Fehmarnbelt: the technology behind the world’s longest immersed tube tunnel
09 March 2023
Historically, immersed tube tunnels (IMTs) have been seen as a third option behind bridges and bored tunnels, but the record-breaking €7.1bn Fehmarnbelt Tunnel is helping to change all that. Construction Europe’s Lucy Barnard looks at the cutting edge technology being used to build the world’s longest IMT.
Visible for miles around as clusters of orange tower cranes and huge yellow excavators standing out against the long grey mudflats topped with January snow and the greyer waters of the Baltic Sea, construction work is in full swing on the Fehmarnbelt Tunnel, a road and rail mega tunnel set to connect Demark and Germany.
Jens Ole Kaslund, technical director at Femern A/S – the body charged with building the 18km long tunnel – nods enthusiastically when asked about the challenges involved in such a project.

“We will be beating two world records by constructing the world’s longest immersed tunnel and the world’s longest combined road and rail tunnel,” he says proudly. “That is in itself an impressive construction and engineering achievement.”
With construction of the record-breaking €7.1bn project now heading into its third year and scheduled to be completed in 2029, engineers around the world will be watching progress with interest, eager to see further applications for the construction techniques and technologies being put into practice in the Fehmarnbelt.
Kaslund, a former project director at Danish rail group Banedanmark, has been working on the project for the last five years and has had overall responsibility for its success since 2019. He says he jumped at the chance of taking the role at the specially-created subsidiary of state-owned Danish transport company Sund & Bælt.
“When I got the opportunity to be part of this amazing project and be part of connecting Scandinavia and central Europe with the longest immersed tunnel in world, I was not a second in doubt,” he grins.
Immersed tunnels
Used since the 1890s as a quick and cheap way of building channels for transport and utilities under rivers and harbours, immersed tube tunnels have historically been seen as a third-choice option for most major infrastructure projects, behind bridges and bored tunnels.

Certainly, the Danish government, which is providing the lion’s share of the development funding, initially planned to complete the rail and road link via a striking cable-stayed bridge similar to the Øresund Bridge, to the east of the country, which connects Denmark with Sweden via a combined railway and motorway bridge, and which opened in 2000.
However, as design teams started to consider the plans in detail, they began to worry that any structure built across the 18km Fehmarn Strait would be vulnerable to prevailing east-west winds and would create a high risk of shipping collisions.
A second option, which would have been drilling under the sea floor using a tunnel boring machine (TBM) similar to the Channel Tunnel between Britain and France, was also ruled out because the seabed was deemed unsuitable for drilling. The depths involved would have made it difficult for high speed trains to get across without significantly expanding the length of the tunnel and the requirements for dual track train and motorway shafts would have necessitated the use of multiple TBMs, making the project much more expensive.
Instead, in 2011, the design teams finally opted to build an immersed tube tunnel (IMT), an undersea tunnel comprising prefabricated segments fitted together. This is the type of tunnel used for the 4,050m Drogden Tunnel which forms part of the Øresund crossing, linking an artificial island at the end of the bridge with Amager Island in Denmark.
“The immersed tunnel solution has many advantages,” Kaslund says. “It is economically more feasible; a tunnel is not affected by weather; it can be constructed almost without interfering with the extensive [shipping] traffic through the Fehmarnbelt; the environmental impact on marine life is less; and we have a lot of experience with immersed tunnels from other Danish projects such as the Øresund Link and Storebælt link. Further, the immersed tunnel was evaluated to be less risky compared to a bridge solution.”

