One for all: Standardizing battery-powered equipment on job sites
15 July 2024
Stefan Pfetsch, managing director of Wacker Neuson, reveals all on the company’s collaboration with competitors on a standardized, cross-platform battery for construction equipment.
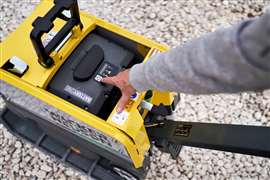
The dream for any owner of battery-powered equipment is to have an agnostic battery platform that can be used on various units, bringing cost benefits and compatibility across the entire fleet.
In 2021, a collaboration between construction OEMs aimed to achieve this dream with the launch of Battery One, a manufacturer-independent swappable battery compatible with machines from various manufacturers.
The collaboration began when road construction equipment manufacturer Bomag approached its German competitor Wacker Neuson.
Since then, companies such as Swepac, Dynapac, Mikasa and Wacker Neuson’s Spanish subsidiary Enar have all joined.
Speaking to IRN about the progress of the initiative, Stefan Pfetsch, managing director of Wacker Neuson, said that after completing the initial stages of designing and refining the units, the focus has now shifted on increasing the number of OEMs offering the batteries as well as scaling up the production line.
“Prior to Bauma 2022, we had to design the machines to be fit for Battery One, but since Bauma, it has been about ramping up production and the manufacturers that offer Battery One in terms of knowledge and training for servicing to make them ready to launch the product into the market.”
He says initial feedback since launching has been positive, with the ease of use, lower maintenance and longer lifespan benefits the main drivers behind demand from customers, alongside emissions reduction.
The batteries, manufactured in Poland and Germany, are available in three sizes: 500Wh, 1000Wh, and 1400Wh. A standard 13.5A charger enables recharging to 80% in 70 to 200 minutes or to 100% in 90 to 255 minutes.
“They lend themselves to light equipment,” Pfetsch says, with typical applications including rammers, plates and internal vibrators.
“In terms of power output, it’s about 3kW, but we can drive an equivalent of approx. 5kW on a gasoline engine because the energy efficiency on electric drive trains is much higher and no transmission like V-Belts is needed.
“There’s also light equipment with higher power demand which we are currently not able to power, but we are working on it.”
Higher power units
Pfetsch suggests that higher power units could be shown at the next Bauma and be available between 2025 and 2028, “We want to increase the capacity and runtime of the battery, but we also want to increase the power that we can supply,” he says.
“If we are able to power up to 5kW equivalent of an internal combustion engine, down the road we would like to power 10kW. Then you would probably power most of the light equipment category.”
Pfetsch goes on to say that believes the technology is in place to support this increase but expects it to take time to “fulfil certain regulations,” which is the “most demanding part of the development.”
Meanwhile, he says that in the future Battery One could also be used in other compact units such as excavators and loaders, though it is not something stakeholders are actively pursuing.
Of course, collaboration among competitors is rare, so why did the companies decide to work together? When asked, Pfetsch reveals that Wacker Neuson was already working on something similar before being approached by Bomag.
He says, “Regulations have been known for quite some time, and this was one of the major motivational points to really get into battery-powered products,” he says. “What’s really important is that we are trying to make it as easy as possible for the end user.
“The more these batteries are made widely available, independent from a manufacturer, the higher the acceptance from the end user.
“How long I can run my machine with a battery, how difficult it is to recharge the battery, and how difficult it is in terms of usage are all things we need to overcome in the early stages of transition. If there’s too much insecurity with the customer, they might revert to diesel.”
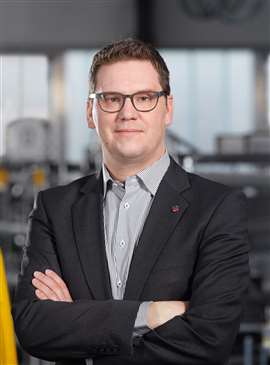
Acceptance of battery-powered equipment in construction
“The most difficult to convince is the end user,” he says. “You have to make it easy for them. That’s what we do in a direct sales organization.
“For example, in Germany, we let customers trial machines, we give them a rammer with the battery, and I would say the rate of having a success is rather high.
“But to get to the point that they trial the battery, other questions need to be solved. For example, standardization is one key question, as well as energy management charging and transportation of batteries.
“We have some answers, but not the full range of answers, and those are things I’m not sure one company would be able to solve. One step, of course, with standardization is that you embrace your competitors.”
And then there is of course the previously mentioned issues around runtime anxiety, charging and usage.
Driving adoption through telematics
A relatively new addition to the Battery One offering can take away some of the apprehension, he says.
Earlier this year the company added telematics to the battery, enabling users to connect wirelessly from their phone via Bluetooth connectivity.
“That monitors almost everything,” Pfetsch says. “You can read out the state of health, state of charge, how many cycles the battery has gone through, the machines the battery was used with, the average run time of the battery and the application of the machine you have been using.”
