Interview: Equipment Depot on its secret to safety
14 June 2024
US-based material handling and equipment rental company Equipment Depot recently celebrated its best safety record in its history, highlighting a company-wide commitment to the goal of lowering its Total Recordable Incident Rate (TRIR) to zero.
This past year, the warehouse solutions provider broke its own record, achieving a TRIR of 1.27, which is more than 3x lower than the industry average of 3.9, the company said.
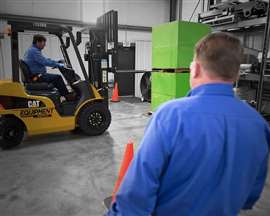
With over 50 branches coast to coast, Equipment Depot announced the achievement this June, which marks the 28th annual National Safety Month, a yearly event spearheaded by the National Safety Council to build awareness of the leading causes of preventable injuries and fatalities in the workplace.
Championing the company’s milestone is Jonathan Pledger, vice president of human resources and safety & training at Equipment Depot, a group company of Mitsubishi Logisnext that offers brands such as Cat lift trucks, Mitsubishi forklift trucks, and Jungheinrich, while providing new and used forklifts, aerial lifts, service, parts, equipment rentals, financing, and automation solutions.
“We are the company we are today because of our dedication to our ‘safety-first’ mission,” Pledger said. “For an 85-year-old company to reach this level confirms that our team members actively strive to create a safer work environment for themselves and others—and I can’t be prouder.
“Our people are at the heart of our company. That’s why we have a motto: Make sure people go home better than the way they came to work. The health, safety, and well-being of our staff and their families, and our customers have always been and will continue to be our top priority.”
We talked with Pledger about Equipment Depot’s approach to safety, and here’s what he had to say.
Rental Briefing: How would you describe Equipment Depot’s safety philosophy?
Pledger: At the core of our philosophy is the belief that all accidents can and should be avoided. We achieve that by discovering unsafe conditions and rectifying them before the opportunity is there for someone to actually get injured.
If you believe some accidents are inevitable, you’re already starting off on the wrong foot. Our overall philosophy is that all accidents should be avoided. We don’t want any of our people to get injured, whether it’s a small injury or a major recordable incident.
I tell my managers quite often, it’s okay to be tough when it comes to safety. We’re responsible for making sure our teams are able to go home safely.
Finally, the most important thing we can do for ourselves and for our teammates is to keep each other safe. Safety is everyone’s job and it’s all of our responsibility.
Rental Briefing: What methods do you use to make sure your staff understands and is executing that philosophy?
Pledger: It starts with local management. Direct supervisors and managers have regular team meetings and generally have at least one safety topic in any gathering they have. We have monthly, OSHA-mandated safety courses that people must complete as well.
Every time we have any type of leadership conversation or meeting, we make sure we talk about safety first.
I think we do a pretty good job, but of course, we always need to get better.
Rental Briefing: What inspires Equipment Depot’s safety philosophy?
Pledger: When I came to the company a little over five years ago, I could see safety was embedded into the company’s culture.
Our technicians are human beings - fathers, mothers, sons, daughters, brothers, sisters - and our leadership team made sure people understood the company really cares about them personally.
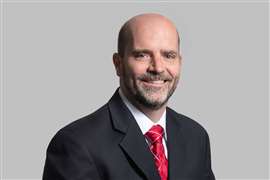
This isn’t a “safety is good business” message, as in, when someone gets hurt, that costs the company a lot of money, etc. That is a reality, but our employees know that it’s not about the bottom line. It’s about the people and keeping them safe.
Our new president, Anthony Garcia, has a lot of knowledge and a ton of interest in getting into the details of safety, doing audits and talking to technicians. His commitment goes beyond just caring to actually engaging with safety on a practical level.
Rental Briefing: How did the company achieve its best safety record in the company’s history?
Pledger: OSHA’s TRIR is measured by calendar year and is based on the number of hours worked versus the number of recordable injuries. Our TRIR was 1.27 last year; the year before it was 1.85.
Things definitely continue to evolve. We’re doing a better job with operator safety training, making sure that takes place within the first few days of employment. There are things we continue to do to improve.
One of the things that made last year’s accomplishment even better, is that we’ve continued to grow through acquisitions and integrating new employees, new sets of technicians. Being able to do that and at the same time, continue to bring that TRIR down. This is a big accomplishment.
One of the most important factors was getting our Environment, Health & Safety (EHS) teams back out in the field with our teams on a regular basis. That’s one of the things we had struggled to do because of Covid travel restrictions and a lot of people working remote. But it’s so critical to get the experts out there.
Rental Briefing: What is Equipment Depot doing that’s different from other companies? What’s the secret?
Pledger: I can’t speak to what other companies may or may not be doing, but I do know it’s critical that every employee understands and believes they can make a difference with safety.
One of the key things we’re trying to get even better at is ensuring our employees know they have work-stop authority. That means if they’re ever in a situation where they feel they’re unsafe, or at risk of getting hurt, they have the authority to stop.
We have a good safety record, and we have a really good team and I think we have a good philosophy and a good culture. But our safety management system was way outdated. So now we’re in the process of rolling out a new cloud-based safety management system that will enable us to do a lot of the things we want to do in real time, versus, through paper, emails and spreadsheets.
