The rise of robotics in the access industry
03 April 2023
How close are we to a truly automated robotic aerial lift, and what projects are underway to get us there?

One of the big takeaways from the ConExpo show in Las Vegas during March, was that the era of driverless machines is drawing closer. In some sectors, this is already a reality – mining has had automated trucks for over a decade, for example.
But that technology looks set to start working its way into the wider construction market, with several manufacturers showcasing their automated machines.
Bobcat unveiled its Rogue X autonomous loader concept at the show, which the manufacturer said “explores the idea of operating where humans cannot go”. The machine does not feature a cab and Matt Sagaser, director of innovation accelerated at Bobcat said it “sets a framework for what is possible. Our team is just getting started on what is next”.
So, it seems, the construction world is starting to talk with the same level of enthusiasm about automated equipment as it did about alternative fuels to diesel some year ago. Lithium batteries are now a reality, particularly in the access sector, and hydrogen is taking real strides.
When will aerial lift robots enter the market?
But how far are autonomous, robotic aerial lifts away from becoming a reality?
There have already been a few steps in this direction. Last year JLG Industries announced a partnership with US-based RE2 Robotics to initially produce a remote-controlled aerial lift, with no basket, to install solar panels.
The project represented the first real move towards autonomous aerial lifts, and in this case helps solve the problem associated with finding skilled labour at a remote location, along with offering safety and productivity advantages.
The partnership came about after RE2 was awarded a project by the US Department of Energy to develop a robotic solar field construction system to manipulate solar photovoltaic panels.
The result is the integration of the RE2 Sapien 6M robotic arm, along with its RE2 Detect and RE2 Intellect software, with a JLG aerial platform. Once completed, the unit will transfer, lift and place the photovoltaic modules.
“It is a bridge to autonomy,” says Rob Messina, JLG’s senior VP of product development, “which is [currently] aspirational. But we’ve seen over the last five years, a tremendous number of companies try to mature technology in the autonomy space.”
A collaborative approach to collaborative robots
In February this year, Terex Corp., Genie’s parent company, announced it has made an equity investment in Apptronik, an Austin, Texas, company specializing in the development of mobile robotic systems.
“Multiple trends are converging to drive adoption of human-centered robots in everyday applications and Apptronik is well positioned to capitalize on this emerging trend,” said Terex Chairman and CEO John L. Garrison, Jr.

Apptronik’s co-founders have worked on advanced human-centered systems including the NASA Valkyrie Robot for the DARPA Robotics Challenge.
Speaking to AI in March, just after the deal was struck, Simon Meester, president of Genie, said, “We are very excited about the partnership.”
He believes the truly autonomous aerial lift is a reality of the future and Genie, alongside Apptronik, is working towards that in two-, five- and ten-year stages. Meester added that this should result in prototypes being introduced in the next couple of years.
And there are some very real issues now that may require the process to be hastened. “I’m not saying it is something that will happen tomorrow,” says Meester. But he adds, “We do believe labour will become even more of a scarce resource and we believe at some point it will make sense to have a robotic solution.”
As Meester points out, “The aerials industry is more closely affiliated to robotics than we may think.”
A boom lift is already robotic in the sense that the arm is remotely operated, “It’s just that a human is currently required for the last stage and the degrees of freedom needed [for that].”
However, Meester is keen to point out that ultimately it comes down to value to the customer. “We want to make sure we bring technology not just because we can but because it makes sense for cost of ownership and productivity for our customers.
“We could bring something out tomorrow - we just don’t think it will be meaningful to them.”
Telematics data and artificial intelligence
Another big take away from ConExpo was telematics. Telematics is nothing new but at ConExpo, not only were the telematics systems on display able to access data from different equipment manufacturers, but almost all contained information on carbon footprint.
In addition, new technology in construction has ever-higher levels of artificial intelligence.
We are already seeing how AI can improve process and operations but at ConExpo we got a glimpse of a future where AI interacts with BIM and digital twins models as well as the actual construction equipment itself on the site.
As David Swan, vice president of products at telematics specialist Trackunit, says, the next step in the journey towards truly autonomous lifts is happening now through machine learning trending and advanced analytics of the productivity of a fleet.
“When we look at machine learning and artificial intelligence it’s about being able to have automated assessment of performance of the fleet and being able to benchmark that against other fleets.”
Over the next 12 to 18 months Trackunit aims to release features that allow fleet owners a quick automated analysis of different groups of units in their fleet, compare it to the wider industry and provide solutions to improve productivity.
The Internet of Robotic Things
After that connectivity is the necessary foundation for us to then take the next step. While the Internet of Things (IoT) is becoming more and more commonplace in the industry and refers to the transfer of data between connected smart devices, the Internet of Robotic Things (IoRT) concerns additional aspects; primarily the ability to make decisions and the physical interaction with objects in the real world.
Swan says, “The first step of connectivity is being able to remotely see what the machine is doing. When we talk about robotics, it is then understanding what the machine is doing without being there - understanding the environment without being there.
“The third phase of that is having a full picture of the machine’s behaviour. You can’t have a machine mysteriously doing its own thing - you have to have that constant connection.”
Once we fully understand the data, adds Swan, we are in a good place to, for example, attach a glazing robot to install windows at the end of a large boom without putting people in the vicinity at risk.
The most likely first step for robotic equipment is having an operator overseeing a machine or a group of machines, says Swan.
The barrier to a truly autonomous artificially intelligent lift is the three dimensios it operates in. “If you look at autonomous driving, which is already a very hard problem to solve – you are really just operating on a two dimensional plain.
Swan explains, “When you look at what a lift does on a jobsite, you have the chassis that’s moving around in a various graded jobsite, you have a boom doing a complex range of motions through its envelopes, then you have a person on the end of the boom that is also doing complex movements with their hands. It’s all happening in a 3D space at different speeds.”
The company is already having conversations with its customers to combine rich data connectivity with integrated video or sensors. “Of course, that’s leading down the path that the steers in that robotics direction.”
Another baby step is around two-way communication with a machine - adjusting the machine’s parameters and potentially the firmwear. “Now we’re looking at the machine, understanding where it is, what the environment is, what the recent activity is and taking actions remotely like limiting the reach and speed or updating firmware remotely.
“That’s something we are actively working on to release in the fairly short term. You can kind of see how that is a little brick on the road towards that.”
Robotic aerial lifts and artificial intelligence