Looking ahead, he says the goal by the end of the year is to have “everyone fully committed to Battery One,” meaning all units would be Battery One branded, no matter which company uses them.
Wacker Neuson will also look to increase the number of units it produces that use Battery One. At the time of writing the company has more than 20,000 batteries on the market, with more than half of that number Battery One branded.
Meanwhile, more than half of the Wacker Neuson portfolio of equipment comprises of battery-powered equipment.
This, he says, the company will also look to steadily increase in the near future; “By 2030, our goal is to have 100% electrified alternatives available, and I think we are on a good track in that regard. The goal is also to have them all being able to run with Battery One batteries.”
STAY CONNECTED
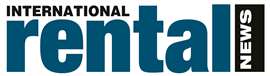


Receive the information you need when you need it through our world-leading magazines, newsletters and daily briefings.
CONNECT WITH THE TEAM
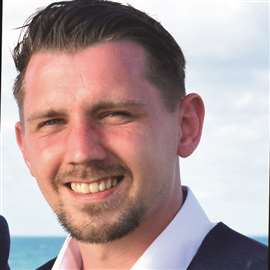

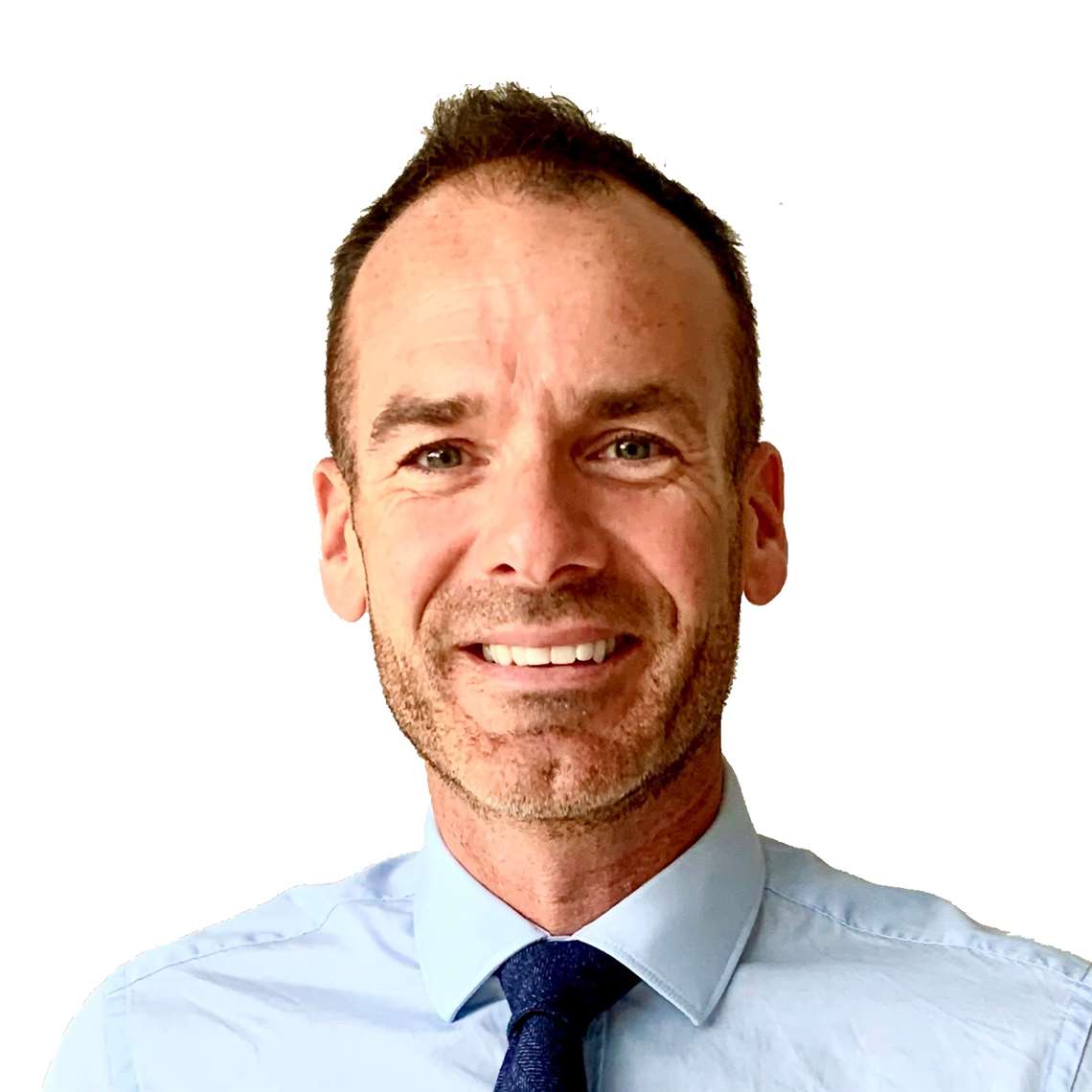