Interview: Caterpillar’s advancing quarrying technology
17 September 2023
As Europe gears up to meet its net zero challenge, it is simultaneously having to deal with an ongoing energy crisis and widespread inflation.

Suppliers of building materials are now reporting a general fall in demand and that means quarry owners are seeing their margins squeezed and must optimise efficiency to remain profitable.
With this in mind, Construction Europe spoke to Peter Sauter and Christian Berling, quarrying experts from Caterpillar, about how technology is being brought to bear on the sector, to help increase both efficiency and sustainability.
CE:
Are quarrying operations currently experiencing similar issues to general construction, or are the challenges in this sector different?
Peter Sauter:
“I think the nature of the business between quarrying and construction is quite different.
“In a quarry site, you have basically a factory without a roof.
You generally have the same processes – you start drilling, blasting, extraction, hauling, dumping into the crusher, screening, then you go to the yard. From there, the final material leaves the quarry site. So, basically, you have a repeating process, hour by hour, day by day.
“Because of this, you have long-term thinking. Quarry customers look for efficiency; ways they can improve the process. With every little change that improves the process, you have a high scalability. You’re repeating hundreds of times a day.
“For example, for truck loading, if you can make the operator a little bit more efficient – say 5 seconds for each truck load – you have scalability if you’re loading 100 trucks a day.
“In the construction business, you tend to have smaller jobsites, which are constantly changing, and they don’t have the same repetitive processes.”
CE:
Do these repeating processes and the potential for scalability make quarries good places to utilise technology?
Peter Sauter:
“We certainly see right now the importance of measuring the material flow. On all our equipment, starting from the load area, we have payload systems – on the excavator, the wheel loader, the truck, as well as the yard, when the material is leaving the quarry.
“If you can measure production, it allows you to avoid overloading or underloading the trucks.
“A quarry customer wants to ensure trucks are loaded to the maximum, because, if you’re underloading trucks, you’re losing efficiency, which means higher costs per tonne.
“Even more important than having the exact payload measurements, though, is that the site manager gets all the information.
“Typically, we are connecting the site and, especially in quarries, we go one step further with VisionLink® Productivity so assets are connected and site managers can analyse performance across job sites, making decisions to improve productivity.
“You can see when machines are running and when they’re idling, and you get all the fuel information – vital information for a site manager.
“The site manager can see how long on average it takes to load a truck. You can also see if there’s a truck with a target payload of 65 tonnes, if it gets underloaded – if it’s at 60 tonnes or 58 tonnes – you can see something is going wrong and can investigate. Using technology, the manager can visualise it like a bell curve; you can see the distribution and the load time, and if there is an excessive load time, he knows something is going wrong. Within VisionLink Productivity, there is a cost dashboard that allows the user to see the working and idle costs broken down by individual machine or job site.
“It’s actionable information from VisionLink Productivity.
CE:
Is this sort of technology being generally adopted in European quarries, or is there still some resistance from those who prefer more traditional methods?
Peter Sauter:
“Now the younger generation is getting into management positions and they are much more data driven than maybe previous generations.

“New systems can show so much information, basically in real time; this helps a lot to enhance efficiency in a quarry site.
For example, machine utilisation: one big element is idle time, and we can show the overall idle ration and drill down one level to see that the overall idle ratio is, let’s say, 40%.
“Maybe you don’t know if that’s good or bad, but you want to see where you have excessive idle.
“We can display the idle segment, especially long idle events, which are larger than nine minutes; that’s something you certainly don’t want to see on your site.
“Each idle event is GPS located, so we can show on a map where excessive idling is happening; is it happening at the crusher, when you’re dumping, at the loading area, or somewhere else?
“This is vital information for a site manager.”
CE:
How do you convince quarry customers of the benefits of your technology?
Christian Berling:
“I like to compare industries; to show them [quarry businesses] which other industries have already made the move into technology.
“A good example is the harbour industry. Here we also have repetitive flows and traditionally a lot of handwork, but today I would say we have a fully automated process, thanks to the container.
“Coming now to the discussion of a quarry owner, they have worked for 50 years in a very traditional way. Honestly, nothing has really changed; there’s still a machine loading a truck, which brings material to the crusher and dumps.
“We may have improved the efficiency or changed the equipment, and we can move more tonnes with fewer people, but the process is the same.
“Using technology – especially remote control – in some areas requires adaptation, but we really see this as a key change we can make in terms of efficiency.”
CE:
Exactly how does using remote control technology improve efficiency in a quarry?