Early last year Robotics specialist nLink launched a robotic aerial lift that is combined with artificial intelligence to initially be used for high pressure washing applications.
Based on a Genie S-80 J boom lift, provided by MEWP distributor Hybeko, the RoboLift can be used without an operator.
The first phase of the project, which was completed in the autumn of 2021, showed that it was possible to build a robot that performs facade cleaning. Based on the boom lift, a robot arm was developed to hold a high-pressure washer. The arm is programmed to perform the washing movements.
The company is now in the process of phase two, to find out where RoboLift is best used in terms of customers’ value chains and workflow. Funds have been allocated for phase two, which includes market analysis and technology adaptations.
STAY CONNECTED
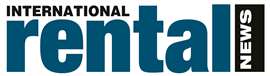


Receive the information you need when you need it through our world-leading magazines, newsletters and daily briefings.
CONNECT WITH THE TEAM
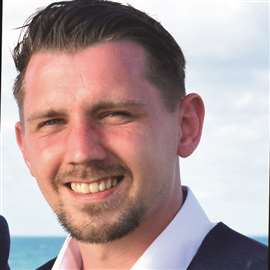

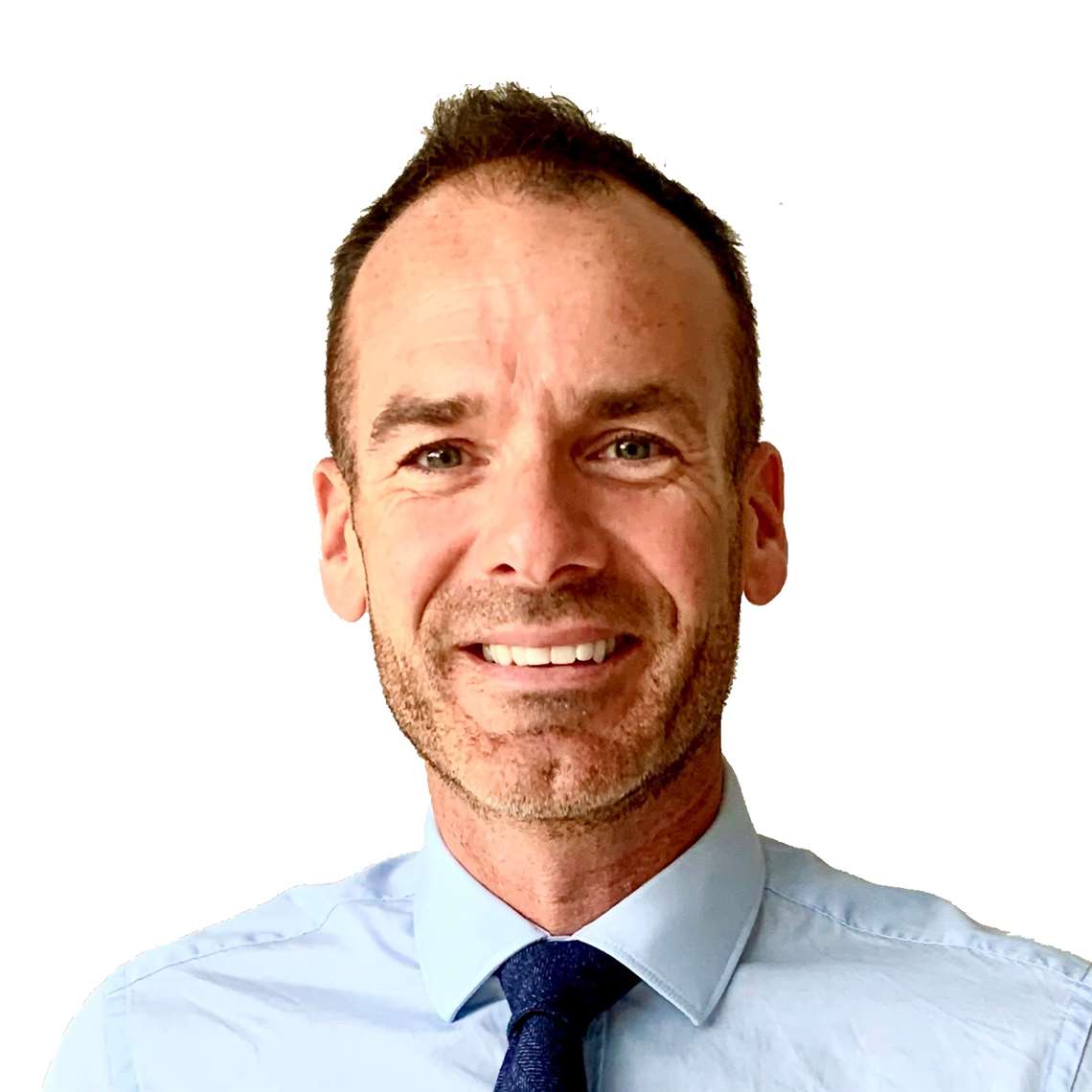