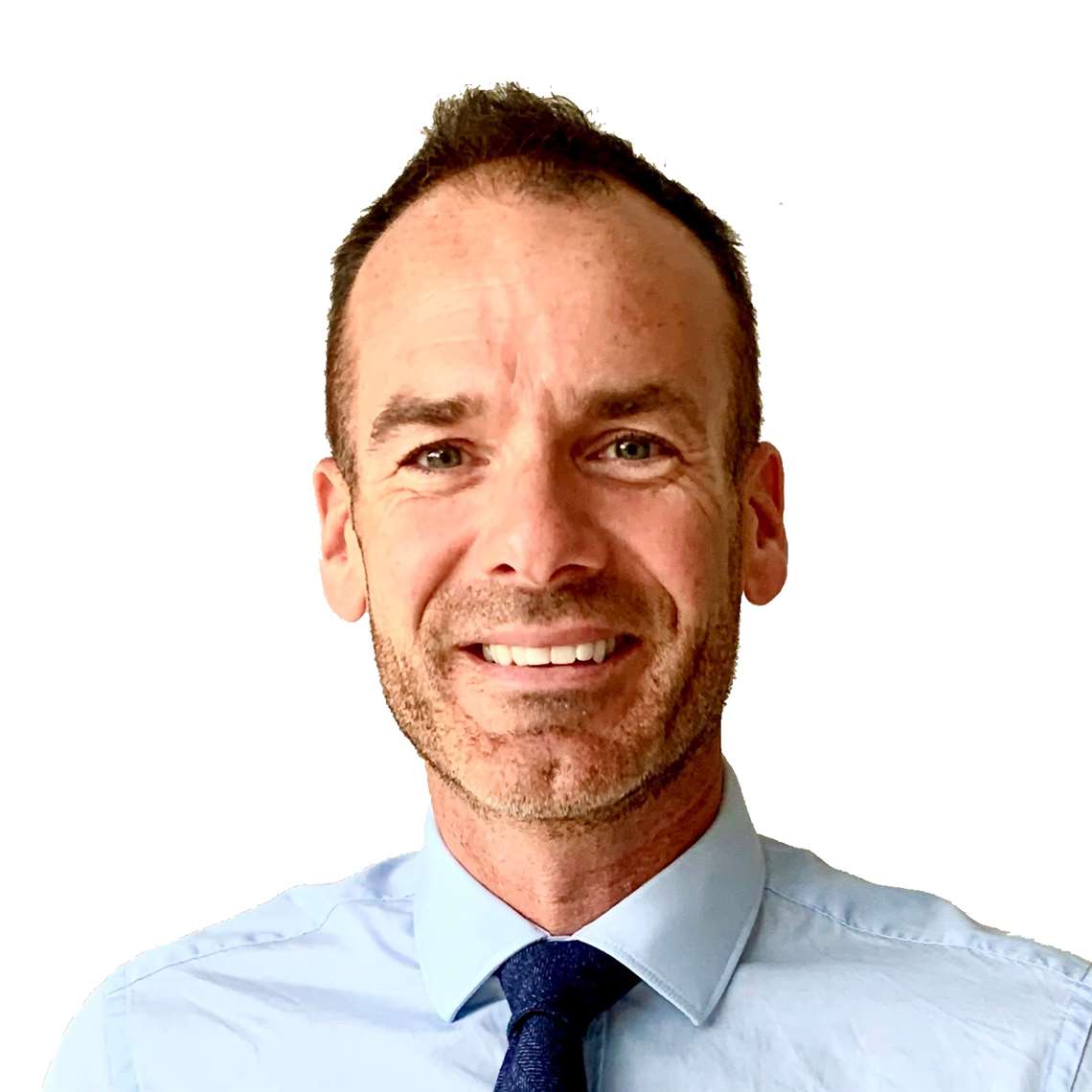