Christian Berling:
“We learned during many customer discussions and site assessments that, in some applications in a quarry – overburden transportation, for example – you still have some kind of idling time on the loading tool or on the dozer on the landfill.
“When the trucks arrive, they are coming loaded, then they dump and the dozer pushes the material off.
“Here, we really see the benefit of non-line-of-site remote control, where you can switch between the assets with the click of a button
If you have a loader and an excavator, loading the overburden material, there are maybe two or three trucks travelling back and forth over maybe 15 or 20 minutes.
“So, there is some time when the excavator is idling, waiting for the next coming truck, and this time can sometimes be quite significant.
If you have a 40-tonne truck dumping, then you push it [the dumped material] with the dozer, that might be two-and-a-half or three pushes to get the load down the hill. So maybe the operator works for two-and-a-half or three minutes, then it’s done.
“Here we see the benefit of switching, with one operator who loads the truck first, the truck then runs to the landfill. Then the operator switches to the dozer and pushes the material down.”
CE:
So, this has a benefit, both in terms of manpower and fuel saving?
Christian Berling:

“It’s equipment utilisation, it’s fuel consumption; if the machine stays there in idling mode, you have a 500 horsepower diesel engine running to cool down the cab, that costs a lot of money and produces greenhouse gases, etc.
“Safety of course is another issue; if you take operators out of the cab, that’s a huge safety benefit.
“And then there’s employee efficiency, which I would connect to the challenge we all have in finding operators.
“It’s a big challenge in every application, so it’s good if we can build a better environment for an operator; I would say a more advanced and efficient environment which could also appeal to a new generation of operators.
“Now, with all the assistance systems we already have – I would not say you could put anyone in a station – that would be wrong – but this might be motivation for someone to join the quarry industry.”
STAY CONNECTED
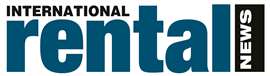


Receive the information you need when you need it through our world-leading magazines, newsletters and daily briefings.
CONNECT WITH THE TEAM
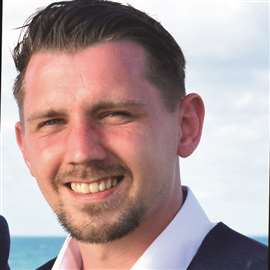

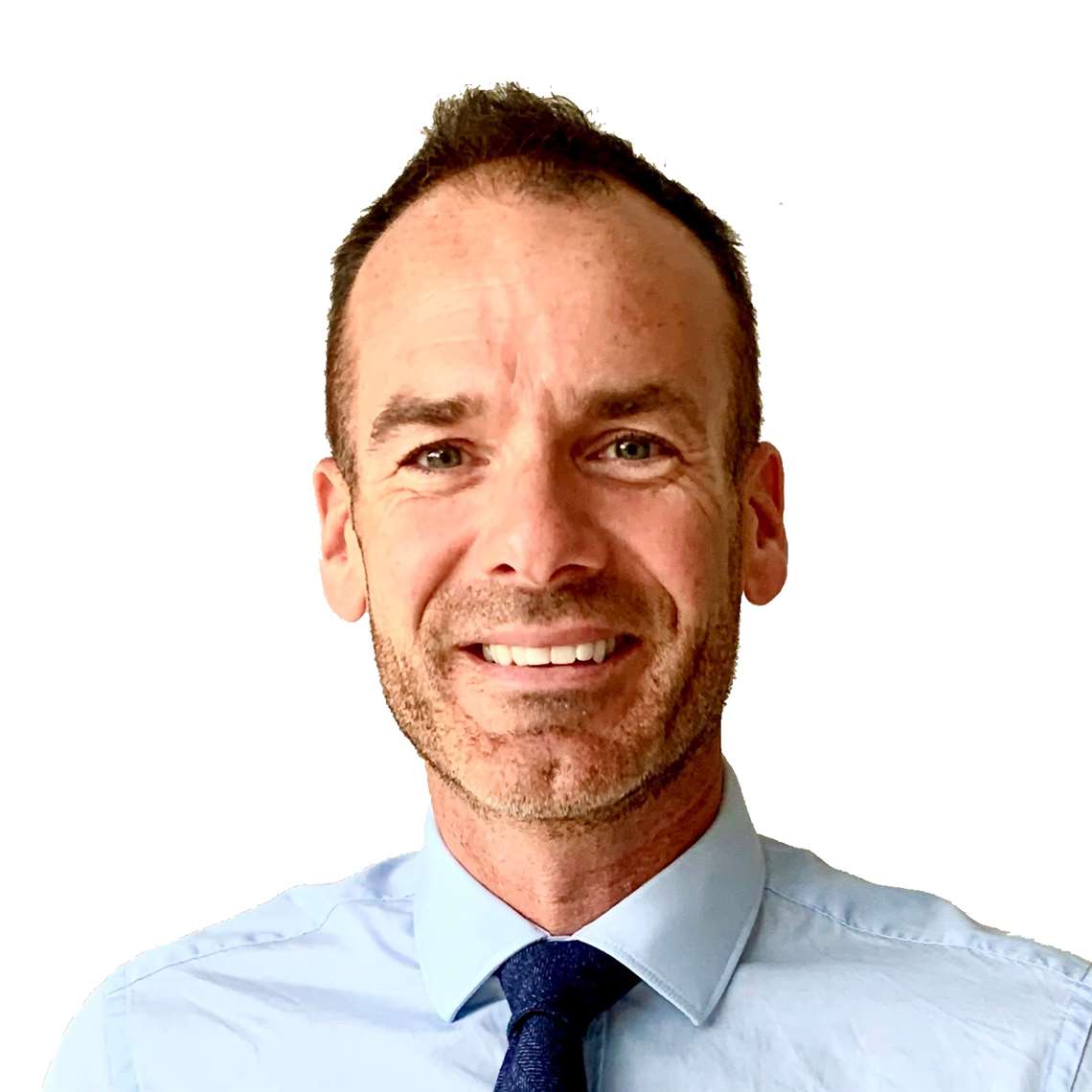