High flow: IRN looks at the pump rental sector
23 April 2014
Manufacturers and rental companies are investing in large pumps. IRN reports on new pump launches and some big application stories.
Sometimes having a range of large diesel driven pumps isn’t enough. That’s what BBA in the Netherlands has decided, with the manufacturer hoping to meet market demand for electrically driven pumps by developing a new range of electric models modified from its BA range of diesel units.
Using the same wet-ends and priming pumps used in its BA pumps, BBA changes the bearing block with a ‘modular’ norm block casting, creating a compact, electrically driven pump. The new range is available in sizes from 3 in up to 24 in, and with motor sizes of up to 250 kW. The new range of sewage and dewatering pumps have capacities ranging from 100 m3/hr up to 6500 m3/hr.
BBA product manager Henno Schothorst tells IRN that in addition to lower running costs, the electric units are much quieter than the diesel units and far cleaner as well. He says there are operational advantages too, because the frequency controlled electric motor allows the pump motor speed to be easily controlled. The controls can include pressure sensors in the sewer and remote monitoring and control is also possible.
The Netherlands-based company – which is offering a 4 year guarantee on all PT, BA and BE pumps sold from the factory after 1 January this year - says that because of their solids handling capabilities the new range will be ideal for both sewage and dewatering applications, and “ideal for the international rental market. The pumps can be used for sewer bypass pumping, flood control and other temporary setups.”
Mr Schothorst says BBA has been discussing the new range with its distributors worldwide and has been getting enquiries from markets including western Europe, Australia and Russia.
Pioneer Pump Solutions (PPS), the UK pump rental company established last year by Pioneer Pump, has expanded its fleet of pumps with the launch of the new 450SM sound attenuated, fully bunded pump, capable of flows in excess of 4000m3/hr or 16000 gallons a minute.
Designed and built by its sister company, Pioneer Pump Ltd, the first four pumpsets were delivered to the rental business as part of its expansion of ultra-high flow pumps that are used by water companies, power generation plants and contractors for applications where available space is restricted but high flows are required.
Kieran Gagg, general manager of PPS, “We have had a sizeable number of enquiries in 2013 from customers looking for combined flow rates of over 10000 m3/hr which would mean mobilising close to a dozen of our competitors pumps, multiple hose runs and extended set up times meaning their ability to respond to large flooding jobs was very challenging even for the largest companies.
“With four 450 mm pumps, powered by Volvo engines, we will be able to offer our customers three pumps plus a backup set capable of flows in excess of 10000 m3/hr and be set up within 24 hours, something previously unheard of in the UK market.”
The new pumpsets are powered by a 575 kW Volvo 1643 engine and drives the pump through a gearbox allowing the pump to operate very high flows with relatively low speeds.
Other features include integrated inline suction and discharge piping further reducing footprint; GSM telemetry for remote management; and integrated safety equipment such as spark arrestors and shutdown equipment for use in refineries.
Simon Ruffles, managing director of Pioneer Pump operations in the UK, said the development of the 450SM was “a milestone” in the UK pump sector; “firstly, no other company can design, manufacture and offer to rent such a large pumpset domestically. Secondly, it only took us 16 weeks from a blank sheet of paper to build and test it.”
He said “the days of having to mobilise larger numbers of smaller pumpsets are perhaps gone and so they should be. When organisations need large amounts of power they look for large generators not larger numbers of smaller units, the same strategy can now be applied to pumping equipment.”
Another UK manufacturer, Selwood Pumps – which has a long established pump rental business in the UK but focuses on sales outside the UK – has also been expanding its range of large pumps. In recent years it has been launching a new range of high head pumps, including the H100, H150 and, most recently, the H200, and is now redesigning its solids handling pumps.
Tony Killick, general manager of Selwood Pumps, tells IRN that the first new pump will be the 12 in S300, which is now in the final design stages. It will share components with the high head range, such as the bearing housing, and uses a Perkins 4 cylinder turbo engine rather than the larger, 6 cylinder Isuzu power plant used on the old model, which means lower fuel use and a more compact footprint.
Mr Killick says it will have the same performance at the original S300, namely a maximum head of 65 m, maximum flow of 1000 m3/hr, a 95 mm solids handling capability.
Regarding its UK rental fleet, Selwood is investing around £3 million on new pumps, comprising a mix of the new super silent solids handling pumps, hydraulic submersibles and the new high head pumps.
The rental operation recently had to respond quickly when two canister pumps failed at one of Anglian Water’s main sewage works. Selwood installed an overpumping system to replace the pumps, which are used to push settled sewage into aeration lanes.
With insufficient space for submersible pumps that could meet the 800 l/s capacity, Selwood instead placed two of its 12 in, super silent S300 pumps at ground level, with a further one on standby, and use flanged 12 in hoses running vertically up the end of the building and across the roof section.
Meanwhile in Stockholm, Sweden, pump manufacturer and rental company Zylem Inc has completed a massive sewer and stormwater bypass pumping installation as part of the city’s Arenastaden (or ‘Arena City’) project.