Technically challenging
Less risky it may be, but the project comes with its own set of technical challenges. For one thing, there is the scale: the tunnel will be nearly three times longer than the IMT section of the Hong Kong-Zuhai–Macau Fixed Link, currently the longest tube tunnel in the world,
To build such an enormous project, Femern A/S has spent two years preparing the site, constructing a specially built harbour capable of receiving up to 80,000 tonnes of material deliveries each week, accommodation for 1,300 workers and, even more impressively, the world’s largest tunnel factory where the concrete tunnel sections will be made.
Client: Femern A/S, a specially-created subsidiary of Danish state-owned transport company Sund & Bælt.
Contractors: Fehmarn Belt Contractors (FBC), a joint venture between Boskalis and Van Oord has been conducting the main dredging and marine work. The Fehmarn Link Contractors (FLC) consortium, which includes Vinci, BAM, Per Aarsleff, Wayss & Freytag Ingenieurbau and Max Bögl Stiftung, has been constructing the tunnel, the portal buildings, the casting factory and workers accommodation since January 2021.
Cost: The Fehmarnbelt link’s overall financial framework of DKK 55.1 billion (€7.1bn) was determined in the 2015 Construction Act. Of this, DKK 7.3 billion is reserves.
Tunnel size: The tunnel will have a 17.6km immersed section and will be 42 meters wide. Its foundation depths will reach more than 40 meters below sea level. It will comprise five tubes: two 2-lane motorways for cars; two electrified rail tunnels; and one emergency corridor.
Construction timing: Enabling works started on the project on the Danish side in 2020 and the German side in 2021. Dredging of the tunnel trench and construction of the factory began in 2021. The first tunnel segment is expected to be laid before summer 2024 and the project is scheduled to complete in 2029.
This facility, which is currently undergoing its finishing touches, is located close to what will be the Danish tunnel entrance in Rødbyhavn, and is set to be the biggest factory building in Denmark. It will eventually cover around 1 million square metres and have six production lines on which 89 huge tunnel sections, each 220m long and 40m wide and weighing a whopping 73,000 tonnes, will be cast. Divided into three production halls, currently Hall B is 95% complete with its first production line ready to start casting the first segment. Halls A and C meanwhile are expected to be finished later this year.
The elements will be cast step-by-step in segments of approximately 24m in the factory. Because the tunnel sections are so big, they will actually be made in pieces so that each standard element will be made up of nine segments.
To reduce both construction time and complexity, Kaslund says the design team attempted to produce the largest sections feasibly possible, which they could cast safely in one sitting without risk of cracks, based on experience from other immersed tunnel projects and similar casting technology on other projects.
And, for the plan to work, each massive segment must be made in the factory to exactly the right specifications.

Concrete casting
Each segment is cast from layers of concrete built up on top of each other in a manner Kaslund likens to “baking an enormous advanced cake.”
Casting each segment according to a detailed plan takes 36 hours of continuous pouring and can be painstaking as workers must ensure that the concrete is exactly the right temperature and consistency – not too cold, not too hot, not too wet and not too dry - before moving on to the next layer and the next.
“The greatest challenge lies in ensuring the quality of the casting,” Kaslund says. “Each element comprises nine segments and each segment needs precision in the casting. The production of the element is done in a climate-controlled environment to ensure the highest quality possible.”
In fact, the tunnel elements are so large that there is no facility big enough to store them, meaning that as soon as each one is completed it must be taken out to sea and installed straight away.

With so much at stake during the casting, Kaslund and his team have opted to try out the process by having a couple of trial runs. To do this they have built a massive test bed facility where they have had a go at prefabricating blocks containing one and a half rail tube segments.
During the final months of 2022 they completed two blocks of 1½ rail tube segments, ensuring that casting, concrete, formworks, quality and other important details are exactly the same as they will be in the real segments. Kaslund says the team is “still reviewing the results.”
Dredging work
Out in the Fehmarn Belt, dredging work on the tunnel trench has been in progress since mid-2021 and is 70% complete. This work is due to finnish next year to enable the first tunnel segment to be laid in the trench before summer 2024.
The contract for dredging and ground reclamation was awarded in 2016 to Fehmarn Belt Contractors (FBC), a joint venture between Dutch dredging specialists Van Oord and Boskalis.
So far, the dredging team has already come up against a number of unusual challenges, including navigating their way around the wreck of a seventeenth century Danish warship and an unexploded second world war bomb.
A fleet of up to nine different dredgers has been pressed into action on the project. Vox Amalia, a Trailing Suction Hopper Dredge (TSHD) - which entered service for Van Oord in March 2020 - acts like a giant, floating vacuum cleaner, hoovering up debris and transporting it has taken on the bulk of the work. She has been assisted by Fetsy and Manta, two barges purchased by FBC and mounted with specialist Liebherr and Mteck cranes for lifting heavy boulders.
In total, the dredging will result in around 19 million cubic meters of sand, stone and soil, which will be used to build a new 300-hectare beach near Rødbyhavn.