We’ve launched this in two of our operating companies over the last two months, and throughout this year, we’re going to be bringing that out to the rest of the organization.
One of the key features is we’ve created a behavior-based field management safety observation audit. All of our managers are going to be responsible, all the way up to our vice presidents and president, to actually go out and do a behavior-based safety observation with each of our people.
One of the main objectives is to be able to observe a risk before an incident happens, and do something about it immediately. With the system we’re launching, let’s say you see a trip hazard. All you need to do is open the app, take a picture of the hazard, and it automatically sets the GPS to that location and dispatches it to the appropriate people, who can then work on getting the problem resolved in real time.
The goal is to get to zero incidents. We’re using technology to be able to accelerate the rate at which we’re able to deal with unsafe situations.
The ability the software is going to give us to engage all levels of management in behavior-based safety is a big step forward for us. It’s not that people were disengaged before, we’re simply enabling them to be engaged in a more meaningful way.
STAY CONNECTED
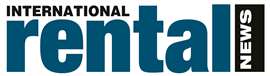


Receive the information you need when you need it through our world-leading magazines, newsletters and daily briefings.
CONNECT WITH THE TEAM
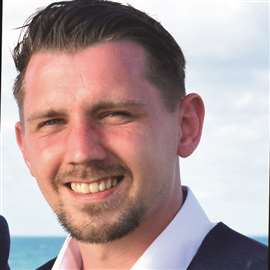

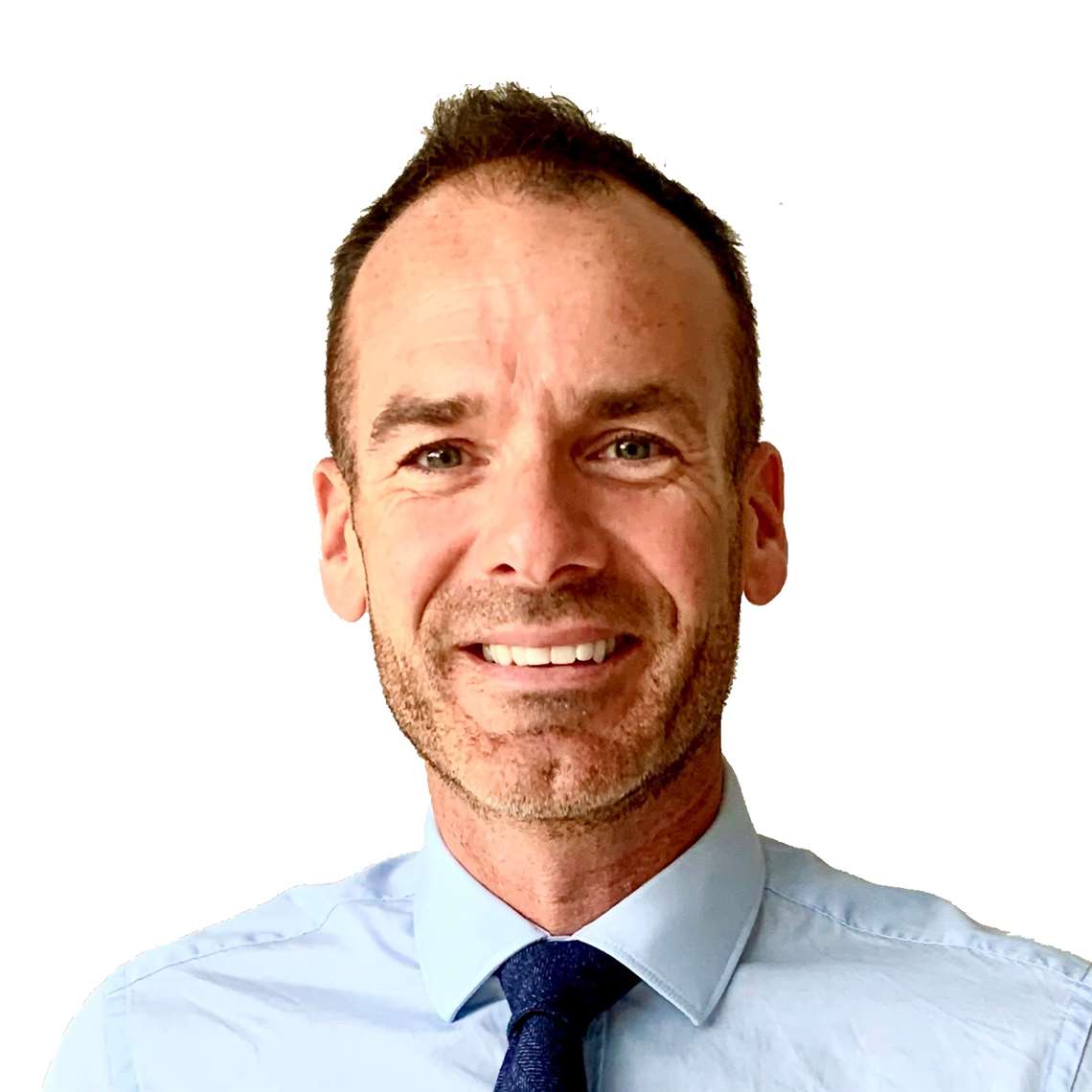