A new bridge, being built by contractor Peab, will link the Arena City to Stockholm’s Kolonnvägen district. The bypass operation was required because under one of the abutments of this new bridge run 75% of the water and wastewater pipes serving the Solna municipality of Stockholm.
To allow uninterrupted wastewater pumping during construction of the bridge, Xylem had to create a bypass pump system to replace existing sewer and storm water lines.
Erik Nordqvist, project manager for Xylem Sweden explains, “The challenge was to devise a system capable of dealing with extremely heavy flows of between 200 and 600 l/s. To manage this, we installed four of Xylem’ s powerful Godwin-brand diesel pumps; three with 150 mm inlet capacity and one with 250 mm inlet capacity. The bypass pumping system had to cover an area of 80 m which in turn required approximately 320 m of pipe.
“It was a significant area of ground to cover that also involved removing extensive surface water, which added to the already heavy flow of wastewater and created a challenging dewatering situation.
“To cope with this additional surface water we incorporated three of Xylem’s Flygt 3153 pumps into the system design, pumping the water to a container equipped with larger capacity Flygt 3202 pumps. These powerful pumps then transported the wastewater 180 yards away,” said Erik. Altogether 996 metres of pipes, in varying dimensions, were used as part of the bypass system.
“Each piece of pipe was three metres long and challenging to maneuver - a 12-inch pipe weighs about 80 kilograms” says Mr Nordqvist, “Peab assisted with the pipe-laying process and we had a good working relationship throughout the project.”
It took just three weeks to construct the bypass pumping system.
The pipe work was laid and pumps operational within one week, with pumping continuing for a period of two weeks while the new pipe and sewer system was being installed. Construction of the Arena City is due to be completed in 2015.
BOX STORY
SPP Pumps shifts gear
SPP Pumps can trace its history back to 1875 – the year that the UK business bought the rights to the Pulsometer Pump in the US – and in that time has seen a number of different owners.
The last 10 years, however, has been a period of continuity under present owner Kiloskar Brothers Ltd (KBL), the US$2.1 billion Indian business that is one of Asia’s largest manufacturers of centrifugal pumps. Over that period revenues at SPP have grown fivefold to around £65 million last year.
Much of this growth has come from non construction markets – SPP has been particularly successful in developing pump-driven fire protection systems for the building services market and for the offshore oil and gas sector.
The company still makes its Autoprime pumps that are popular in the construction and rental sphere, although that business is smaller now, with annual sales of around 100 units, than it was at the height of the construction boom, when it was selling 400 pumps a year.
“It’s a very popular pump in the business”, says Ken Winn, the ex-Siemens executive who joined last year as site director at SPP’s manufacturing centre in Coleford, UK, succeeding retiring director Terry Newby, “It’s one of the products that brought me here. It’s an important product for us and we have development projects ongoing.”
One of these is the creation of a pump modification system that will allow standard pumps to be transformed easily into solids handling units. This design is undergoing trials now before its full commercial launch later this year.
Another possibility – although one very much for the future – is for SPP to take on the range of submersible pumps produced by Kirloskar. There is a precedent for this kind of cooperation, with SPP’s industrial division now selling some KBL-made pumps.
SPP, although located in the heart of rural England, is an export oriented company, with around 60% of its sales to export markets. It has sales and service facilities worldwide, and continues to invest in these.
For example, SPP recently inaugurated a new facility in Atlanta, US, which is KBL’s seventh facility outside India. SPP says the new facility will boost production capacity by 30%, with revenues in North America expected to reach US$40 million in the next three years. Meanwhile in South Africa, KBL and SPP are this year to combine their existing plants at a single location in Johannesburg.
The owners have serious ambitions for the business. Alok Kirloskar, who is managing director of SPP Pumps, speaking last November on the 10th anniversary of the SPP acquisition, said the deal had represented a strategic move by KBL to increase its global footprint; “In the next decade we intend to double our market presence.”
BOX STORY
Thompson develops barge pump system
Thompson Pump, the Florida, US-based pump manufacturer and rental company, has developed a pumping system for use on flood control barges.
The Thompson Flood Control Barrier Pumping System, for which Thompson has received patent approval, uses a pumping arrangement powered by a single diesel engine to make it easy to float and submerge the barge without the need for multiple power sources.
Designed by the company’s vice president of engineering, Dale Conway, the set-up comprises a Thompson centrifugal pump, plus diesel engine and dry running oil-less vacuum pump priming system.
The pump transfers water into barge compartments when sinking, and reverses the process when the flood recedes and the barge is floated again. A hydraulic system controls a winch connected to the shoreline to position the barge in the waterway.
The pump is enclosed with a cage and lockable doors for maximum security, and comes equipped with a solar powered battery charger and built in control panel with automatic shutdown capabilities.
Thompson tells IRN that the special barges are tailor-built per project and are “multi-million dollar” systems that can take months or years to build and place on site. To date, four have been produced and deployed in Louisiana with several more planned for the future.
BOX STORY
Rental alliance
Pioneer Pump Solutions (PPS) and submersible pump rental company Hydrainer combined forces during the UK’s recent severe flood events to help prevent a potential 30000 gpm overflow at an important sewage treatment works.