Placing the segments
Once a complete tunnel segment has been manufactured in the factory, it will be rolled out and taken to an upper basin where it will be fitted with temporary steel bulkheads at both ends to make it watertight and ensure it floats.
Huge doors will close behind it, allowing the basin to then be flooded with water – rather like a lock on a canal. This will allow tugboats to move each section down to the lower basin and then out to sea.
For the crews on the tugboats the challenge is clear – positioning each 217m 73,500 tonne floating concrete tunnel segment in exactly the right spot so that when its ballast tanks are flooded with water, each element will sink 40m to the seabed, landing in the dredged trench next to one another and within 15mm of its target.
“We demand a high degree of precision,” agrees Kaslund. “We are talking about kilometre-long distances, so when we dig the tunnel trench and place the individual elements, even small deviations along the way can have great significance. Our work must be extremely precise, so when the last element is placed, we need an accuracy of very few millimetres.”

To achieve this, Kaslund says the construction team has developed its own “unique GPS-system” which relies on the latest technology to improve GPS accuracy from the typical range of several metres used in mobile phones and cars to an accuracy of 8mm horizontally and 15mm vertically.
The system is being supplied by Danish company Geoteam, which won an EU tender to supply the reference network for the project in spring 2020. It works by boosting the satellite signals available in the construction area by installing 10 stationary terrestrial Global Navigation Satellite Systems stations (GNSS stations).
As anyone using a modern car SatNav system knows only too well, satellite signals to Earth can be weak and quickly run into disturbances, leading to inaccuracies. The GNSS stations, which are located on both the Danish and German sides of the Fehmarn Belt, correct for errors in the satellite signals so that construction machinery and ships can navigate with high accuracy. (Four of the stations have been built by Femern A/S and six by Geoteam.)

Kaslund says that by eliminating these errors, the positioning system can provide tugboat teams with the exact coordinates necessary to lower the tunnel segments into position.
So far that hasn’t been tested for real because the first tunnel segments are expected to be placed later this year. However, Kaslund says that the system has already been used for more than a year by the construction equipment that is helping to build the 500,000 square metre work port.
Gina gasket solution
Kaslund says that during the manufacturing process, one end of each tunnel segment is mounted with a Gina gasket, which is a huge hollow vulcanised rubber fitting designed to sit around the entire end of the segment.
In a process which has changed little over the past 70 years, the Gina gasket is then used to connect the segments forming a watertight seal.
Once an element has been laid in the trench, it is coupled together with the adjacent segment and pulled against it using hydraulic jacks. As the elements are brought together the gasket squashes around the join, forming a small reservoir between the two steel bulkheads. The construction team then gets to work pumping the water out of this reservoir which makes the water pressure on the other end of the element compress the Gina profile which seals the joint.
Later a second rubber seal, known as an Omega seal, is then clamped across the joint on the inside of the tunnel and, once the pressure between the Gina and Omega seals has been tested, the temporary bulkheads are removed.
“At the start of the project we evaluated several possible solutions to improve the existing [Gina] joint technology but we did not find solutions superior to the well-known technology developed slightly from the 1950s,” Kaslund says. “Also the size of the tunnel project was assessed to be too long to try a new technology before testing it in smaller scale.”
The process continues until all the elements are in place. Then, Kaslund says, they will be secured in the tunnel trench with gravel and sand and covered with a protective layer of stone which will be level with the existing seabed.
Once that is complete, the construction team can begin work on the tunnel’s technical and mechanical installations such as railway tracks, ventilation, cameras, communication systems, signage and painting, which then must be thoroughly tested before the tunnel’s expected opening date of mid-2029.

+100 year design life
Kaslund says that once in operation, the Fehmarnbelt Tunnel has been designed to be used for well over a century, justifying the €7.1bn cost.
Femern A/S hopes to recoup that cash by charging car drivers a toll – likely to be set at close to the rate for the ferry crossing, which is currently around €100.
And, by halving journey times between Scandinavia and Central Europe, Femern predicts that the tunnel will be so popular that it could be $4bn in profit after just 50 years.
By providing a viable ‘green’ alternative to flying, the tunnel can also justify the huge carbon cost involved in its creation. And, as technology continues to evolve to include more powerful EV batteries and electrified roads that recharge cars’ batteries as they drive, Kaslund predicts that demand could be even greater.
“The tunnel will be built to last at least 120 years so the project will pay itself back CO2-wise many times over in its lifespan,” he says.
“This is based on today’s technology in the car fleet and the ferries and our traffic model prognosis. New developments of transportation technology within the next 10-20 years such as e-roads would therefore have a positive effect on the payback time.”
STAY CONNECTED
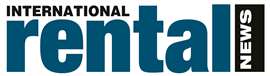