Pioneer, which is now renting its diesel engine driven pumps in the UK as well as manufacturing and selling pumps, mobilised eight 200 SL high flow, 8 in solid handling pumps, plus hoses and accessories, within four hours, leaving six hours for setup and commissioning.
Kieran Gagg, general manager of PPS, who was directly involved in the overnight setup, said the team did an “outstanding job under very challenging conditions. Access to the site was restricted as was space, so being able to get our 200SL units which are capable of over 1000m3/hr each close enough to the site was the reason we designed and built these units - they offer large flows but are very light and compact.”
The 200SL pump is powered by JCB’s 444 turbocharged four cylinder engine. The pumps have on-board telemetry, integrated fuel tanks and sophisticated engine management systems.
STAY CONNECTED
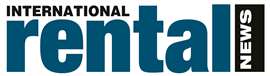


Receive the information you need when you need it through our world-leading magazines, newsletters and daily briefings.
CONNECT WITH THE TEAM
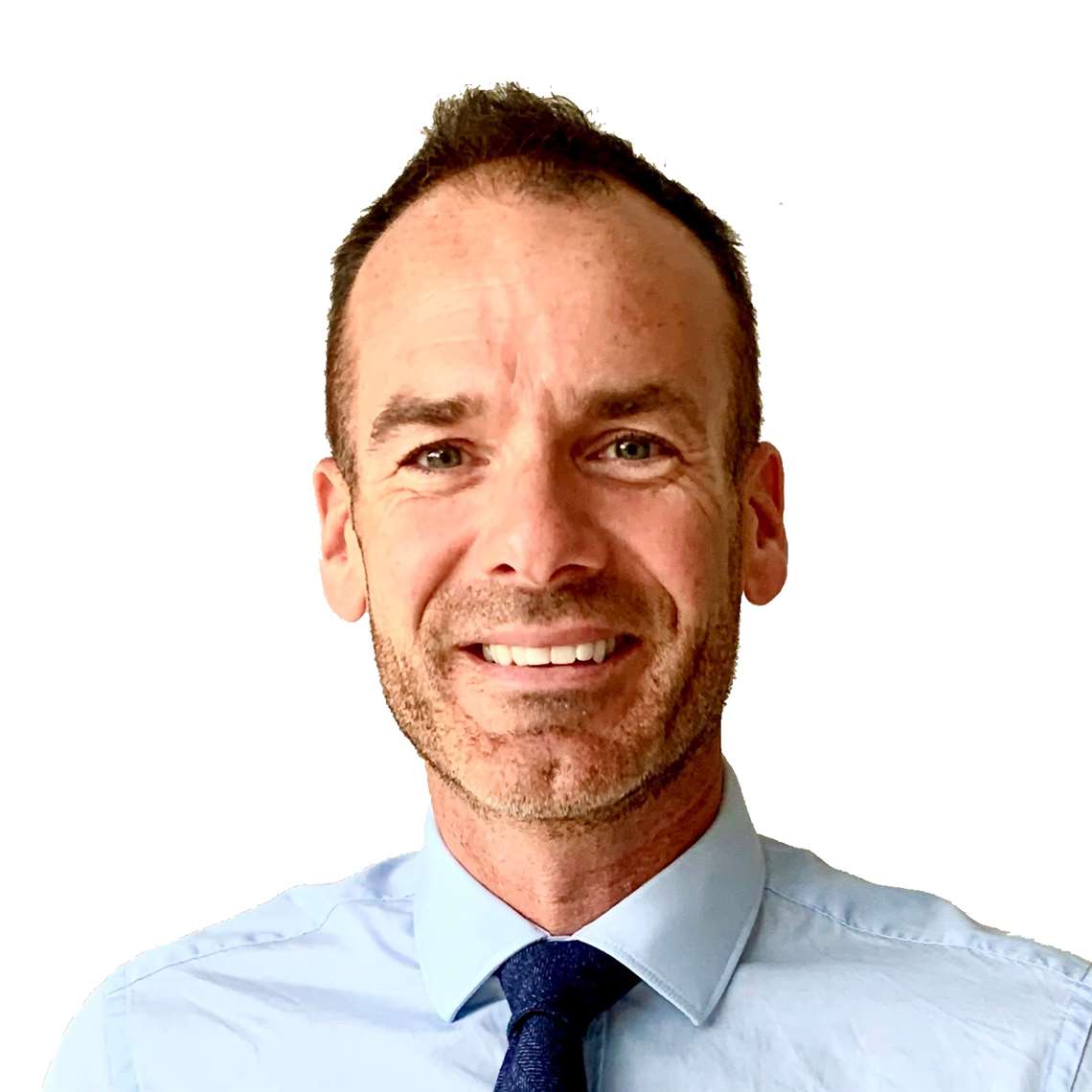
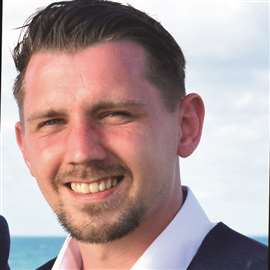