Receive the information you need when you need it through our world-leading magazines, newsletters and daily briefings.
CONNECT WITH THE TEAM
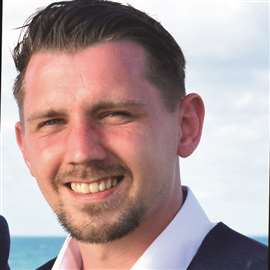

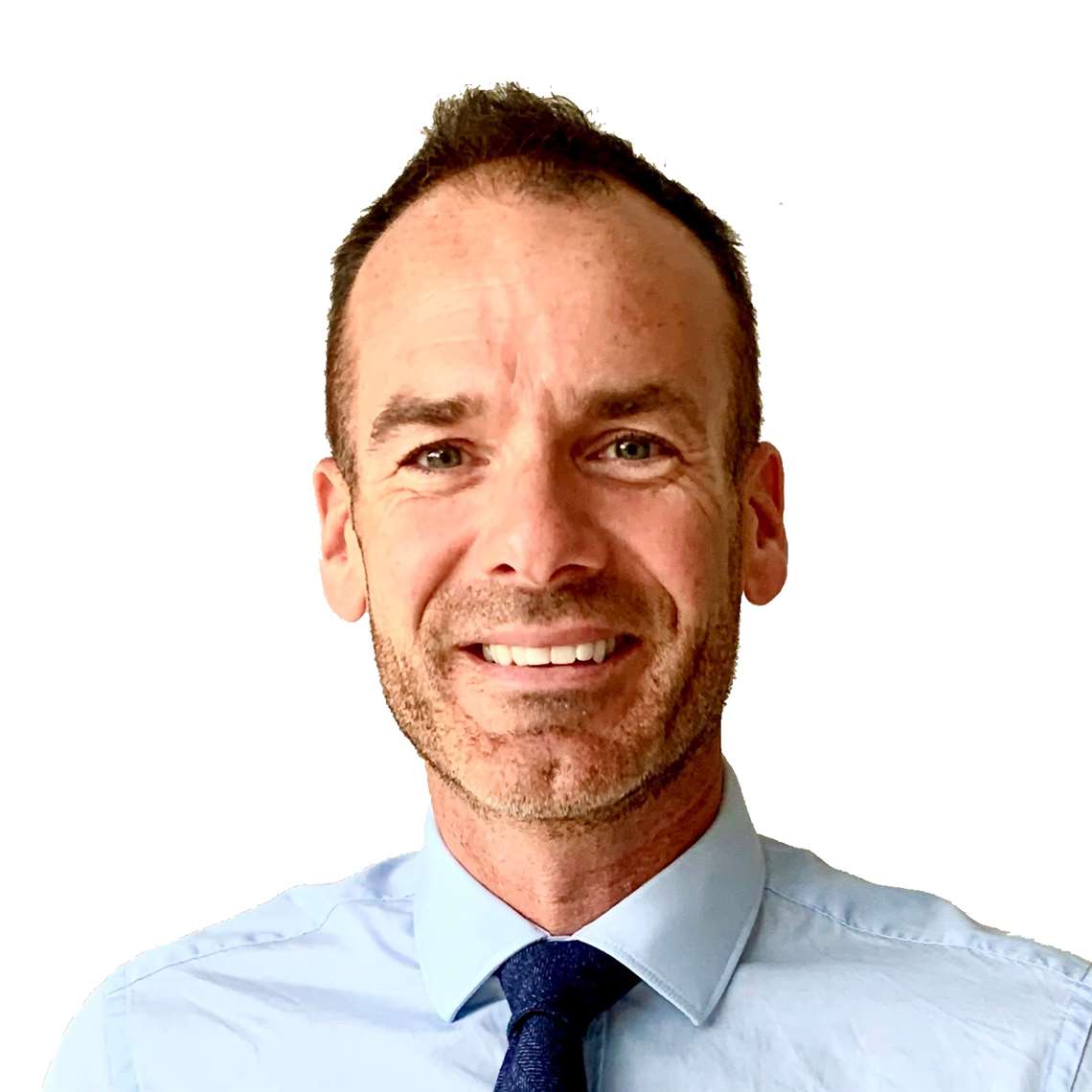